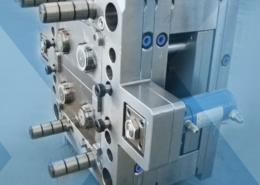
What is Design of Experiments (DOE) in Scientific Molding? - scientific plastic
Author:gly Date: 2024-10-15
Hot Runner Temperature Controller also called HRTC in short form. Hot runner temperature controller is used to run mainly Plastic Injection Molding Machine's molds. Let's try to understand 2 main types of molds. Hot Runner vs Cold Runner Injection Mold: Key Differences You Need to Know   Home Blog Hot Runner vs Cold Runner Injection Mold: Key Differences You Need to Know Hot Runner vs Cold Runner Injection Mold: Key Differences You Need to Know Updated: October 17, 2022 An injection mold is a component designed according to the intended product using processes such as CNC machining and is where the molten plastic is injected and cooled. There are several injection molds types. However, based on the temperature held by the runner and the mold,  there are two mold systems: hot runner and cold runner. Each mold system uses a different mechanism which affects plastic fabrication differently. As a result, there is a need for a proper understanding of the hot runner mold vs cold runner mold comparison before selection. This article does the hot runner vs cold runner injection molding comparison by introducing both systems, how they work, and their differences. Furthermore, it shows how to choose the right mold for your project.   What is a Hot Runner Mold?  A hot runner mold is an injection mold with a manifold system (i.e., containing a heating component, manifold, and nozzle) that ensures that molten plastic injected into the mold maintains its temperature. Hot runner injection molding is suitable for molding plastics that require steady flow and injection pressure for part fabrication. Furthermore, with the method, there is a reduction in defects such as sink marks that occur due to fluctuating injection pressure and underfilled molds. Types of Hot Runner Mold Based on the method of maintaining the heat, here are the two types of hot runner molds used in plastic injection molding: Insulated Hot Runners Insulated hot runners molds have extremely thick runners in the mold plate, which causes part of the molten plastic to cool down and insulate the system. The insulation reduces heat loss, allowing the mold system to maintain an open plastic flow. Insulated hot runner molds are less expensive than heated ones because they do not use manifolds and drops. Furthermore, they have flexible gates, reduced defects, and favor easy color change. However, it has a few disadvantages, such as freeze-ups at the gate, non-uniform mold filling, long start-up periods, and the need for a fast cycle to maintain the thermoplastic molten state due to the absence of a manifold system.  Heated hot runners The heated hot runner is the major type of hot runner system with heating achievable using a heating component in one-half of the mold. However, they come in two designs: externally heated and internally heated. Externally heated hot runners: The heating component is outside the mold. As a result, there is no obstruction in the molten thermoplastic flow (better flow control) and no drop in injection pressure. Furthermore, the molten plastic does not freeze and is ideal for color change. Externally heated hot runner molds are suitable for thermosensitive materials. Internally heated hot runners: Here, the heating component is in the mold, leading to a drop in injection pressure, incompatibility with color change, and material hanging up and degrading in the mold. However, there is better flow due to the heated runner and gate tip control. What is a Cold Runner Mold?  A cold runner mold is the basic injection mold with runners at the same temperature as the mold cavity. The system involves injecting the molten plastic into locating ring. Afterward, the molten plastic passes through a sprue and runner, which are cold, before entering the mold cavity. As a result, when the plastic cools, it takes the shape of the mold cavity with the solidified plastic in the runner attached. The cold-runner mold features a large runner (larger than the part), removing the tendency of underfilling the mold. Aside from that, it is suitable for working with any plastic polymer irrespective of heat sensitivity, is less expensive than hot runners, and is easily maintained. However, they generate waste. Types Of Cold Runner Systems There are two types of cold runner molds system based on the number of mold plates: · Two Plate Cold Runner System The two-plate cold runner system comprises two plates with the stationary mold containing the sprue, runners, gate, and cavities. It is the fastest, simplest, and least costly cold runner system. However, the runner is attached to the final product and should be cut off. · Three Plate Cold Runner System A three-plate cold runner system is similar to the two-plate system. However, the three-plate injection mold is flexible with an additional runner plate. Furthermore, there is no need to cut the runner from the injection molded part, and the mold does not require an ejection system for part removal. 