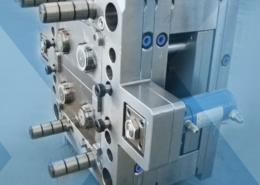
Exploring the Versatility of ABS Molding
Author:gly Date: 2024-06-08
Introduction
ABS molding stands as a cornerstone in the realm of plastic manufacturing, offering a versatile and cost-effective solution for producing a wide range of components. This article aims to delve into the intricacies of ABS molding, shedding light on its processes, applications, advantages, and future prospects.
Unveiling ABS Molding
ABS molding, or Acrylonitrile Butadiene Styrene molding, involves the injection of molten ABS resin into a mold cavity, where it cools and solidifies to form the desired shape. This method is widely employed due to its excellent balance of mechanical properties, impact resistance, and ease of processing.
ABS molding is favored for its versatility, allowing for the production of components with intricate geometries, sharp details, and smooth surface finishes. Moreover, ABS resin can be easily modified to achieve specific properties, such as flame retardancy, UV resistance, or enhanced toughness, making it suitable for diverse applications across industries.
Applications Across Industries
ABS molding finds extensive applications in various industries, including automotive, electronics, consumer goods, and appliances. In automotive manufacturing, ABS components are used for interior trim, dashboard panels, and exterior body parts, thanks to their durability, impact resistance, and aesthetic appeal. Similarly, in the electronics industry, ABS is favored for its electrical insulation properties, making it ideal for enclosures, housings, and structural components.
Moreover, ABS molding is widely employed in the production of consumer goods such as toys, sporting equipment, and household appliances, where its combination of strength, rigidity, and affordability makes it a preferred choice for manufacturers.
Advantages and Challenges
ABS molding offers several advantages, including excellent dimensional stability, good surface finish, and ease of secondary processing, such as painting, plating, or welding. Additionally, ABS resin can be easily recycled and reprocessed, contributing to its sustainability and environmental friendliness.
However, challenges such as warpage, shrinkage, and surface defects may arise during the molding process, requiring careful consideration of processing parameters, mold design, and material selection to mitigate these issues effectively.
Technological Advancements and Future Directions
Recent technological advancements in ABS molding have focused on enhancing process efficiency, reducing cycle times, and improving part quality. Innovations such as advanced mold designs, hot runner systems, and in-mold decoration techniques have enabled manufacturers to achieve higher productivity and greater design freedom.
Looking ahead, the future of ABS molding is poised for further innovation and development. Research efforts are underway to explore novel materials, optimize processing techniques, and integrate digital technologies such as simulation software and IoT-enabled equipment to create smarter, more efficient manufacturing solutions.
Conclusion
In conclusion, ABS molding stands as a versatile and cost-effective solution for producing a wide range of components across industries. Despite facing challenges, continuous innovation and technological advancements ensure that ABS molding remains at the forefront of plastic manufacturing. As industries evolve and demand for high-quality, customized components continues to grow, the role of ABS molding in shaping the future of manufacturing will only become more significant. By embracing innovation, sustainability, and collaboration, ABS molding manufacturers can unlock new opportunities and drive the industry forward into a brighter and more resilient future.
GETTING A QUOTE WITH LK-MOULD IS FREE AND SIMPLE.
FIND MORE OF OUR SERVICES:
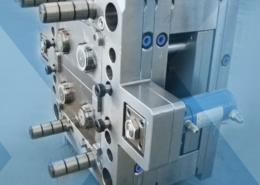
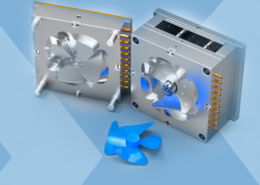
Plastic Molding
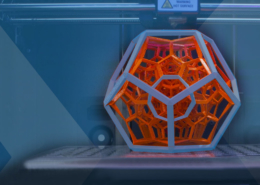
Rapid Prototyping
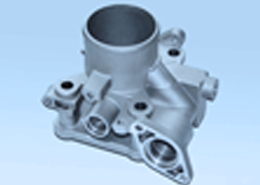
Pressure Die Casting
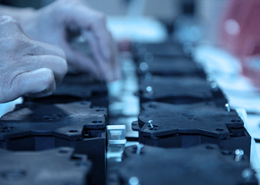
Parts Assembly
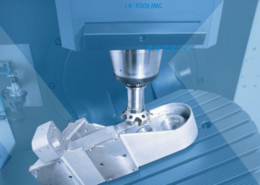