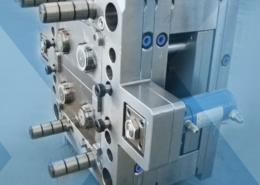
The Role of Mold in the Plastics Industry: A Comprehensive Overview
Author:gly Date: 2024-06-05
In the world of manufacturing, mold and plastic are two essential components that form the backbone of countless products and applications. Together, they enable the creation of everything from simple household items to complex industrial components, revolutionizing the way we live and work. In this comprehensive overview, we will explore the intricacies of mold and its crucial role in the plastics industry, discussing its impact, applications, and future potential.
Molds, often referred to as moulds in British English, are hollowed-out structures used in the process of casting or molding materials into desired shapes and sizes. They serve as templates, defining the final shape and structure of the product. In the context of plastics, molds are precision-tooled devices that are used to shape molten plastic into a solid form, creating parts with intricate details and accurate dimensions.
The molding process begins with the design and fabrication of the mold itself. This involves the creation of a negative impression of the desired product, usually using high-grade steel or aluminum. The mold is then assembled and prepared for use, often involving the application of heat-resistant coatings and the installation of cooling systems.
The plastics industry relies heavily on molding techniques to produce a diverse range of products. Plastics, being malleable in their molten state, can be easily shaped into complex geometries by molds. This flexibility combined with the mold's precision allows for the creation of parts with tight tolerances and intricate features.
Molding techniques vary depending on the type of plastic being used and the desired properties of the final product. Injection molding, for instance, is a widely used process that involves injecting molten plastic into a mold cavity under high pressure. This process is highly efficient and suitable for mass production, making it a staple of the plastics industry.
Other molding techniques include die casting, blow molding, vacuum molding, and compression molding, among others. Each technique has its unique advantages and is chosen based on the specific needs of the application.
Applications of Mold in the Plastics Industry**
The applications of mold in the plastics industry are vast and diverse. Automobiles, for instance, rely heavily on plastic components produced using molds. These components range from interior trim pieces to exterior parts like bumpers and hoods. The precision and repeatability of molding processes ensure that these parts fit perfectly and meet strict safety standards.
The electronics industry also benefits from mold-made plastics. Components like housings, connectors, and insulation are commonly made using molding techniques. The ability to create intricate details and tight tolerances is crucial in this industry, where precision and reliability are paramount.
Moreover, the packaging industry relies on plastic molds to produce containers, bottles, and other packaging materials. These products must meet strict standards for durability, leakage resistance, and aesthetic appeal. Molding techniques allow for the creation of packaging materials that are both functional and visually appealing.
The Future of Mold in the Plastics Industry**
As technology continues to evolve, so do the capabilities and applications of mold in the plastics industry. Advancements in mold design and fabrication, along with new molding techniques and materials, are pushing the boundaries of what's possible.
One such advancement is the emergence of additive manufacturing, or 3D printing, which allows for the creation of complex molds and parts without the need for traditional machining processes. This technology offers greater flexibility and shorter lead times, enabling the rapid prototyping and customization of products.
Additionally, the integration of digital technologies like CAD/CAM systems and simulation software is improving the efficiency and accuracy of mold design and production. These tools allow for precise modeling, analysis, and optimization of mold designs, reducing waste and cost while improving product quality.
Furthermore, the increasing focus on sustainability is driving the development of bio-based plastics and recyclable molds. These materials offer a more environmentally friendly alternative to traditional plastics, reducing the industry's carbon footprint and waste generation.
In conclusion, the role of mold in the plastics industry is crucial and diverse. It enables the creation of a wide range of products with precise dimensions, intricate details, and high-quality finishes. As technology evolves, so do the capabilities of mold, opening up new possibilities for innovation and customization. As we move forward, it's exciting to consider the potential impact that mold and plastics will have on our world, shaping the future of manufacturing and beyond.
GETTING A QUOTE WITH LK-MOULD IS FREE AND SIMPLE.
FIND MORE OF OUR SERVICES:
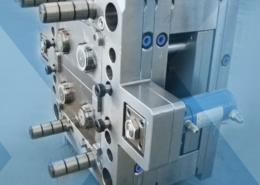
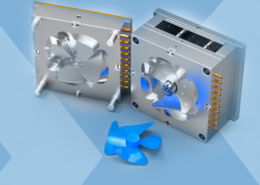
Plastic Molding
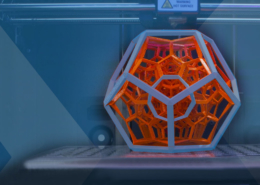
Rapid Prototyping
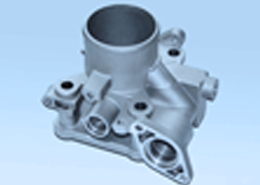
Pressure Die Casting
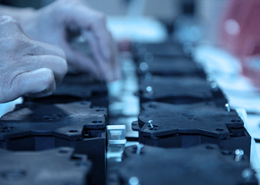
Parts Assembly
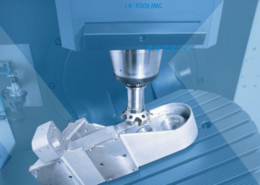