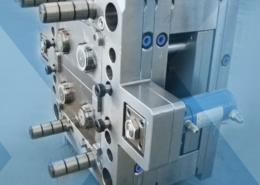
Exploring the Intricacies of Bobbin Molding
Author:gly Date: 2024-06-08
Bobbin molding stands at the forefront of innovative manufacturing techniques, offering a versatile approach to producing intricate components with precision and efficiency. In this article, we delve into the world of bobbin molding, unraveling its complexities, applications, and potential impact on industrial processes.
Unraveling Bobbin Molding
Introduction to Bobbin Molding
Bobbin molding, also known as coil winding molding, encompasses a specialized manufacturing process wherein materials are wound around a cylindrical or spool-like core to create intricate shapes and structures. This technique finds widespread application in industries ranging from electronics to textiles, owing to its ability to produce complex components with high repeatability and accuracy.
Historical Evolution
The origins of bobbin molding can be traced back to ancient civilizations, where artisans utilized rudimentary tools and techniques to fashion intricate objects from natural materials such as wood, bone, and clay. Over the centuries, advancements in materials science and manufacturing technologies have propelled bobbin molding into the realm of precision engineering, enabling the production of miniature components for a myriad of applications.
Operational Mechanics
At its core, bobbin molding involves the winding of a flexible material, such as wire, thread, or composite filament, onto a pre-formed core or bobbin. This process may be facilitated manually or automated using specialized machinery, depending on the complexity and scale of production. The winding pattern and tension are carefully controlled to achieve the desired shape and structural integrity of the final product.
Applications Across Industries
Electronics and Electrical Engineering
In the realm of electronics and electrical engineering, bobbin molding plays a pivotal role in the fabrication of coils, transformers, and inductors used in various electronic devices and power systems. The precise winding of conductive wires onto insulated bobbins ensures optimal performance and reliability in applications ranging from consumer electronics to aerospace systems.
Textile Manufacturing
Bobbin molding finds extensive application in textile manufacturing, particularly in the production of sewing and embroidery threads. By winding natural or synthetic fibers onto bobbins of varying sizes and shapes, manufacturers can tailor thread properties such as strength, elasticity, and color to meet the diverse needs of the textile industry, from fashion apparel to automotive upholstery.
Automotive Components
The automotive industry leverages bobbin molding for the production of critical components such as airbag initiators, sensor coils, and solenoids. The ability to precisely wind conductive wires or magnetic materials onto compact bobbins enables the integration of sophisticated electronic and electromechanical systems into modern vehicles, enhancing safety, performance, and efficiency.
Technological Innovations
Advanced Materials
Advancements in material science have expanded the repertoire of materials suitable for bobbin molding, ranging from traditional metals and polymers to exotic alloys and composite materials. These materials offer enhanced mechanical properties, thermal stability, and electrical conductivity, unlocking new possibilities for engineering complex components with superior performance and durability.
Automation and Robotics
The integration of automation and robotics in bobbin molding processes has revolutionized production efficiency and quality control. Automated winding machines equipped with precision control systems and robotic manipulators can achieve higher throughput, tighter tolerances, and reduced waste compared to manual operations, thereby streamlining manufacturing workflows and minimizing human error.
Digital Twin Technology
The adoption of digital twin technology enables manufacturers to simulate and optimize bobbin molding processes in virtual environments, prior to physical production. By modeling the behavior of materials, equipment, and operating parameters, engineers can identify potential issues, optimize designs, and refine production strategies, resulting in faster time-to-market and improved product quality.
Challenges and Future Outlook
Integration Complexity
The integration of bobbin molding into existing manufacturing processes poses challenges related to equipment compatibility, process synchronization, and workflow optimization. Addressing these challenges requires interdisciplinary collaboration and investments in research and development to develop seamless integration solutions tailored to specific industry requirements.
Material Sustainability
As sustainability concerns continue to drive industry trends, the bobbin molding sector faces pressure to adopt eco-friendly materials and manufacturing practices. Research into biodegradable polymers, recycled metals, and renewable fibers holds promise for reducing environmental impact while maintaining performance and cost-effectiveness in bobbin molding applications.
Skills Development
The evolving nature of bobbin molding technologies necessitates ongoing skills development and training initiatives to equip the workforce with the knowledge and competencies required to operate and innovate within the field. Educational programs, apprenticeships, and professional certifications play a crucial role in nurturing talent and fostering innovation in bobbin molding industries.
Conclusion
Bobbin molding stands as a testament to human ingenuity and technological innovation, offering a versatile and precise manufacturing solution across diverse industries. As we navigate the complexities of the modern industrial landscape, embracing advancements in materials science, automation, and digitalization will be instrumental in unlocking the full potential of bobbin molding and shaping the future of manufacturing.
GETTING A QUOTE WITH LK-MOULD IS FREE AND SIMPLE.
FIND MORE OF OUR SERVICES:
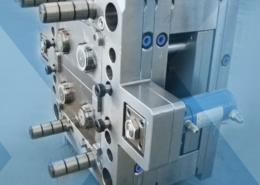
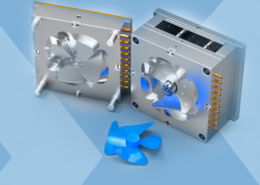
Plastic Molding
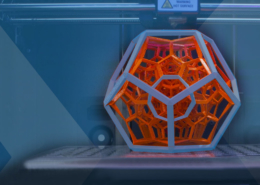
Rapid Prototyping
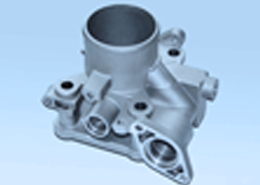
Pressure Die Casting
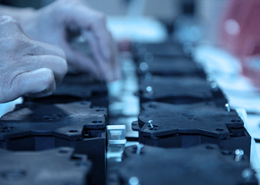
Parts Assembly
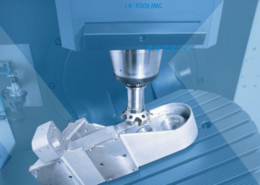