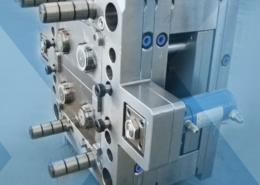
Gas Assist Injection Molding: Revolutionizing Plastic Manufacturing
Author:gly Date: 2024-06-08
Plastic injection molding has long been a cornerstone of industrial manufacturing, allowing for the mass production of intricate and durable plastic parts. However, traditional injection molding techniques often face challenges such as uneven cooling, warping, and sink marks. In response to these challenges, gas assist injection molding (GAIM) has emerged as a revolutionary process that enhances the efficiency, quality, and versatility of plastic part production.
The Concept of Gas Assist Injection Molding
Gas assist injection molding involves injecting a precisely metered volume of nitrogen gas into the mold cavity after the polymer melt fills a certain percentage of the cavity. This controlled gas pressure pushes the molten plastic against the mold walls, hollowing out the part and eliminating sink marks while ensuring uniformity in wall thickness. The gas also aids in cooling the part, reducing cycle times and improving overall productivity.
Gas assist injection molding was first introduced commercially in the 1980s and has since undergone significant advancements in technology and application. Today, it is widely utilized across various industries, including automotive, consumer goods, and electronics, to produce complex, lightweight, and aesthetically pleasing plastic components.
Advantages of Gas Assist Injection Molding
Gas assist injection molding offers several distinct advantages over traditional molding techniques. Firstly, it enables the production of large, complex parts with reduced material usage, resulting in cost savings and environmental benefits. Additionally, GAIM allows for the creation of hollow structures within parts, which can significantly reduce weight without compromising strength or functionality. This is particularly advantageous in industries such as automotive, where lightweight components contribute to fuel efficiency and performance.
Furthermore, gas assist injection molding enhances design flexibility by minimizing the need for multiple injection points and eliminating the risk of weld lines or knit lines. This allows for the creation of parts with intricate geometries and cosmetic surfaces, expanding the possibilities for product innovation and differentiation.
Process Optimization and Control
Achieving optimal results with gas assist injection molding requires precise control over process parameters such as gas pressure, injection speed, and temperature. Advanced simulation software enables engineers to predict and optimize the flow of gas and molten plastic within the mold cavity, ensuring uniform filling and minimizing defects.
Moreover, real-time monitoring systems allow for continuous adjustment of process parameters during production, ensuring consistent part quality and reducing scrap rates. This level of control is essential for meeting tight tolerances and quality standards in industries with stringent requirements, such as medical devices and aerospace.
Challenges and Future Directions
Despite its numerous advantages, gas assist injection molding also presents challenges, particularly in terms of initial investment costs and complexity of equipment. Additionally, optimizing the gas flow pattern and distribution within the mold cavity remains a topic of ongoing research to further enhance part quality and production efficiency.
Future advancements in GAIM technology may focus on integrating sensors and artificial intelligence algorithms to enable autonomous process optimization and predictive maintenance. Additionally, research into new materials compatible with gas assist injection molding could expand its application to novel industries and applications.
In conclusion, gas assist injection molding represents a significant advancement in plastic manufacturing, offering unparalleled design flexibility, cost savings, and production efficiency. By harnessing the power of nitrogen gas, this innovative process has transformed the way complex plastic parts are produced, driving innovation and sustainability across various industries. As research and development continue to push the boundaries of GAIM technology, the future holds exciting possibilities for further enhancing its capabilities and expanding its reach.
GETTING A QUOTE WITH LK-MOULD IS FREE AND SIMPLE.
FIND MORE OF OUR SERVICES:
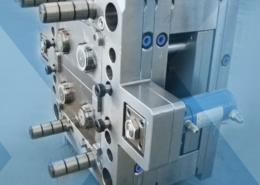
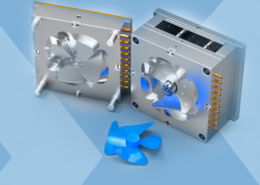
Plastic Molding
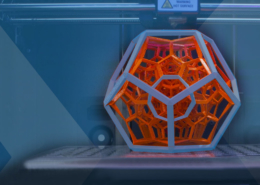
Rapid Prototyping
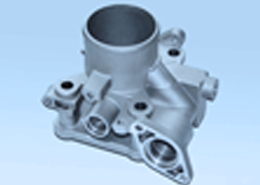
Pressure Die Casting
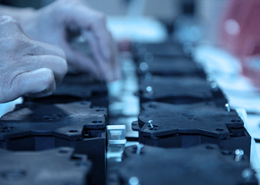
Parts Assembly
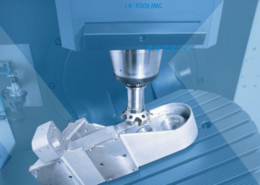