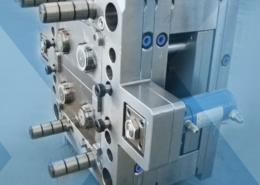
What is a reasonable cost for a plastic injection mold? - low cost plastic injec
Author:gly Date: 2024-10-15
The process of creating a new product can be a very time consuming and costly process. Here we will cover 3 basic aspects of launching a new product addressing an anticipated timeline and budget for each:
Prototyping generally takes two forms: 3D printing or short-run injection mold prototyping. Accurate can both 3D print and create short-run tooling. 3D printing is a great medium for prototyping runs of 1-10 parts generally. For prototyping runs of 50-100 or more parts, short-run injection molding tends to be more cost effective. 3D prints can have a turnaround time as little as 1-2 business days. Short-run molds tend to have a lead time of 2-3 weeks minimum. The advantages of a short-run injection mold are that it can be used for initial production and as well will offer much larger quantities of parts at a lower rate than 3D printing.
High-Density Polyethylene (HDPE) is a thermoplastic polymer supplied in pellet form for injection molding. HDPE is widely used for injection molding due to its low cost, chemical resistance, high tensile strength, impact resistance, and low moisture absorption. In addition to its physical properties, HDPE has excellent processability due to its relatively low melt temperature and low viscosity.Â
This blog series is for inventors and new businesses looking at creating a new product using the process of plastics injection molding. It’s aimed at anyone with limited experience in launching a new injection molded product.
Parts production and secondary operations will be quoted in conjunction with your mold quote. Upon approval of sample parts from your mold, the molder will be able to fulfill your orders. The pricing of parts include: mold setup and take down, materials, labor, and machine hours. For example: Mold setup and take down might be $300, materials may be $.50/part, labor might be $20/hr, and machine hours might be $50/hr. If your part has a cycle time of 30 seconds and is a 2 cavity mold then you make 2 parts each 30 seconds. Thus over 10 hours you make 2400 parts. The cost per part for an operator assisted production run would be: $300 for setup + $200 for 10hrs of labor + $500 for 10 machine hours + $1200 for materials which is a total of $2200 or a per part price of $0.917. If your order was for 600 parts your per part price would rise as the setup fee would remain the same thus your per part price goes to $1.00 for a production time of 2.5 hours.
HDPE is a thermoplastic. It can be remelted and reused if properly processed at a recycling plant. Most recycling plants will accept HDPE due to its widespread use, in addition to HDPE being one of the easiest plastics to recycle. HDPE can also be downcycled, i.e., reused on lower-value items like imitation plastic lumber.Â
In summary, with a new product you will likely spend a few weeks and a few thousand dollars on design to start, a few thousand to tens of thousands for a mold that will take a month or more to build, then finally a few thousand dollars and a couple weeks for your first production run. Accurate recommend starting a new project at least one quarter before you plan to begin production.
HDPE has low thermal conductivity. If cooling is too quick or uneven, this can result in the part warping or shrinking during injection molding. HDPE can have a shrinkage rate of between 1.5% and 4.0%.
Get custom HDPE injection molded prototypes and production parts in as few as five business days. Dozens of materials and finishes are available. ISO 9001:2015, ISO 13485, IATF 16949:2016, and AS9100D certified.
Accurate has an in-house tool shop and can quote your mold for tooling both in-house or made in China. Tooling quotes usually take 5 business days due to the complexity of quoting a new mold. We quote all large molds (for machines larger than 300 tons) using our Chinese supplier. All other molds are quoted in-house unless requested. Lead time on a mold varies greatly according to the current workload in the shop and the complexity of the mold. In general lead times are 4-12 weeks and include the 1-2 weeks it will take to sample your mold. Shop hours for mold makers are in the $80/hr - $125/hr range. Molds can take 30-80 hours to build, or longer.
Choose from millions of possible combinations of materials, finishes, tolerances, markings, and certifications for your order.
HDPE is a popular material for garden furniture due to its low cost. The strength and toughness of HDPE make it possible to produce lightweight and low-cost furniture without compromising mechanical strength. HDPE can also be downcycled for use in imitation lumber that can be used to produce low-cost furniture.Â
Injection molding HDPE requires a large amount of initial capital investment as the tooling can be very expensive. It is only cost-effective for larger production volumes. Listed below are two potential alternatives to HDPE injection molding:
HDPE has a density of around 960 kg/m3. This is lightweight compared to metals and even some plastics. HDPE also has a high strength-to-weight ratio which means it can be used to produce thin-walled products like bottles or chemical tanks but still maintain high levels of strength and rigidity.
HDPE is considered food-safe and is approved by the FDA. It is widely used for both single-use and long-term food storage applications. In addition, HDPE is very tough and can protect the food contents during transportation.Â
Hard hats must be able to withstand sudden impacts and must also absorb as much of the impact energy as possible. As such, HDPE is an excellent choice for hard hats as it is a highly durable and impact-resistant material.Â
HDPE is considered food-safe by the FDA (Food and Drug Administration) and is widely used to store food items. HDPE is highly inert and stable and as such does not leach dangerous chemicals into food products.Â
Each HDPE formulation will have a unique set of material properties depending on their intended application. Table 1 below lists some common material properties of standard HDPE:
Accurate can also offer some basic assembly and finishing services. As a custom molder we can do assembly, decorating, inserting, drilling, and other services. These services would be quoted on a per part basis upon request, usually at the same time as quoting the production of parts.