3 plate injection mold is friendlier and more flexible. They are the most suitable for working with products with complex designs, and they are a lower-cost alternative to hot runner systems. Disadvantages of this injection mold include long cycle time, complex tool design, and high material waste. Hot Runner Mold vs Cold Runner Mold â Advantages of Each System Each runner mold has its advantages making them suitable for different applications and industries. Here, we will talk about their advantages and how they compare. Hot Runner System Advantages The hot runner system is widely applicable in plastic product fabrication due to the following advantages: Reduced cycle time: One main difference between a hot runner and cold runner injection molding is the cycle time. Hot runner injection molds have a faster cycle time due to the plastic being kept at optimum temperature, increasing flowability. Reduced material wastage: Itâs more cost-effective as the mold system generates little to no material waste.    Optimal Part Quality: Parts made using hot runner molds have better final quality due to the excellent filling profile and injection pressure.  Molding Automation: Automation is possible because there is no need for post-processing processes such as trimming, waste recycling, and removal of runners.  Design Flexibility: There is flexibility in injection mold design in the placement of the gate using the hot tip gate, valve gate, or edge gate. As a result, there is an increase in part aesthetics and optimum filling of mold cavities during the injection. Cold Runner System Advantages The cold runner system has the following advantages: Lower tooling cost: The cold runner mold system has a lower investment cost in injection mold tooling. As a result of the lower tooling cost, molding is cost-effective. Less inspection and maintenance cost: Cold runner molds are not complex. Consequently, there is less need for inspection and maintenance, leading to decreased maintenance costs and downtime. Thermosensitive plastics: Another difference between hot runner and cold runner molds is their application in molding thermosensitive plastics. Cold runner systems are the most suitable for thermally sensitive polymers. Furthermore, they are also suitable for any plastics. Hot Runner Mold vs Cold Runner Mold â Drawbacks of Each System Each runner mold also has its drawbacks. Here, we will talk about their disadvantages and how they compare to each other. Hot Runner System Disadvantages The hot runner system has the following disadvantages: High investment cost: Hot runner systems have a high initial investment and maintenance cost due to the sophistication of the molds and advantages such as reduced cycle time, part quality, and flexibility. High requirement for precision in the equipment: The system requires high-end equipment due to the need for precision. Otherwise, there might be defects because of failure in the machine. An example is the plastic seal failure which can lead to the molten plastic spilling and damaging the hot runner assembly. Cold Runner System Disadvantages Cold runner injection molding has the following disadvantages: Material wastage: Material waste is another difference in the hot runner vs cold runner molding comparison. The molten plastic solidifies in the cold runner system. Consequently, these lead to scraps that need trimming. Injection pressure drop: Heat transfers from the plastic to the mold plates during plastic flow, which causes shrinkage leading to pressure drop and further forming defects such as sink marks and underfilling parts. High cycle time: Cold injection molding has a slower cycle time due to reduced plastic flowability. Aside from that, removing the runner and sprue (especially in the two mold systems) also increases the cycle time.
Energy Monitoring Systems: These systems track the total energy consumption of the injection molding machine, highlighting areas where energy efficiency can be improved.
For more information on materials and machine settings in injection molding, refer to the Injection Molding Material Wikipedia page and the Injection Molding Machine Wikipedia page.
The quality of the plasticizing process directly impacts product quality and lifespan. Uniform melting ensures defect-free products, enhancing both aesthetic and functional attributes. Products with proper plasticizing exhibit enhanced mechanical properties and durability.
Barrel Temperature: Precision in controlling barrel temperatures, typically between 200°C and 300°C, is necessary for achieving the desired melt quality.
Screw Diameter and L/D Ratio: A larger screw diameter, typically ranging from 18mm to 150mm, can handle higher volumes of material, impacting the throughput rate and melting efficiency. The L/D (length to diameter) ratio, ideally between 20:1 and 24:1, is critical for effective plastic melting and mixing.
