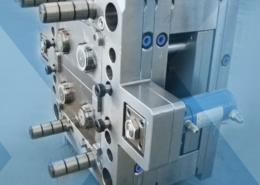
What Is Delrin? - delrin injection molding
Author:gly Date: 2024-10-15
If you want to produce high-quality machined parts with a sleek appearance, it’s essential to consider some critical factors related to CNC machining.
This molten resin then enters the mold cavity. However, the resin injection mechanism does not fill up the mold since the product has hollow sections. The amount of injected resin material depends upon the volume of the part. It typically depends on geometrical factors like wall thickness, ribbed features, holes, etc. Usually, around ~70%-80% of the mold fills up with plastic material.
The choice of materials in injection moulding isn’t arbitrary. It requires a careful balancing act between functionality, safety, and cost.
These include the intended use, the environment in which the device will operate, and the complexities of human anatomy.
Hence, there is a secondary gas penetration phase where more gas flows into the mold to fill up these gaps. This maintains uniform pressure and guarantees a neat fill.
The industry is making strides towards sustainability, reducing its environmental footprint while maintaining product quality.
Moreover, parts with large surfaces and curved profiles are tackled quite efficiently. The gas channels are in line with the entire surface, allowing the gas to apply pressure all over the wide surface area. As a result, manufacturing large surfaces is not a considerable issue.
A major advantage of this manufacturing technique is that it can handle a wide range of plastic materials. We will discuss below the main plastic materials compatible with this process.
Injection moulding in medical device manufacturing isn't just a process; it's a pillar of modern medicine. Its role, often understated, is undeniably critical, shaping the future of healthcare one device at a time. As technology advances, so will the capabilities of injection moulding, promising even more innovative and life-changing medical devices.
Injection moulding, at its core, is the art of crafting objects by injecting molten material into a mould. It's akin to a modern-day alchemy where raw plastics transform into life-saving devices.
In an industry where sterility is paramount, injection moulding rises to the occasion, employing stringent sterilisation protocols.
The resin melts due to external heating and friction while the constantly decreasing pitch of the screw compresses it to pressurize it. For gas assist molding, pressure is lower than conventional injection molding as there is less material to pack into the mold due to hollow sections. Also, since the pressure comes from gas rather than a thick, viscous liquid, there are lower viscosity-based frictional losses inside the pressurized media itself.
It is a very popular method to manufacture large, hollow molded plastic parts. It enjoys numerous advantages such as remarkable surface finish and geometric accuracy.
After the required amount of resin enters the mold, the process of primary gas penetration begins. A pressurized gas source releases nitrogen into the spruce network, which forms a bubble inside the resin material.
External gas assisted injection molding is fundamentally different from the internal process. The gas does not penetrate the material to create hollow sections. Rather, it enters into the mold through microchannels from one side only. It packs the molten resin against the mold’s walls by applying pressure from the backside/non-aesthetic side of the part.
Gas assisted molded parts to have various applications. Generally, it is for injection molding hollow parts with ribbed/boss features and smooth surface finish requirements.
Quality control is the guardian angel of injection moulding, ensuring each product meets the highest standards of safety and efficacy.
In addition to good surface quality, this technique also allows for thicker sections due to better packing and shrinkage-countering ability. Especially, for ribbed/boss features the rib/wall ratio can be up to 1, which is much better than some other methods. This lends strength and stability to the molded part.
Selecting an injection moulding services partner is a decision that echoes through every device produced, impacting countless lives.
Gas assist has several pros that make it the go-to technique for many manufacturers. Summarized below are all of its main advantages and disadvantages.
Towards the end of the primary gas penetration phase, the resin starts to cool down and contract. Due to the gap created by this thermal contraction, the gas pressure slightly decreases. This can cause part deformations and induce geometric errors, which are never desirable.
In this article, we dive deep into this manufacturing process and discuss what it is and its types, applications, and materials.
The manufacturing sector is one of the most innovative in today’s fast-paced world, setting new standards with each stride. Gas assisted injection molding is one such novel plastic manufacturing technique that offers great product quality.
Gas assisted injection molding is a plastic molding process that combines principles of conventional injection molding with the application of pressurized inert gas. It uses mold cavities in the form of the product’s shape. The mold is partially filled with ~70%-80% molten plastic raw material. Injecting Nitrogen gas fills the remaining volume to pack the plastic material against the mold’s walls.
Plastic manufacturing is a versatile field that is continually developing. When it comes to complex geometries and top-of-the-class manufacturing capabilities, gas-assisted injection molding is one of the number one options.
