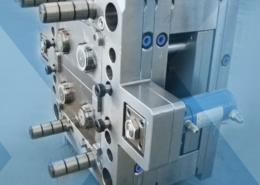
Exploring Clean Room Injection Molding: Precision in a Controlled Environment
Author:gly Date: 2024-06-08
Clean room injection molding stands at the forefront of precision manufacturing, offering unparalleled control over production environments to ensure the highest quality of molded products. This advanced manufacturing process combines the principles of injection molding with stringent cleanliness standards, creating a controlled environment free from contaminants. In this article, we delve into the world of clean room injection molding, unraveling its intricacies, applications, and benefits.
Unveiling the Concept
Clean room injection molding involves the integration of injection molding processes with clean room technology to achieve superior product quality and consistency. The primary objective is to minimize the presence of airborne particles, such as dust, microbes, and other contaminants, to safeguard the integrity of the manufacturing process and the final product. This level of precision and cleanliness is particularly critical in industries such as medical devices, pharmaceuticals, and electronics, where even the slightest impurity can compromise product performance and safety.
Key Components
Controlled Environment
Clean room injection molding facilities are equipped with specialized HVAC systems, air filtration units, and contamination control measures to maintain a controlled environment. These facilities adhere to stringent cleanliness standards, such as ISO classes, to ensure minimal particle counts and microbial contamination.
Molding Equipment
The injection molding machines used in clean room environments are constructed from materials that are easy to clean and resistant to corrosion. These machines are equipped with advanced controls and monitoring systems to maintain optimal operating conditions and ensure consistent product quality.
Applications
Clean room injection molding finds applications in a wide range of industries, including:
Medical Devices
In the medical device industry, clean room injection molding is utilized for manufacturing precision components such as syringe barrels, IV connectors, and surgical instruments. The stringent cleanliness standards ensure compliance with regulatory requirements and patient safety.
Pharmaceutical Packaging
Clean room injection molding is employed for producing pharmaceutical packaging components, including vials, ampoules, and caps. The controlled environment prevents contamination and ensures the integrity of the packaging materials, maintaining the efficacy of the drugs.
Advantages
Precision and Consistency
Clean room injection molding offers unparalleled precision and consistency in product manufacturing, ensuring uniformity in dimensions, surface finish, and mechanical properties. This level of precision is essential for producing high-quality components with tight tolerances.
Compliance with Regulatory Standards
The stringent cleanliness standards enforced in clean room environments ensure compliance with regulatory requirements, such as Good Manufacturing Practices (GMP) and ISO standards. This is particularly important in industries such as healthcare and pharmaceuticals, where product safety and quality are paramount.
Challenges and Considerations
Cost
The implementation of clean room injection molding entails significant upfront costs associated with facility construction, equipment acquisition, and maintenance. However, the long-term benefits, such as improved product quality and regulatory compliance, justify the investment for many manufacturers.
Training and Certification
Operating in a clean room environment requires specialized training and certification for personnel to adhere to cleanliness protocols and contamination control measures. Manufacturers must invest in training programs to ensure compliance and competency among their workforce.
Future Directions
As technology continues to evolve, the future of clean room injection molding holds promising opportunities for innovation and advancements. Emerging technologies, such as automation, robotics, and real-time monitoring systems, are poised to enhance efficiency, productivity, and quality in clean room manufacturing environments. Additionally, the integration of artificial intelligence and data analytics can provide valuable insights for process optimization and quality control.
Conclusion
In conclusion, clean room injection molding represents the pinnacle of precision manufacturing, offering unparalleled control over production environments to ensure the highest quality of molded products. With its applications spanning across industries such as healthcare, pharmaceuticals, and electronics, clean room injection molding plays a vital role in producing critical components with stringent cleanliness and quality requirements. As technology continues to advance and regulatory standards evolve, the future of clean room injection molding holds tremendous potential for innovation, efficiency, and excellence in manufacturing. Through continuous investment in technology, training, and process optimization, manufacturers can unlock new opportunities and propel the industry towards a cleaner, safer, and more efficient future.
GETTING A QUOTE WITH LK-MOULD IS FREE AND SIMPLE.
FIND MORE OF OUR SERVICES:
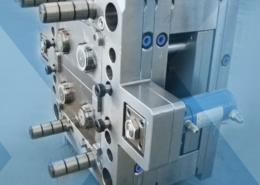
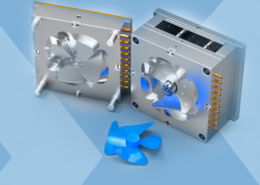
Plastic Molding
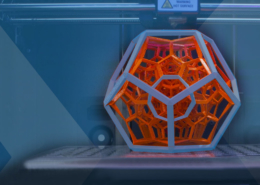
Rapid Prototyping
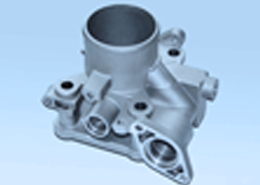
Pressure Die Casting
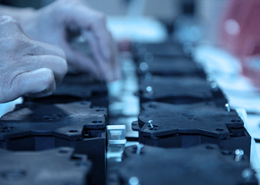
Parts Assembly
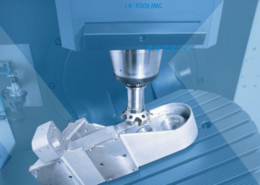