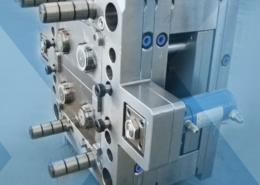
Exploring the Advancements of Co-Injection Molding
Author:gly Date: 2024-06-08
Co-injection molding, a cutting-edge technology in the realm of plastic injection molding, has garnered substantial attention due to its remarkable capabilities and applications. This article aims to delve into the intricacies of co-injection molding, elucidating its significance, methodologies, applications, advantages, challenges, and future prospects.
Introduction: Unveiling the Potential of Co-Injection Molding
Co-injection molding, also known as sandwich molding or multi-material injection molding, revolutionizes traditional injection molding processes by enabling the seamless integration of multiple materials within a single product. This innovative technique involves the simultaneous injection of two or more materials into a mold, resulting in a composite structure with distinct layers or properties.
Evolution of Co-Injection Molding
The concept of co-injection molding traces back to the mid-20th century, with initial developments focusing on enhancing product aesthetics and performance. Over the decades, advancements in material science, mold design, and process control have propelled co-injection molding into a versatile manufacturing solution, catering to diverse industries ranging from automotive and packaging to electronics and medical devices.
Mechanisms and Process Overview
At its core, co-injection molding entails the synchronized injection of two polymers through a specialized injection molding machine equipped with multiple barrels and nozzles. The process begins with the primary material being injected into the mold cavity, followed by the secondary material, which encases or encapsulates the primary component. Precise control of injection timing, pressure, and temperature is crucial to achieving optimal bonding between the layers and desired part properties.
Applications Across Industries
The versatility of co-injection molding transcends traditional manufacturing boundaries, offering a myriad of applications across various sectors.
Automotive Industry Advancements
In the automotive industry, co-injection molding facilitates the production of lightweight, durable components with enhanced structural integrity and aesthetic appeal. From interior trim panels and dashboard components to exterior body panels and bumper systems, co-injection molding enables the integration of contrasting colors, textures, and functionalities within a single part, thereby optimizing design flexibility and cost-effectiveness.
Packaging Solutions and Sustainability
Co-injection molding plays a pivotal role in revolutionizing packaging solutions, particularly in the food and beverage sector. By incorporating barrier layers, recyclable materials, and innovative designs, manufacturers can develop eco-friendly packaging solutions that prolong shelf life, minimize product waste, and comply with stringent regulatory standards. Furthermore, the ability to create multi-layered structures enhances packaging durability, tamper resistance, and product protection during transit and storage.
Electronics and Consumer Goods
In the realm of electronics and consumer goods, co-injection molding facilitates the integration of functional elements, such as conductive traces, insulating layers, and embedded components, within intricate product designs. From smartphone casings and wearable devices to household appliances and electronic enclosures, co-injection molding offers unparalleled design freedom and customization options, thereby elevating product performance, aesthetics, and user experience.
Advantages and Challenges
Despite its myriad benefits, co-injection molding presents certain challenges and considerations that necessitate meticulous attention and expertise.
Advantages of Co-Injection Molding
Enhanced Product Performance: By combining complementary materials with distinct properties, co-injection molding enables the development of products with superior mechanical, thermal, and chemical resistance properties.
Cost Efficiency: The ability to incorporate recycled or lower-cost materials as secondary layers reduces material expenses and enhances sustainability.
Design Flexibility: Co-injection molding empowers designers to create complex geometries, integrated functionalities, and aesthetic enhancements without compromising manufacturing efficiency or part integrity.
Challenges and Considerations
Material Compatibility: Selecting compatible materials with matching melt temperatures, viscosities, and adhesion properties is critical to achieving robust bonding and minimizing delamination or interfacial defects.
Process Optimization: Fine-tuning process parameters, such as injection pressure, temperature profiles, and cooling rates, is essential to mitigating warpage, sink marks, and other molding defects.
Tooling Complexity: Designing and fabricating molds capable of accommodating multiple materials, flow channels, and gating systems require advanced tooling expertise and precision machining capabilities.
Future Directions and Opportunities
As co-injection molding continues to evolve and gain traction across industries, several avenues for innovation and optimization emerge.
Material Innovation and Compatibility
Advancements in polymer chemistry, additive manufacturing, and nanotechnology pave the way for the development of novel materials with tailored properties and improved compatibility for co-injection molding applications. By leveraging biodegradable polymers, nano-additives, and functionalized surfaces, manufacturers can enhance material adhesion, barrier performance, and sustainability.
Process Integration and Automation
The integration of real-time monitoring systems, predictive analytics, and machine learning algorithms enables proactive process optimization, defect detection, and quality assurance in co-injection molding operations. Automated handling and robotic-assisted manufacturing further streamline production workflows, reduce cycle times, and enhance manufacturing efficiency.
Sustainability and Circular Economy
In alignment with global sustainability initiatives and circular economy principles, co-injection molding offers a pathway towards closed-loop material recycling, waste reduction, and resource conservation. By designing products for disassembly, material recovery, and remanufacturing, manufacturers can minimize environmental impact, extend product lifespan, and create value-added opportunities throughout the product lifecycle.
Conclusion: Pioneering the Future of Injection Molding
In conclusion, co-injection molding stands at the forefront of innovation, driving advancements in material science, manufacturing technology, and product design. By seamlessly integrating multiple materials within a single part, co-injection molding enables unparalleled design flexibility, performance optimization, and sustainability across diverse industries. Embracing a holistic approach that encompasses material innovation, process optimization, and sustainability principles, stakeholders can unlock the full potential of co-injection molding and pioneer the next generation of injection molding solutions.
GETTING A QUOTE WITH LK-MOULD IS FREE AND SIMPLE.
FIND MORE OF OUR SERVICES:
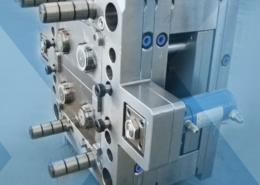
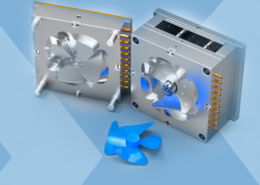
Plastic Molding
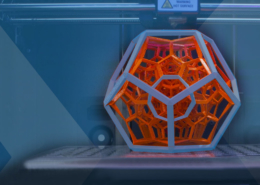
Rapid Prototyping
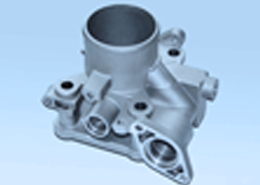
Pressure Die Casting
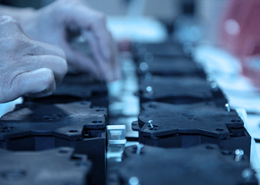
Parts Assembly
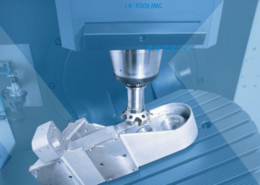