Plasticizing in injection molding is the essential process where solid plastic pellets are transformed into a molten state, ready for molding. This process depends on a screw mechanism within the injection machine, combining heat and mechanical work to melt the plastic. Its efficiency plays a pivotal role in determining the quality of the molded product, ensuring the plastic’s uniformity and flow properties.
Plasticizing capability in injection molding refers to the process of heating and melting plastic resin to make it fluid and ready for injection into a mold cavity, ensuring proper flow and filling.
Currently it only shows your basic business info. Start adding relevant business details such as description, images and products or services to gain your customers attention by using Boost 360 android app / iOS App / web portal.
Motor Power: Motor power, generally in the 15 to 50 kW range, is essential for driving the screw and melting the plastic.
Thermal Imaging Cameras: These are used to monitor barrel temperatures, ensuring optimal heat distribution and identifying potential issues like cold spots that can affect material consistency.
Data Logging and Analysis Software: This software tracks and analyzes machine parameters like cycle time, temperature profiles, and energy consumption, providing real-time insights into the efficiency of the plasticizing process.
For a deeper understanding of optimizing plasticizing processes, you can refer to the Injection Molding Optimization Wikipedia page.
To assess plasticizing efficiency in injection molding, several key metrics and performance indicators are crucial. Cycle Time is a primary metric, typically measured in seconds; the shorter the cycle time, the higher the efficiency, indicating a faster conversion of raw material into a molten state. Energy Consumption per Cycle, measured in kilowatt-hours (kWh), is another critical indicator. Efficient plasticizing processes consume less energy, often below 0.5 kWh per cycle for optimized systems. Material Consistency, evaluated through product quality checks, reflects the uniformity and stability of the plasticized material, directly impacting the final product’s quality.
Viscosity Measuring Devices: These tools measure the viscosity of the molten plastic, a critical factor in determining the efficiency of the plasticizing process. Ideal viscosity ranges are material-specific, but consistent readings are indicative of efficient plasticizing.
Back Pressure: This affects the degree of mixing and melting. Higher back pressure, within a range of 5 to 20 bar, can improve color dispersion and material consistency but may increase wear on the screw and barrel.
Efficient plasticizing significantly influences production costs and efficiency. Optimizing this process allows for faster cycle times and reduced energy use, leading to substantial cost savings. A 10% decrease in cycle time can lead to a similar reduction in production expenses. Furthermore, it can minimize material waste, enhancing cost-effectiveness.
To explore more about efficiency measurement in injection molding, consider visiting the Injection Molding Process Wikipedia page.
The choice of material plays a pivotal role in determining the plasticizing capability in injection molding. Different materials require distinct temperatures and pressures for effective plasticizing. For instance, polycarbonate needs temperatures around 280°C to 320°C, whereas polyethylene may melt effectively at temperatures as low as 180°C to 220°C. The viscosity of the material also dictates the required screw speed and back pressure, directly influencing the energy consumption. Materials with higher viscosity often need more power, potentially increasing the motor requirement up to 50 kW or more, depending on the size of the machine.
Clamp Force: Essential for holding the mold closed during injection, clamp force (measured in tons) depends on the size of the mold and the material being used. Larger parts with more complex designs typically require higher clamp forces.
The configuration and settings of the injection molding machine significantly affect plasticizing. Key parameters include:
Injection Speed and Pressure: These parameters, tailored to the specific material and product design, influence the quality of the final product. Higher speeds and pressures can reduce cycle times but may introduce defects if not properly managed.