Delving into the specifics of injection moulding reveals a complex yet elegant process. It's a ballet of machinery, materials, and meticulous control, choreographed to produce precision medical devices.
The gas assisted injection molding process has two main types, external and internal. It also follows a specific workflow with three steps. In the following sections, we distinguish between the two types and explain the step-by-step procedure.
For your plastic parts, RapidDirect can help you become more competitive in your market through our specialized injection molding services!
Internal gas assisted molding is more widely used than the external process, so we shall discuss it first. Initially, molten plastic resin enters the mold through spruce channels. Then, the gas enters through a nozzle and forms a bubble inside the molten resin. The pressure of the growing gas bubble forces the resin against the walls of the mold, giving the parts their shape.
The gas assist injection molding process takes place in three stages (refer to the injection molding diagram below). Each stage constitutes an important step of the process and requires design sense and practical skill from the manufacturing team.
To facilitate our customers, we have developed an efficient online quotation platform that provides rapid quotes based on the design files you upload. Augmenting these quotes is a detailed design feasibility analysis and DFM feedback, which is just one example of the personalized attention you will get here at RapidDirect. Contact us to get in touch with our team for your custom plastic manufacturing needs.
The pressure and growing volume of the gas bubble push the molten resin to the boundaries of the mold. The pressure of the gas remains constant during this process, ensuring that the resin reaches all corners of the mold, filling it up.
The extremely high level of precision needed within the aerospace industry makes CNC machining a suitable manufacturing process for the sector.
Our state-of-the-art equipment and years of experience guarantee that you will get high-quality plastic parts that will help you beat the competition.
This process is well-known for its fine surface finish quality. Since the gas pressure acts uniformly on the non-aesthetic side, the opposite end tightly packs into the mold extremities, taking its exact shape. The resultant surface is so precise that it also includes fine textures and patterns of the mold. Consequently, external gas assisted molding is preferable if the part has surface patterns and imprints.
The medical industry has found a steadfast ally in injection moulding. Elia Guidorzi, international marketing executive at Tecni Waterjet discusses how this technique plays a crucial role in healthcare advancements.
At first, the mold clamps shut, and raw resin is fed into the hopper of the injection molding equipment. Just as in a regular injection molding process, the machine melts and pressurizes the resin in its screw-feed section.
This process is well-suited to manufacture hollow, lightweight geometries. Additionally, the gas exerts constant pressure on the resin, which helps to minimize shrinkage and distortion/warpage. These factors are usually the main reason for the deteriorating dimensional accuracy of thin walls. Thus, thin-walled parts are another special application of this process.
Its roots stretch back to the late 19th century, evolving from producing combs and buttons to intricate medical components. This journey has been marked by continuous refinement and adaptation, mirroring the medical field's own evolution.
Now that you know about the ins and outs of gas assisted injection molding, it is time to know who does it best. RapidDirect is your best choice in injection molding services. Our ever-growing establishment boasts a talented team of professional engineers and technicians, supported by powerful manufacturing capabilities. For our esteemed clientele, we offer plastic manufacturing services in a wide variety of plastic materials.
The future of injection moulding in medical applications is bright, fuelled by relentless innovation and technological advancements.
Cycle times are also significantly lower for internal gas assisted molding. Due to the geometries having hollow portions and thin cross-sections, they cool down quickly in comparison to solid parts.
GETTING A QUOTE WITH LK-MOULD IS FREE AND SIMPLE.
FIND MORE OF OUR SERVICES:
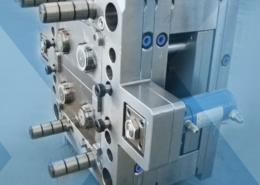
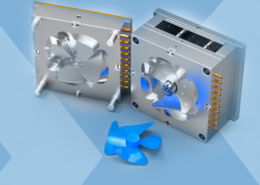
Plastic Molding
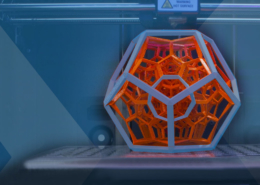
Rapid Prototyping
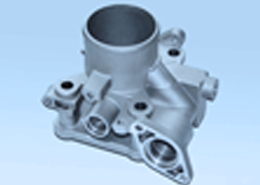
Pressure Die Casting
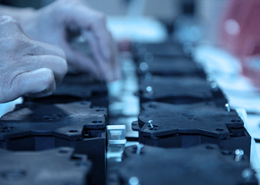
Parts Assembly
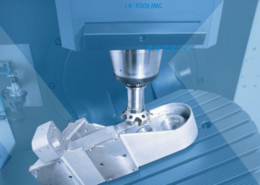