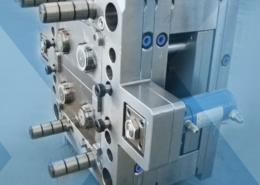
What is a precision injection mold? - precision injection
Author:gly Date: 2024-10-15
Polyphenylene sulfide (PPS) is another high-performance polymer with engineering applications. As well as having a high CST, it exhibits excellent UV and chemical resistance, making it suitable for outdoor use. PPS parts include gaskets, seals, and electrical insulation. Polyphenylsulfone (PPSU) is slightly weaker and less thermally resistant, but exhibits greater hardness.
This website contains affiliate marketing links. We may earn a commission on purchases made through these links, at no extra cost to you.
3ERP has many years of experience making prototypes and production parts via injection molding, and we can mold parts in the above materials and many more besides. Request a free quote for your next batch of high-temperature plastic parts.
Injection molding can process a wide range of materials. In addition to metals and thermosets, injection molding is suited to a large number of thermoplastic polymers, from commodity polymers like ABS to high-performance materials like PEEK.
Polyether ether ketone (PEEK) is a high-performance polymer used for engineering purposes. With a melting temperature of 343 °C, it is as robust and strong as it is difficult to process. Its extremely high CST makes it suitable for applications in demanding industries like aerospace. Example PEEK parts include bearings, pumps, and compressor plate valves.
Such a huge business would require of you to have made reserves or the necessary measures related to storage or mainly, Warehousing facilities. All the parts which are moulded or being injected would need space or some storage facilities where they can be kept without losing their quality or some major uncertain event. However, the required Warehousing space would vary on the nature of your business, or to put it in simple words, it would depend on the size of your moulded parts which you manufacture.
Specialize in CNC machining, 3D printing, urethane casting, rapid tooling, injection molding, metal casting, sheet metal and extrusion
Polyoxymethylene (POM) or acetal is another engineering thermoplastic in a lower price bracket than ultra-premium materials like PEEK. It provides good stiffness and low friction, with a relatively high CST. Molded POM can be made into various engineering parts like gears and fasteners, as well as automotive and electronics parts.
As an aspiring entrepreneur, you would have many business ideas or Start-up ideas which you would have thought of and made the necessary arrangements to implement the same. However, survey says that most of the new ventures or business ideas are related to the Manufacturing industry. There are tons of areas or industries where you can start as a manufacturer of a particular product line, depending on the demand and the potential of that product. The Injection Moulding business is one of the most demanded industry which has a huge impact in the industry and for most of the finished products.
So which are the best heat-resistant thermoplastics for injection molding? This article discusses some of the most popular thermally resistant injection molding materials, noting their respective advantages and applications, as well as discussing the complexities of using such materials during the injection molding process.
We at StartupYo facilitate aspiring entrepreneurs pursue their entrepreneurial dreams and become a trusted companion in their journey towards successful businesses.
Nylon 66 is one of the more heat-resistant polyamides (PA) that is widely used in injection molding. With good mechanical strength and rigidity, nylon 66 has applications in the automotive industry for under-the-hood components like air intake manifolds. Glass-filled PA66 has a slightly higher CST, while PA46 is another good choice for high-temp applications.
The most temperature-resistant injection molding plastics come at a high cost but exhibit excellent thermal performance, both in terms of their continuous service temperature (CST) — how much heat they can withstand over long periods of time — and their resistance to even higher temperatures in short bursts.
We select business ideas that sounds convincing for us and which also have various advantages and upsides to offer. The Injection Moulding business clearly gives the impression of huge profits for an individual, due to its mass-production feature. However, there is various other advantages of starting this venture, which are mentioned as follows.
For an ultra high-temp plastic like PEEK, the injection molding machine barrel will reach temperatures above 400 °C, with the molds around 160 °C. These high temperatures can pose certain issues, such as residue getting stuck in the barrel feeder areas. High-temp materials like PEEK often necessitate purging of the machine before use of a subsequent molding material.
