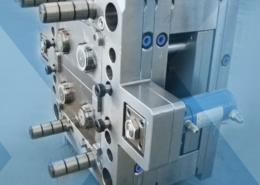
Exploring Double Shot Injection Molding: A Comprehensive Overview
Author:gly Date: 2024-06-08
In the realm of manufacturing, innovation is the cornerstone of progress. One such innovation that has revolutionized the production of plastic components is double shot injection molding. This advanced technique offers a myriad of benefits, ranging from enhanced design flexibility to improved efficiency in production processes. In this article, we delve into the intricacies of double shot injection molding, exploring its mechanisms, applications, advantages, challenges, and future prospects.
Understanding Double Shot Injection Molding
Double shot injection molding, also known as two-shot molding or multi-shot molding, is a sophisticated manufacturing process that involves injecting two different materials into a single mold in two consecutive cycles. This process enables the creation of complex plastic parts with varying colors, materials, or properties in a single operation. Unlike traditional injection molding, which produces monolithic parts, double shot molding offers unparalleled versatility and efficiency in component production.
Mechanism of Double Shot Injection Molding
The process of double shot injection molding begins with the injection of the first material into the mold cavity to form the initial structure or substrate. Subsequently, a second material is injected into the same mold cavity, either sequentially or simultaneously, to create additional features, colors, or textures on the substrate. This sequential injection process is facilitated by specialized equipment and precise control systems, ensuring seamless integration of multiple materials within a single component.
Materials Utilized in Double Shot Molding
Double shot injection molding supports a wide range of thermoplastic and thermoset materials, including but not limited to polypropylene (PP), acrylonitrile butadiene styrene (ABS), polycarbonate (PC), thermoplastic elastomers (TPE), and silicone rubber. The selection of materials depends on the specific requirements of the application, such as mechanical properties, chemical resistance, and aesthetic appeal. Additionally, compatibility between the materials is crucial to achieve optimal adhesion and bonding during the molding process.
Equipment and Tooling for Double Shot Molding
The successful implementation of double shot injection molding relies on advanced machinery and precision tooling. Dual injection molding machines equipped with rotating or shuttle molds enable the sequential injection of different materials with high accuracy and repeatability. Additionally, specialized tooling, such as core-back technology and interchangeable inserts, facilitates the creation of intricate geometries and overmolded features. These cutting-edge equipment and tooling solutions are essential for achieving consistent quality and efficiency in double shot molding operations.
Applications of Double Shot Injection Molding
Double shot injection molding finds widespread applications across various industries, owing to its ability to create complex, multi-material components with exceptional precision and functionality. Some notable applications include:
Consumer Electronics
In the consumer electronics industry, double shot molding is utilized for producing sleek and durable components such as smartphone cases, keypads, and buttons. The ability to incorporate different materials and colors within a single part allows manufacturers to achieve aesthetic appeal and ergonomic design while maintaining structural integrity and functionality.
Automotive Components
In the automotive sector, double shot injection molding is employed for manufacturing interior and exterior components, including dashboard panels, door handles, and decorative trims. By integrating soft-touch TPEs with rigid plastics, automotive manufacturers can enhance the tactile feel and visual appeal of vehicle interiors while meeting stringent performance and durability requirements.
Medical Devices
In the medical device industry, double shot molding is utilized for fabricating specialized components such as seals, valves, and grips for medical instruments and devices. The ability to combine biocompatible materials with antimicrobial additives enables the production of sterile and ergonomic parts essential for healthcare applications.
Advantages and Challenges of Double Shot Injection Molding
Advantages
Design Flexibility
: Double shot molding offers unparalleled design freedom, allowing for the creation of complex geometries, multi-color patterns, and overmolded features in a single operation.
Cost Efficiency
: By consolidating multiple manufacturing steps into a single process, double shot molding reduces labor costs, material waste, and assembly time, thereby enhancing overall efficiency and competitiveness.
Improved Product Quality
: The integration of different materials with complementary properties enhances the performance, aesthetics, and functionality of plastic components, leading to higher customer satisfaction and brand loyalty.
Challenges
Material Compatibility
: Ensuring compatibility between different materials is critical to achieving strong adhesion and bonding in double shot molding, requiring thorough material selection and testing.
Tooling Complexity
: Designing and fabricating molds for double shot molding involves intricate geometries and precise tolerances, which can increase tooling costs and lead times.
Process Optimization
: Achieving consistent and defect-free parts in double shot molding requires meticulous process optimization, including temperature control, injection timing, and mold cooling, to minimize defects such as warpage, sink marks, and knit lines.
Future Perspectives and Recommendations
As double shot injection molding continues to evolve, there are several areas for future research and development to explore:
Material Innovation
: The development of new materials with enhanced properties, such as improved adhesion, durability, and recyclability, will expand the capabilities and applications of double shot molding.
Process Optimization
: Further advancements in process control technologies, such as real-time monitoring and predictive analytics, will enable manufacturers to optimize cycle times, reduce scrap rates, and improve overall efficiency.
Sustainability Initiatives
: Integrating sustainable practices, such as using bio-based or recycled materials and minimizing energy consumption, will align double shot molding with global sustainability goals and consumer preferences.
In conclusion, double shot injection molding represents a paradigm shift in plastic component manufacturing, offering unparalleled design flexibility, efficiency, and quality. By understanding its mechanisms, applications, advantages, and challenges, manufacturers can harness the full potential of this innovative technology to drive innovation and competitiveness in their respective industries.
GETTING A QUOTE WITH LK-MOULD IS FREE AND SIMPLE.
FIND MORE OF OUR SERVICES:
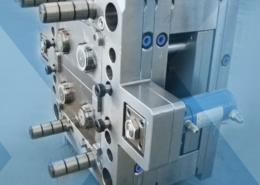
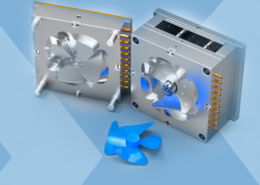
Plastic Molding
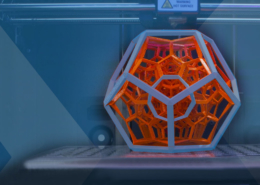
Rapid Prototyping
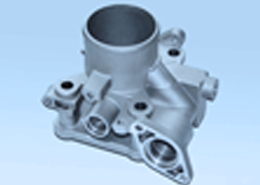
Pressure Die Casting
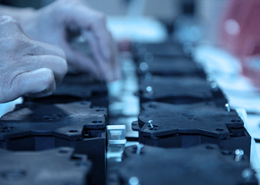
Parts Assembly
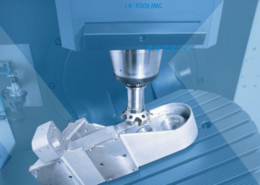