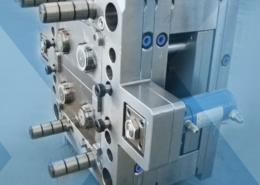
The Essential Guide to Plastic Injection Molding Services
Author:gly Date: 2024-06-01
In the world of manufacturing, plastic injection molding services occupy a pivotal position, offering a range of benefits that make it an ideal choice for producing a wide variety of parts and components. This article aims to provide a comprehensive understanding of plastic injection molding services, discussing their importance, applications, benefits, and the factors to consider when selecting a service provider.
What is Plastic Injection Molding?
Plastic injection molding is a manufacturing process that involves injecting molten plastic into a mold cavity to form a desired shape or part. The process begins with the melting of plastic granules in a heated barrel, which are then injected under high pressure into a mold. The mold, which is specifically designed to create the desired shape, is cooled, and the plastic solidifies to form the final product. Once the part is cooled and ejected from the mold, it can be inspected, trimmed, and packaged for delivery.
Applications of Plastic Injection Molding
Plastic injection molding services find applications across various industries, including automotive, electronics, medical, packaging, and consumer goods. The versatility of this process allows for the production of small, intricate parts as well as large, complex components. Additionally, the ability to create custom molds makes injection molding an ideal choice for prototyping and low-volume production.
Benefits of Plastic Injection Molding
There are several benefits of utilizing plastic injection molding services:
1. Cost-Effectiveness**: Injection molding is an efficient and cost-effective manufacturing process. It allows for the production of parts in large volumes with consistent quality, which reduces unit costs and overall production expenses.
2. Design Flexibility: Injection molding offers design flexibility, allowing for the creation of complex shapes and features that may be difficult to achieve with other manufacturing methods.
3. Material Versatility: Injection molding can be used with a wide range of plastic materials, including thermoplastics and thermosets. This versatility allows for the creation of parts with specific mechanical, chemical, and electrical properties.
4. Production Speed**: Injection molding machines can operate at high speeds, resulting in short cycle times and increased production rates. This efficiency is essential for meeting high-demand production schedules.
5. Scalability**: Injection molding is scalable, meaning it can easily adapt to changes in production volumes. Whether it's a small-scale prototype or a large-scale production run, injection molding can meet the demands efficiently.
Factors to Consider When Selecting a Plastic Injection Molding Service Provider
When choosing a plastic injection molding service provider, it's crucial to consider the following factors:
1. Capability and Expertise Ensure that the service provider has the necessary expertise and equipment to handle your specific project requirements. Consider their ability to work with the desired plastic materials, as well as their experience in creating similar parts or components.
2. Quality Assurance**: Quality is paramount in the injection molding process. Ensure that the service provider has a rigorous quality assurance program that includes in-process inspections, testing, and final inspection to ensure consistent product quality.
3. Production Capacity**: Consider the production capacity of the service provider to ensure they can meet your demands, whether it's a small-scale prototype or a large-scale production run.
4. Cost-Effectiveness: Compare quotes from multiple service providers to ensure you're getting competitive pricing. Consider the overall cost, including materials, labor, and any additional fees.
5. Lead Time: Determine the service provider's lead time for project delivery. This is especially crucial for time-sensitive projects.
6. Customer Service and Support**: Excellent customer service and support are crucial for ensuring smooth project execution. Look for a service provider who is responsive, communication-oriented, and willing to collaborate closely with you throughout the project lifecycle.
In conclusion, plastic injection molding services offer a range of benefits that make it an ideal choice for manufacturing a wide variety of parts and components. When selecting a service provider, it's crucial to consider their capability, expertise, quality assurance program, production capacity, cost-effectiveness, lead time, and customer service. By doing so, you can ensure that your project is executed efficiently, cost-effectively, and with the desired quality outcomes.
GETTING A QUOTE WITH LK-MOULD IS FREE AND SIMPLE.
FIND MORE OF OUR SERVICES:
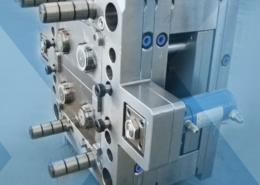
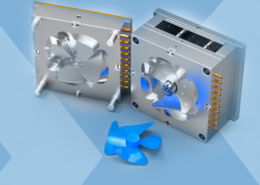
Plastic Molding
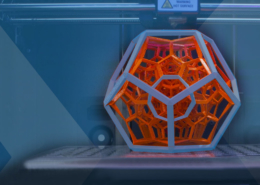
Rapid Prototyping
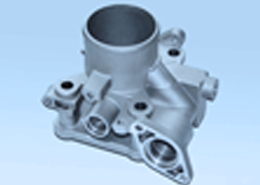
Pressure Die Casting
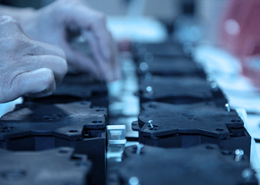
Parts Assembly
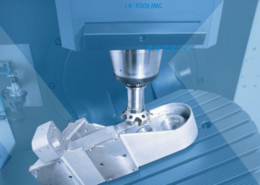