As a custom molder Accurate offers a wealth of experience in metal to plastic conversions as well as reengineering parts to eliminate gluing and other secondary operations. Accurate is experienced with over molding and the use of blowing agents for thicker walled parts. We would be happy to speak with you about the specifics of your project.
Industrial Design rates run from approx. $85/hr to $125/hr. Most designers need at least 2 weeks to turn around a design with the number of hours required varying greatly according to the project and the number of revisions after an initial design. Expect that your designer will need a few business days to quote your design work and to pay at least a 50% deposit to get started. The balance will be due before you will obtain your design files. Please note that you should obtain transferable files upon payment in full. These are files with your design that can be revised by another designer if necessary and of which you have full rights to the design.
HDPE has poor UV resistance as the carbon-hydrogen bonds are attacked by UV radiation. The breaking of these bonds ultimately causes photo-oxidation which degrades the material over time. Additives like UV stabilizers can be incorporated into the HDPE formulation to improve its UV resistance.Â
Xometry offers the highest quality HDPE injection molding service and is able to assist with the design of the part and tooling to ensure it follows DFM (Design for Manufacturing) best practices. This will help ensure the product can be successfully manufactured with no defects. Thereafter, Xometry can facilitate manufacturing with one of our trusted partners to ensure the parts are produced to the required specifications. HDPE is a popular injection molding material as it has excellent processability. HDPE also has a low moisture absorption rate and is lightweight, making it ideal for a wide range of applications.Â
Plastic bottles are one of the most popular uses for HDPE. While most bottles are formed using blow molding techniques, the blank tubes used to make these bottles must be injection molded. HDPE does not leach into the stored liquid and is highly moisture-resistant, making it ideal for bottling applications.Â
With a 3D part design in hand along with a proof of concept prototype you are ready to quote a mold. The mold designer will need your 3D design files and will take those and may need to make some small adaptations to the part that will reap benefits when molded. The mold designer will need approval for these changes and you can verify the impact on your parts with your industrial designer before approving the changes requested.
HDPE is susceptible to environmental stress cracking. When exposed to long-term tensile loads, cracks can form in the material. This is further exacerbated if the HDPE is exposed to a corrosive environment. These cracks can develop at loads much lower than the tensile strength of the material.Â
In Part 3, join us to learn more about how to make your parts and mold cost less, and how to ensure you have enough cash flow to start you project.
HDPE is highly resistant to moisture and is relatively flexible. As such, it is widely used for piping to transport large volumes of water. Individual pipe sections are welded together to eliminate potential leaks. These pipes are often buried underground.Â
In summary ensure you have a few thousand dollars set aside for design and prototyping. In addition expect a timeline minimum of 2-3 weeks plus revisions.
Terms usually include 50% due at the time of placing an order, 25% on mold completion, and 25% due upon approval of sample parts.
HDPE is highly resistant to moisture ingress. Also, with the addition of UV (ultraviolet) stabilizers, HDPE can be made resistant to UV radiation, making it an ideal material for outdoor applications.Â
HDPE is considered a commodity plastic and is relatively low-cost when compared to other plastics like polypropylene, for example. This makes it a cost-effective material to use for injection molded products. It must, however, be noted that the tooling required for injection molding is often the largest contributor to initial set-up cost.Â
The initial phase of creating a 3D design will mean employing an Industrial Designer who can turn your idea into a 3D rendering that can be passed along to a toolmaker for mold design. At this time you may also look to take advantage of 3D printing technology to get a proof of concept.
GETTING A QUOTE WITH LK-MOULD IS FREE AND SIMPLE.
FIND MORE OF OUR SERVICES:
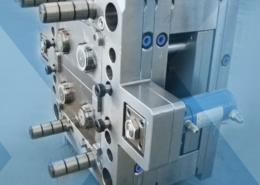
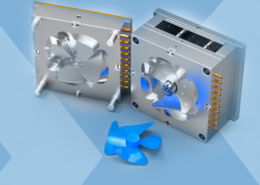
Plastic Molding
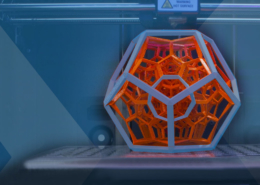
Rapid Prototyping
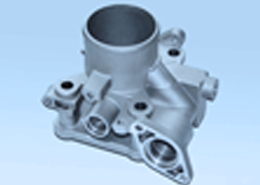
Pressure Die Casting
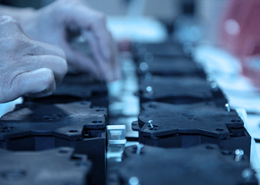
Parts Assembly
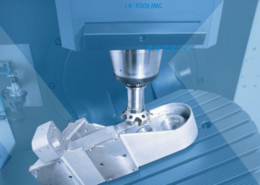