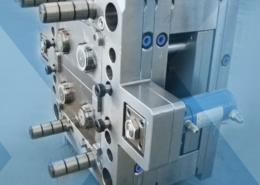
Exploring ABS Injection Molding: Revolutionizing Manufacturing
Author:gly Date: 2024-06-08
Introduction
ABS injection molding stands at the forefront of modern manufacturing processes, heralding a revolution in the production of plastic components. With its versatility, durability, and cost-effectiveness, ABS injection molding has become a cornerstone technique in various industries, ranging from automotive to consumer electronics. This article delves into the intricacies of ABS injection molding, exploring its key aspects and highlighting its significance in contemporary manufacturing.
Material Properties
ABS, short for Acrylonitrile Butadiene Styrene, possesses a unique set of properties ideal for injection molding. Its high impact resistance, excellent machinability, and dimensional stability make it a preferred choice for manufacturing intricate components. Moreover, ABS exhibits good chemical resistance and can be easily modified to meet specific requirements, further enhancing its utility across diverse applications.
ABS injection molding entails the precise melting and injection of ABS pellets into molds, where they cool and solidify to form the desired part. The process offers exceptional reproducibility and allows for intricate geometries, enabling the production of complex components with tight tolerances. Furthermore, ABS can be blended with other materials to impart additional properties, such as enhanced strength or flame retardancy, expanding its applicability in various industries.
Process Overview
The ABS injection molding process begins with the preparation of the raw material, where ABS pellets are dried to remove moisture and ensure optimal molding conditions. The pellets are then fed into the injection molding machine, where they are heated to their melting point and injected into the mold cavity under high pressure. Once inside the mold, the molten ABS material takes the shape of the cavity and is cooled using either water or air to facilitate solidification.
The mold is then opened, and the newly formed part is ejected, ready for further processing or assembly. The entire cycle is completed rapidly, with cycle times ranging from a few seconds to minutes, depending on the complexity of the part and the intricacies of the mold design. With advancements in technology, such as computer-aided design (CAD) and simulation software, the ABS injection molding process has become more efficient and cost-effective, driving its widespread adoption in the manufacturing industry.
Applications
ABS injection molding finds extensive applications across various industries, owing to its versatility and superior mechanical properties. In the automotive sector, ABS is used to manufacture interior and exterior components, such as dashboards, bumpers, and trim panels, due to its impact resistance and aesthetic appeal. Similarly, in the consumer electronics industry, ABS is employed in the production of casings, enclosures, and housings for electronic devices, thanks to its excellent surface finish and dimensional stability.
Moreover, ABS injection molding is prevalent in the production of household appliances, medical devices, and toys, where durability, affordability, and safety are paramount. The ability of ABS to withstand harsh environments, coupled with its ease of processing, makes it an ideal choice for manufacturing a wide range of products that require precision and reliability.
Challenges and Innovations
While ABS injection molding offers numerous advantages, it is not without its challenges. One significant issue is the potential for warpage and shrinkage during the cooling process, which can result in dimensional inaccuracies and surface defects. To mitigate these challenges, manufacturers employ advanced mold design techniques, such as conformal cooling and rapid heat cycling, to achieve uniform cooling and minimize part distortion.
Furthermore, ongoing research and development efforts are focused on enhancing the sustainability of ABS injection molding by exploring alternative materials and eco-friendly processes. Bio-based ABS formulations, derived from renewable sources, offer promising solutions to reduce the environmental impact of traditional petroleum-based ABS resins. Additionally, the adoption of energy-efficient technologies and recycling initiatives aims to minimize waste and promote circular economy principles within the manufacturing ecosystem.
Conclusion
In conclusion, ABS injection molding represents a cornerstone technology in modern manufacturing, offering unparalleled versatility, efficiency, and quality. Its unique material properties, coupled with advancements in process optimization and sustainability, continue to drive innovation across various industries. As we move towards a future characterized by smart manufacturing and sustainable practices, ABS injection molding stands poised to play a pivotal role in shaping the landscape of industrial production. By embracing innovation and collaboration, manufacturers can harness the full potential of ABS injection molding to realize their visions of efficiency, reliability, and environmental stewardship.
GETTING A QUOTE WITH LK-MOULD IS FREE AND SIMPLE.
FIND MORE OF OUR SERVICES:
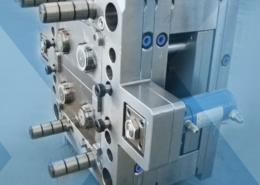
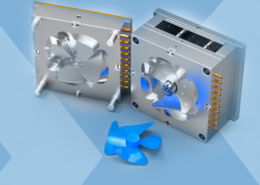
Plastic Molding
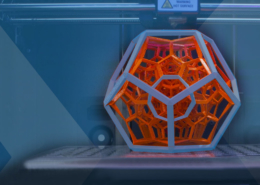
Rapid Prototyping
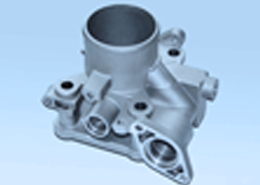
Pressure Die Casting
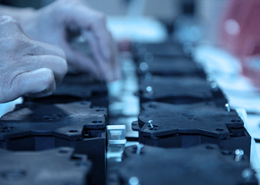
Parts Assembly
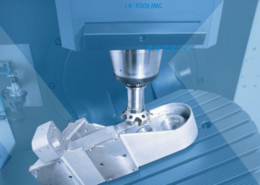