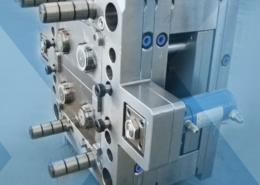
The Craft of Plastics: The Art and Science of Plastic Molding
Author:gly Date: 2024-06-01
In the world of manufacturing, plastic molding stands as a cornerstone process, shaping the future of countless products and industries. From the smallest household items to the largest industrial components, plastic molding plays a pivotal role in creating the objects that define our modern world. This article delves into the art and science of plastic molding, exploring its intricacies, applications, and the ever-evolving technology that drives it forward.
1. The Basics of Plastic Molding
Plastic molding is a manufacturing process that involves shaping plastic materials into desired forms using heat and pressure. The most common types of plastic molding include injection molding, compression molding, extrusion molding, and blow molding. Each of these techniques has its unique advantages and is suitable for different types of plastics and applications.
Injection Molding**: This is the most widely used plastic molding technique. It involves injecting molten plastic into a mold cavity under high pressure, where it cools and solidifies to form the desired shape. Injection molding is ideal for creating complex parts in large volumes with high precision.
Compression Molding**: In this process, plastic material is placed into a preheated mold cavity and compressed under heat and pressure to shape it. Compression molding is often used for thermosetting plastics, which cannot be reheated repeatedly like thermoplastics.
Extrusion Molding**: This process involves forcing molten plastic through a die to create continuous profiles such as pipes, rods, or sheets. Extrusion molding is used for producing long, continuous plastic parts.
Blow Molding**: Blow molding is primarily used for creating hollow plastic parts like bottles, containers, and pipes. It involves inflating a plastic parison (a preformed blob of plastic) within a mold cavity to create the desired shape.
2. Materials Used in Plastic Molding
The choice of plastic material is crucial in plastic molding. The most commonly used plastics for molding include thermoplastics and thermosetting plastics. Thermoplastics, such as polyethylene, polypropylene, and polystyrene, can be reheated and remolded repeatedly. On the other hand, thermosetting plastics, such as epoxy and phenolic resins, become permanently set when heated and cannot be reheated.
3. Applications of Plastic Molding
Plastic molding finds applications across diverse industries, including automotive, consumer electronics, medical, packaging, and more. In the automotive industry, plastic molding is used to create lightweight, durable parts like dashboards, door panels, and bumpers. In consumer electronics, plastic molding is essential for producing cases, buttons, and connectors. The medical industry relies on plastic molding for creating surgical instruments, implants, and disposable medical devices.
4. Advances in Plastic Molding Technology
With the ever-evolving landscape of manufacturing technology, plastic molding is also experiencing significant advancements. 3D printing, a form of additive manufacturing, has revolutionized the plastic molding industry. It allows for the creation of complex shapes and geometries that were previously difficult or impossible to achieve using traditional molding techniques. Additionally, the integration of advanced materials, such as composites and nanomaterials, has enhanced the performance and durability of plastic-molded parts.
5. Environmental Considerations
Despite its widespread use, plastic molding has its environmental implications. The disposal of plastic waste is a significant challenge, and recycling efforts are ongoing. However, the industry is also responding with sustainable practices, such as using bioplastics derived from renewable resources and implementing circular economy principles to reduce waste and improve resource efficiency.
Conclusion
Plastic molding, a crucial process in modern manufacturing, combines the art of design with the science of materials and technology. Its versatility, precision, and cost-effectivenesss have made it an indispensable tool in creating the products that shape our world. As technology continues to evolve, the future of plastic molding looks even more promising, with advances in materials, processes, and sustainability efforts leading the way.
GETTING A QUOTE WITH LK-MOULD IS FREE AND SIMPLE.
FIND MORE OF OUR SERVICES:
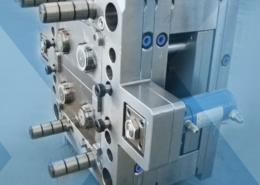
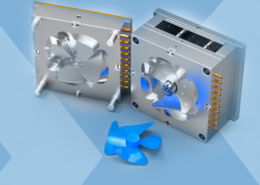
Plastic Molding
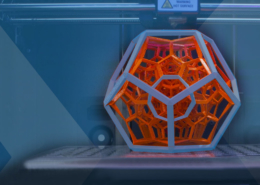
Rapid Prototyping
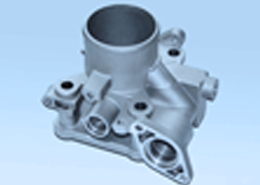
Pressure Die Casting
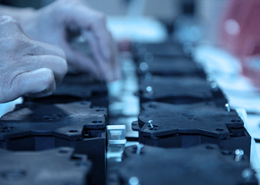
Parts Assembly
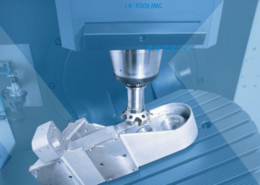