Hot Runner Temperature Controller also called HRTC in short form. Hot runner temperature controller is used to run mainly Plastic Injection Molding Machine's molds. Let's try to understand 2 main types of molds. Hot Runner vs Cold Runner Injection Mold: Key Differences You Need to Know   Home Blog Hot Runner vs Cold Runner Injection Mold: Key Differences You Need to Know Hot Runner vs Cold Runner Injection Mold: Key Differences You Need to Know Updated: October 17, 2022 An injection mold is a component designed according to the intended product using processes such as CNC machining and is where the molten plastic is injected and cooled. There are several injection molds types. However, based on the temperature held by the runner and the mold,  there are two mold systems: hot runner and cold runner. Each mold system uses a different mechanism which affects plastic fabrication differently. As a result, there is a need for a proper understanding of the hot runner mold vs cold runner mold comparison before selection. This article does the hot runner vs cold runner injection molding comparison by introducing both systems, how they work, and their differences. Furthermore, it shows how to choose the right mold for your project.   What is a Hot Runner Mold?  A hot runner mold is an injection mold with a manifold system (i.e., containing a heating component, manifold, and nozzle) that ensures that molten plastic injected into the mold maintains its temperature. Hot runner injection molding is suitable for molding plastics that require steady flow and injection pressure for part fabrication. Furthermore, with the method, there is a reduction in defects such as sink marks that occur due to fluctuating injection pressure and underfilled molds. Types of Hot Runner Mold Based on the method of maintaining the heat, here are the two types of hot runner molds used in plastic injection molding: Insulated Hot Runners Insulated hot runners molds have extremely thick runners in the mold plate, which causes part of the molten plastic to cool down and insulate the system. The insulation reduces heat loss, allowing the mold system to maintain an open plastic flow. Insulated hot runner molds are less expensive than heated ones because they do not use manifolds and drops. Furthermore, they have flexible gates, reduced defects, and favor easy color change. However, it has a few disadvantages, such as freeze-ups at the gate, non-uniform mold filling, long start-up periods, and the need for a fast cycle to maintain the thermoplastic molten state due to the absence of a manifold system.  Heated hot runners The heated hot runner is the major type of hot runner system with heating achievable using a heating component in one-half of the mold. However, they come in two designs: externally heated and internally heated. Externally heated hot runners: The heating component is outside the mold. As a result, there is no obstruction in the molten thermoplastic flow (better flow control) and no drop in injection pressure. Furthermore, the molten plastic does not freeze and is ideal for color change. Externally heated hot runner molds are suitable for thermosensitive materials. Internally heated hot runners: Here, the heating component is in the mold, leading to a drop in injection pressure, incompatibility with color change, and material hanging up and degrading in the mold. However, there is better flow due to the heated runner and gate tip control. What is a Cold Runner Mold?  A cold runner mold is the basic injection mold with runners at the same temperature as the mold cavity. The system involves injecting the molten plastic into locating ring. Afterward, the molten plastic passes through a sprue and runner, which are cold, before entering the mold cavity. As a result, when the plastic cools, it takes the shape of the mold cavity with the solidified plastic in the runner attached. The cold-runner mold features a large runner (larger than the part), removing the tendency of underfilling the mold. Aside from that, it is suitable for working with any plastic polymer irrespective of heat sensitivity, is less expensive than hot runners, and is easily maintained. However, they generate waste. Types Of Cold Runner Systems There are two types of cold runner molds system based on the number of mold plates: · Two Plate Cold Runner System The two-plate cold runner system comprises two plates with the stationary mold containing the sprue, runners, gate, and cavities. It is the fastest, simplest, and least costly cold runner system. However, the runner is attached to the final product and should be cut off. · Three Plate Cold Runner System A three-plate cold runner system is similar to the two-plate system. However, the three-plate injection mold is flexible with an additional runner plate. Furthermore, there is no need to cut the runner from the injection molded part, and the mold does not require an ejection system for part removal. 