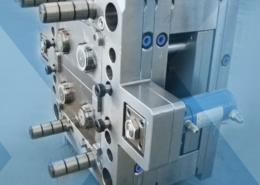
Exploring Advanced Plastic Moulding Techniques
Author:gly Date: 2024-06-08
Introduction: Unveiling the Future of Manufacturing
Advanced plastic moulding techniques represent the pinnacle of modern manufacturing, where innovation and precision converge to push the boundaries of what's possible. From intricate designs to high-performance materials, advanced plastic moulding offers a wealth of opportunities for industries seeking to stay ahead in a competitive landscape. In this article, we delve into the world of advanced plastic moulding, exploring its techniques, applications, benefits, and future directions.
1. High-Performance Materials
At the forefront of advanced plastic moulding is the use of high-performance materials that offer superior properties in terms of strength, durability, and chemical resistance. From engineering-grade thermoplastics to exotic polymers, these materials are carefully selected to meet the demanding requirements of various industries.
For example, in the aerospace sector, advanced plastic moulding techniques are used to produce lightweight components from materials such as carbon fiber-reinforced polymers, which offer exceptional strength-to-weight ratios and resistance to harsh environments. Similarly, in the medical field, biocompatible materials like PEEK (polyether ether ketone) are utilized for manufacturing surgical implants and instruments, where compatibility with the human body is crucial.
2. Complex Geometries and Microstructures
Advanced plastic moulding techniques enable the production of components with intricate geometries and microstructures that were previously unattainable using conventional methods. Through processes such as multi-shot moulding, overmoulding, and micro-injection moulding, manufacturers can achieve precise control over part features and material distribution.
For instance, in the automotive industry, advanced plastic moulding techniques are used to produce complex interior trim components with integrated functionalities, such as air vents, lighting, and electronic controls. Similarly, in the electronics sector, micro-injection moulding enables the fabrication of miniature components for devices such as smartphones, wearables, and medical sensors, where size and precision are paramount.
3. Sustainability and Circular Economy
In addition to performance enhancements, advanced plastic moulding techniques are driving sustainability initiatives and promoting a circular economy by reducing material waste and energy consumption. By optimizing processes, minimizing scrap, and incorporating recycled and bio-based materials, manufacturers can mitigate the environmental impact of plastic production.
For example, advancements in injection moulding simulation software allow for the optimization of process parameters to minimize material usage and energy consumption while maximizing part quality and production efficiency. Furthermore, the integration of closed-loop recycling systems enables the reprocessing of post-consumer and post-industrial plastic waste into new raw materials for moulding, reducing reliance on virgin plastics and diverting waste from landfills.
4. Future Directions and Innovations
Looking ahead, the future of advanced plastic moulding holds promise for continued innovation and advancement. Emerging trends such as 3D printing, nanocomposite materials, and smart manufacturing are reshaping the landscape of plastic manufacturing, offering new possibilities for customization, efficiency, and functionality.
Additive manufacturing techniques like selective laser sintering (SLS) and fused deposition modelling (FDM) enable rapid prototyping, tooling, and low-volume production of complex geometries with minimal material waste. Furthermore, the development of nanocomposite materials, reinforced with nanoscale fillers such as graphene and carbon nanotubes, offers enhanced mechanical, thermal, and electrical properties for a wide range of applications.
Conclusion: Embracing the Future of Manufacturing
In conclusion, advanced plastic moulding techniques represent a paradigm shift in modern manufacturing, offering unparalleled opportunities for innovation, performance, and sustainability. Through the use of high-performance materials, complex geometries, sustainability initiatives, and future-oriented innovations, advanced plastic moulding is poised to shape the future of industries ranging from aerospace and automotive to healthcare and electronics.
As we navigate the complexities of the 21st century, let us embrace the transformative potential of advanced plastic moulding to drive progress, prosperity, and sustainability. By leveraging cutting-edge technologies, materials, and design methodologies, we can unlock new possibilities for efficiency, customization, and environmental responsibility, ensuring a brighter future for generations to come.
GETTING A QUOTE WITH LK-MOULD IS FREE AND SIMPLE.
FIND MORE OF OUR SERVICES:
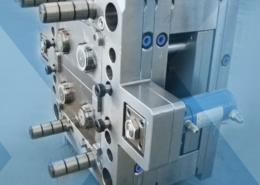
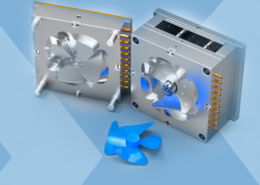
Plastic Molding
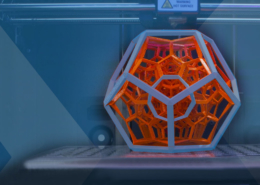
Rapid Prototyping
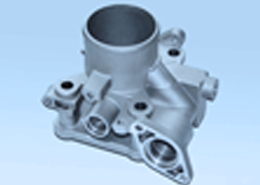
Pressure Die Casting
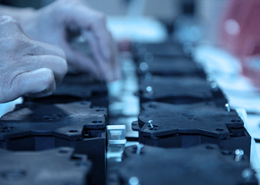
Parts Assembly
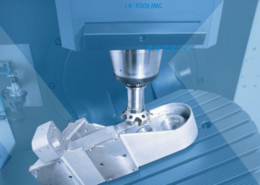