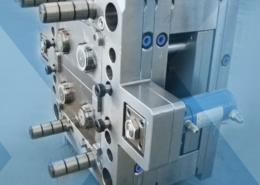
The Essential Role of Molds in Plastic Manufacturing
Author:gly Date: 2024-06-05
Plastics, a ubiquitous material in modern life, have transformed the way we live, work, and interact with the world. From the smallest components of electronics to the largest structural elements of architecture, plastics play a crucial role in nearly every industry. However, the creation of these versatile products starts with a crucial component: molds for plastic.
Plastic molding is a process that involves shaping thermoplastic or thermosetting plastic materials into desired shapes and sizes using a mold. The mold, typically made of metal or other durable materials, serves as a template that dictates the final shape and structure of the plastic part. The molding process involves several stages, including material preparation, mold heating, material injection, cooling, and ejection of the finished part.
Types of Plastic Molding
There are several types of plastic molding techniques, each with its unique characteristics and applications. Injection molding is one of the most common methods, where molten plastic is injected into a mold cavity under high pressure. This process is suitable for producing large quantities of identical parts quickly and efficiently.
Another popular method is die casting, which involves pouring molten plastic into a preheated mold cavity. This technique is often used for creating smaller, more intricate parts that require a high level of detail and precision.
Blow molding, on the other hand, is used to produce hollow plastic parts, such as bottles and containers. In this process, a parison (a tube of plastic) is inflated within a mold, forcing it to take the shape of the mold cavity.
Designing effective plastic molds requires a deep understanding of material properties, molding processes, and the end-use requirements of the plastic part. Mold designers must consider factors such as part geometry, wall thickness, draft angles, ejection systems, and material shrinkage during the molding process.
Proper mold design can significantly impact the quality, efficiency, and cost of plastic production. For instance, optimizing mold cooling systems can shorten cycle times and reduce warping. Similarly, incorporating ejector pins and other ejection systems can ensure smooth and consistent part ejection, avoiding damage or deformation.
Applications of Plastic Molding**
The versatility and customizability of plastic molding make it applicable in almost every industry. In the automotive industry, plastic molds are used to produce a range of components, from interior trim pieces to structural parts like bumpers and dashboards. In electronics, plastic molds are essential for creating components like casings, connectors, and insulation.
The medical industry also relies heavily on plastic molding for creating medical devices, surgical instruments, and disposable products like syringes and IV tubing. The aerospace industry utilizes lightweight, strong plastic parts molded to precise specifications for aircraft components and equipment.
Advancements in Plastic Molding Technology**
As technology continues to evolve, so does the field of plastic molding. Advancements in mold materials, CAD/CAM systems, and molding machines have led to improvements in efficiency, precision, and sustainability.
New mold materials, such as ceramic and composite materials, offer higher thermal stability and longer lifetimes, enabling more complex and precise molding operations. Advanced CAD/CAM systems allow for more accurate mold design and analysis, reducing the need for physical prototypes and speeding up the design-to-production process.
Moreover, innovative molding machines are capable of higher pressures and temperatures, enabling the production of advanced materials like high-performance plastics and composites. This, in turn, opens up new possibilities for creating lighter, stronger, and more durable plastic parts across various industries.
Sustainability Considerations**
As global awareness of environmental sustainability grows, so does the focus on sustainable practices within the plastic molding industry. Molders are increasingly looking for ways to reduce waste, use recycled materials, and implement energy-efficient production methods.
Designing molds for easier material recovery and part ejection can help reduce waste during the molding process. The use of bioplastics and recycled plastics as raw materials can further contribute to environmental sustainability. Additionally, investing in energy-efficient molding machines and implementing lean manufacturing practices can help reduce energy consumption and operational costs.
Conclusion**
Plastic molds play a pivotal role in the production of plastic parts, shaping the materials into the desired forms and sizes for various applications. The complexity and diversity of molding processes, coupled with advancements in technology and sustainability considerations, highlight the importance of continuously innovating and optimizing molding processes.
As the demand for plastic products continues to grow, so does the need for reliable, efficient, and sustainable molding solutions. By harnessing the power of advanced molding techniques and technologies, we can create a more sustainable and innovative future where plastics continue to serve as a valuable material
GETTING A QUOTE WITH LK-MOULD IS FREE AND SIMPLE.
FIND MORE OF OUR SERVICES:
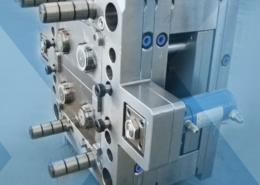
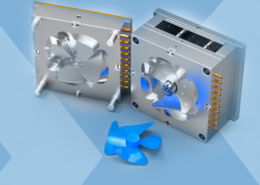
Plastic Molding
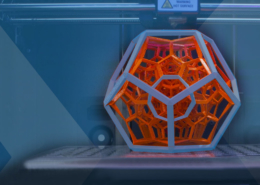
Rapid Prototyping
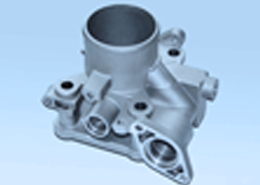
Pressure Die Casting
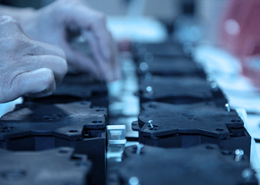
Parts Assembly
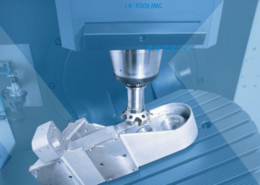