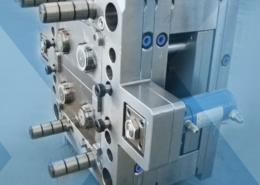
Bottle Cap Injection Molding: Revolutionizing Packaging
Author:gly Date: 2024-06-08
Bottle cap injection molding is a pivotal process in the manufacturing of caps for bottles, a fundamental component of the packaging industry. With its intricate design and precise execution, it stands as a testament to the ingenuity of modern engineering. This article delves into the nuances of bottle cap injection molding, exploring its mechanisms, applications, and impact on various industries.
1. The Genesis of Innovation
The genesis of bottle cap injection molding can be traced back to the mid-20th century when the demand for efficient packaging solutions soared. Traditional methods of cap production were labor-intensive and time-consuming, prompting researchers and engineers to seek alternative approaches. Thus, the concept of injection molding emerged, revolutionizing the manufacturing landscape.
Injection molding involves the melting of thermoplastic materials, such as polyethylene or polypropylene, under high pressure. The molten material is then injected into a mold cavity, where it solidifies to form the desired shape. This process offers unparalleled precision and repeatability, making it ideal for mass production.
2. Precision Engineering
One of the defining characteristics of bottle cap injection molding is its precision engineering. The molds used in this process are meticulously crafted to exact specifications, ensuring uniformity across all produced caps. This level of precision is essential in industries where consistency and quality are paramount, such as pharmaceuticals and food packaging.
Moreover, advancements in technology have enabled the integration of features such as tamper-evident seals and child-resistant closures into the molding process. These enhancements not only enhance product safety but also cater to the evolving needs of consumers.
3. Efficiency and Cost-Effectiveness
In addition to precision, bottle cap injection molding offers unparalleled efficiency and cost-effectiveness. The automated nature of the process minimizes human intervention, reducing the risk of errors and increasing productivity. Furthermore, the ability to use recyclable materials enhances sustainability while simultaneously lowering production costs.
This efficiency has made bottle cap injection molding indispensable in various industries, ranging from beverage manufacturing to cosmetics packaging. With shorter lead times and higher output rates, companies can meet consumer demands while maintaining a competitive edge in the market.
4. Driving Innovation Forward
Bottle cap injection molding continues to drive innovation forward, pushing the boundaries of what is possible in the realm of packaging. Research and development efforts are focused on optimizing cycle times, reducing material waste, and exploring novel materials with enhanced properties.
Furthermore, advancements in digital design and simulation software have streamlined the prototyping process, allowing for rapid iterations and faster time-to-market. This agile approach to product development empowers manufacturers to stay ahead of trends and adapt to changing consumer preferences.
In Conclusion:
In conclusion, bottle cap injection molding stands as a cornerstone of modern packaging solutions, combining precision engineering with efficiency and innovation. Its impact extends across industries, shaping the way products are packaged, distributed, and consumed. As we look to the future, continued research and development in this field promise even greater advancements, further cementing its importance in the global manufacturing landscape.
GETTING A QUOTE WITH LK-MOULD IS FREE AND SIMPLE.
FIND MORE OF OUR SERVICES:
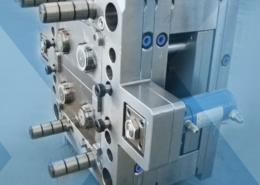
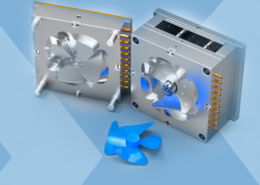
Plastic Molding
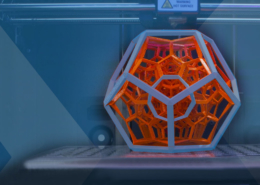
Rapid Prototyping
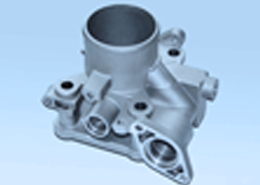
Pressure Die Casting
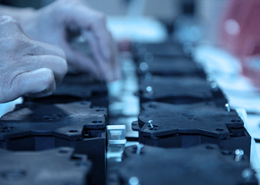
Parts Assembly
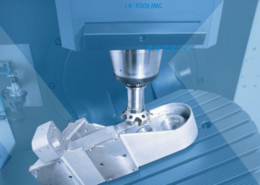