3 plate injection mold is friendlier and more flexible. They are the most suitable for working with products with complex designs, and they are a lower-cost alternative to hot runner systems. Disadvantages of this injection mold include long cycle time, complex tool design, and high material waste. Hot Runner Mold vs Cold Runner Mold â Advantages of Each System Each runner mold has its advantages making them suitable for different applications and industries. Here, we will talk about their advantages and how they compare. Hot Runner System Advantages The hot runner system is widely applicable in plastic product fabrication due to the following advantages: Reduced cycle time: One main difference between a hot runner and cold runner injection molding is the cycle time. Hot runner injection molds have a faster cycle time due to the plastic being kept at optimum temperature, increasing flowability. Reduced material wastage: Itâs more cost-effective as the mold system generates little to no material waste.    Optimal Part Quality: Parts made using hot runner molds have better final quality due to the excellent filling profile and injection pressure.  Molding Automation: Automation is possible because there is no need for post-processing processes such as trimming, waste recycling, and removal of runners.  Design Flexibility: There is flexibility in injection mold design in the placement of the gate using the hot tip gate, valve gate, or edge gate. As a result, there is an increase in part aesthetics and optimum filling of mold cavities during the injection. Cold Runner System Advantages The cold runner system has the following advantages: Lower tooling cost: The cold runner mold system has a lower investment cost in injection mold tooling. As a result of the lower tooling cost, molding is cost-effective. Less inspection and maintenance cost: Cold runner molds are not complex. Consequently, there is less need for inspection and maintenance, leading to decreased maintenance costs and downtime. Thermosensitive plastics: Another difference between hot runner and cold runner molds is their application in molding thermosensitive plastics. Cold runner systems are the most suitable for thermally sensitive polymers. Furthermore, they are also suitable for any plastics. Hot Runner Mold vs Cold Runner Mold â Drawbacks of Each System Each runner mold also has its drawbacks. Here, we will talk about their disadvantages and how they compare to each other. Hot Runner System Disadvantages The hot runner system has the following disadvantages: High investment cost: Hot runner systems have a high initial investment and maintenance cost due to the sophistication of the molds and advantages such as reduced cycle time, part quality, and flexibility. High requirement for precision in the equipment: The system requires high-end equipment due to the need for precision. Otherwise, there might be defects because of failure in the machine. An example is the plastic seal failure which can lead to the molten plastic spilling and damaging the hot runner assembly. Cold Runner System Disadvantages Cold runner injection molding has the following disadvantages: Material wastage: Material waste is another difference in the hot runner vs cold runner molding comparison. The molten plastic solidifies in the cold runner system. Consequently, these lead to scraps that need trimming. Injection pressure drop: Heat transfers from the plastic to the mold plates during plastic flow, which causes shrinkage leading to pressure drop and further forming defects such as sink marks and underfilling parts. High cycle time: Cold injection molding has a slower cycle time due to reduced plastic flowability. Aside from that, removing the runner and sprue (especially in the two mold systems) also increases the cycle time.
Barrel Temperature Settings: Precise temperature control is crucial. Inadequate heating can lead to poor melting, while overheating can degrade the material. Most machines have multiple heating zones, each requiring specific temperature settings based on the material used.
Plasticizing’s role in injection molding is crucial. It directly affects the mold filling characteristics and the end product’s quality. Proper plasticizing ensures that the plastic has an appropriate viscosity for even and complete mold filling, leading to products with consistent dimensions and structural integrity. This is vital for shortening cycle times, enhancing production efficiency, and lowering costs.
Screw Design: A crucial factor, where screws with optimal length-to-diameter ratios (around 20:1) provide enhanced melting and mixing.
GETTING A QUOTE WITH LK-MOULD IS FREE AND SIMPLE.
FIND MORE OF OUR SERVICES:
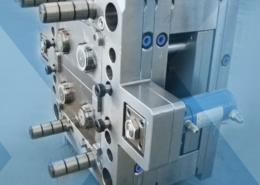
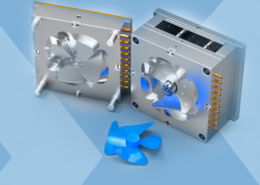
Plastic Molding
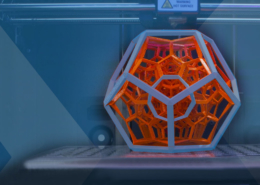
Rapid Prototyping
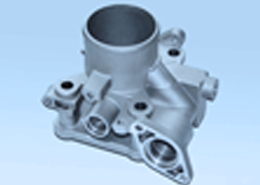
Pressure Die Casting
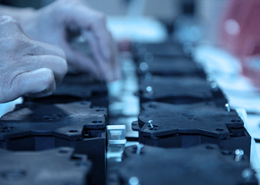
Parts Assembly
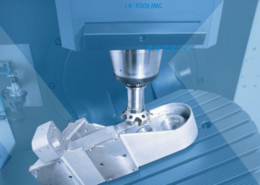