Engineers sometimes need temperature-resistant moldings that do not need to be of aerospace-grade quality. In these cases, they can choose from more affordable temperature-resistant polymers with good engineering properties. (For the lowest possible budgets, engineers might select a commodity polymer like ABS, which has a reasonable CST of 90 °C but which is also sold in various “high heat” ABS formulations resisting up to 110 °C.)
Engineers will select a thermoplastic based on the requirements of the molded part. Some moldings need to be impact-resistant, some need to be food-safe, while others need to be flexible. Another property that engineers and product designers often require is heat resistance. Heat-resistant molded parts can be used in a range of situations, such as near engines, within powerful electronic parts, and in extreme outdoor environments.
Another molding consideration with high-temperature plastics is unwanted freezing off of the nozzle or mold gates. If temperatures are not quite high enough, gates or the machine nozzle can freeze off before the mold cavity is completely filled. Larger gates may mitigate this issue if it persists.
In various industries, there are certain requirements of parts and materials for many purposes. Such parts or moulds are manufactured in large quantities and reproduced and repeated again and again in the same form. Such type of manufacturing process is called as Injection Moulding Business. The process even allows you to manufacture or reproduce the same part even in the quantities of millions, this depends entirely on the tools or the machinery that you use. The Injection Moulding business follows a simple and same process throughout the time; however, it also requires efficient planning and management.
Polyetherimide (PEI), often known by the brand name Ultem, is a high-performance polymer often used as a slightly more affordable alternative to PEEK. As well as performing well in high temperatures, it offers good strength, ductility, and chemical resistance. Applications of PEI include medical components, throttle bodies, and thermostat housings.
Because the injection molding machine must melt down pellets of the chosen thermoplastics, high-temperature materials are necessarily more difficult to process. However, with the right setup, it is still possible to achieve high-quality moldings using these engineering materials.
In the manufacturing process of Injection Moulding, the key lies in lowering the production cost of your process to increase your profits. Hence, knowing and performing the most effective way of the manufacturing process is essential for every business owner who is indulged in Injection Moulding Business. The usual process of injection moulding is as follows.
Disclaimer: The information contained in this Article is for general information purposes only. The information is provided by StartupYo (SAB Weblabs Pvt.Ltd). While we endeavour to keep the information up to date and truest to the best of our knowledge, we make no representations or warranties of any kind, express or implied, about the completeness, accuracy, reliability, suitability or availability with respect to the website or the information, products, services, or related graphics contained on the website for any purpose. Any reliance you place on such information is therefore strictly at your own risk.
Polycarbonate (PC) is often used for its high-quality appearance — especially for transparent parts — and good impact resistance, but the thermoplastic also offers good heat resistance. PC can be molded for uses in electronics, automotive, and aerospace. It is also used for optical and lighting components like headlamp lenses.
GETTING A QUOTE WITH LK-MOULD IS FREE AND SIMPLE.
FIND MORE OF OUR SERVICES:
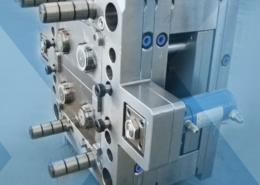
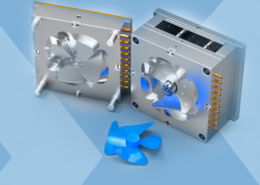
Plastic Molding
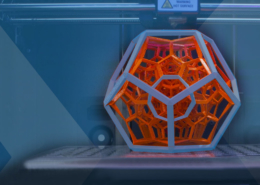
Rapid Prototyping
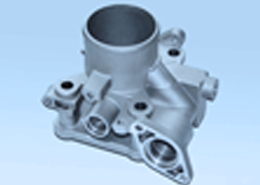
Pressure Die Casting
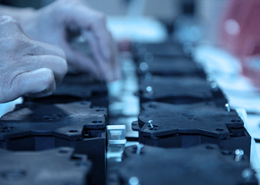
Parts Assembly
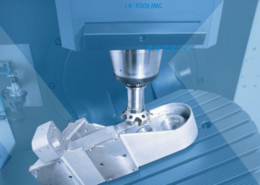