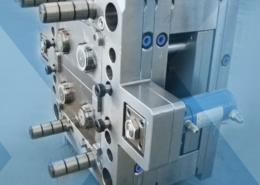
The Essentials of Plastic Injection: A Comprehensive Guide
Author:gly Date: 2024-06-01
Plastic injection, a fundamental process in the manufacturing industry, has revolutionized the way we produce everyday items ranging from small parts to large components. This article aims to provide a comprehensive understanding of plastic injection, its working principles, essential components, and best practices.
Introduction to Plastic Injection
Plastic injection molding is a manufacturing process that involves the injection of molten plastic into a mold cavity under high pressure. The mold, typically made of metal, is designed to give the desired shape to the plastic as it cools and solidifies. This process is highly versatile and can be used to produce a wide range of products, from simple to complex geometries.
Working Principles of Plastic Injection
The plastic injection molding process typically follows these steps:
1. Material Preparation: The raw material, usually pellets of plastic, is loaded into the injection molding machine.
2. Melting and MixingInside the machine, the pellets are heated to their melting point, mixed, and homogenized to ensure uniform composition.
3. Injection: The molten plastic is then injected into the mold cavity through a runner system under high pressure.
4. Cooling and Solidification: The mold is cooled to allow the plastic to solidify and take the desired shape.
5. Ejection and Trimming: Once cooled, the molded part is ejected from the mold and may require further trimming or finishing.
Essential Components of a Plastic Injection Molding Machine**
1. Injection Unit: Responsible for melting and injecting the plastic into the mold.
2. Clamping Unit: Closes and holds the mold securely during the injection process.
3. Control Unit: Regulates the entire process, including temperature, pressure, and timing.
4. Mold: The heart of the process, designed to give the desired shape to the plastic.
5. Runner System: Directs the flow of molten plastic from the injection unit to the mold cavity.
Best Practices in Plastic Injection Molding
1. Material Selection: Choose the right plastic material based on the desired properties, such as strength, durability, and cost.
2. Mold Design: Ensure the mold design is optimized for efficient filling, cooling, and ejection.
3. Process Control: Maintain strict control over temperature, pressure, and timing to ensure consistent product quality.
4. Quality Assurance: Implement robust quality assurance procedures to detect and correct any defects or inconsistencies.
5. Sustainability: Consider the environmental impact of the materials and processes used, aiming for more sustainable practices.
Applications of Plastic Injection Molding**
Plastic injection molding finds applications across various industries, including automotive, electronics, packaging, medical devices, and consumer goods. Its ability to produce parts with complex geometries, high precision, and repeatability makes it an ideal choice for mass production.
Conclusion
Plastic injection molding is a fundamental process in modern manufacturing, enabling the production of a wide range of products. Understanding its working principles, essential components, and best practices is crucial for achieving consistent product quality and maximizing efficiency. As we move forward, sustainable practices and innovative material developments will further enhance the capabilities of plastic injection molding, opening up new opportunities in various industries.
GETTING A QUOTE WITH LK-MOULD IS FREE AND SIMPLE.
FIND MORE OF OUR SERVICES:
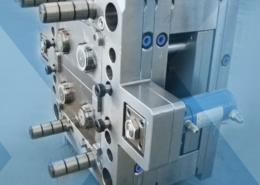
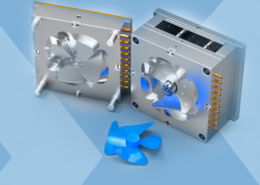
Plastic Molding
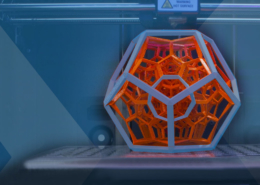
Rapid Prototyping
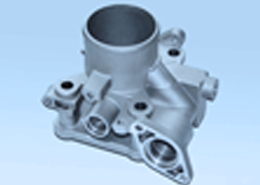
Pressure Die Casting
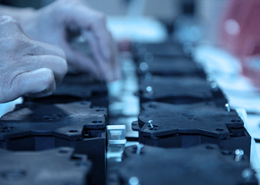
Parts Assembly
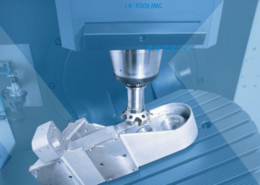