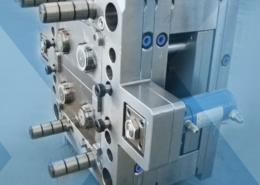
Exploring the Potential of Acrylic Injection Molding
Author:gly Date: 2024-06-08
Introduction
Acrylic injection molding stands as a pivotal process in modern manufacturing, offering unparalleled versatility and precision in the production of various components. This article delves into the depths of acrylic injection molding, exploring its mechanisms, applications, challenges, and future prospects.
Unraveling Acrylic Injection Molding
Acrylic injection molding involves the melting of acrylic pellets and injecting the molten material into a mold cavity under high pressure. Upon cooling, the acrylic solidifies into the desired shape, boasting exceptional clarity, dimensional accuracy, and surface finish.
Acrylic injection molding has garnered significant interest due to its ability to produce complex shapes with precise details, making it a preferred choice for a wide range of applications.
Applications Across Industries
Acrylic injection molding finds extensive applications across diverse industries, including automotive, electronics, signage, and consumer goods. In automotive, acrylic components are utilized for interior trim, lighting lenses, and instrument panels, offering durability and aesthetic appeal. Similarly, in electronics, acrylic is favored for its transparency and UV resistance, making it suitable for display screens and housings.
Advantages and Challenges
The process of acrylic injection molding offers several advantages, such as high optical clarity, excellent weatherability, and ease of coloring. However, challenges such as material shrinkage, surface defects, and tooling costs require careful consideration and expertise to overcome.
Despite these challenges, the benefits of acrylic injection molding outweigh the drawbacks, making it a preferred choice for manufacturers seeking high-quality, aesthetically pleasing components.
Technological Advancements and Future Directions
Recent technological advancements, including improved mold designs, advanced processing techniques, and the development of new acrylic formulations, have enhanced the capabilities and efficiency of acrylic injection molding. Furthermore, ongoing research focuses on exploring sustainable alternatives and optimizing recycling processes to reduce environmental impact.
Conclusion
In conclusion, acrylic injection molding stands at the forefront of modern manufacturing, offering unmatched precision, clarity, and versatility in producing a wide range of components across industries. Despite facing challenges, continuous technological advancements and research efforts ensure that acrylic injection molding remains a vital process in shaping the future of manufacturing. As industries evolve and sustainability becomes increasingly important, further innovation and collaboration are essential for unlocking the full potential of acrylic injection molding and meeting the demands of a rapidly changing world.
GETTING A QUOTE WITH LK-MOULD IS FREE AND SIMPLE.
FIND MORE OF OUR SERVICES:
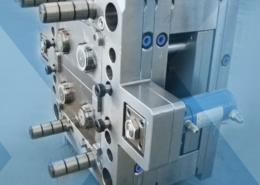
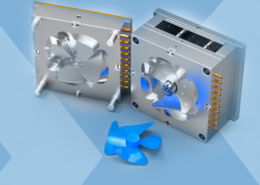
Plastic Molding
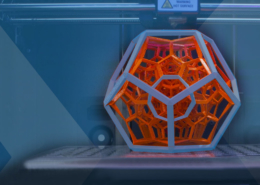
Rapid Prototyping
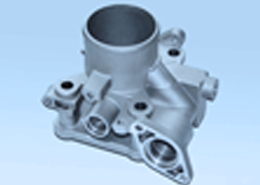
Pressure Die Casting
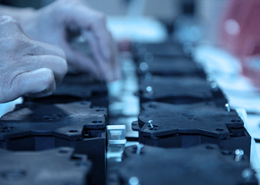
Parts Assembly
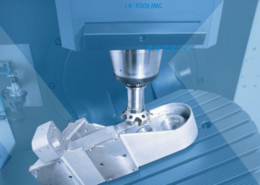