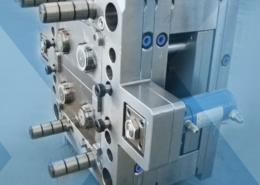
What is double injection molding? Simple Guide to 2 Shot ... - two part injectio
Author:gly Date: 2024-10-15
The pressure and growing volume of the gas bubble push the molten resin to the boundaries of the mold. The pressure of the gas remains constant during this process, ensuring that the resin reaches all corners of the mold, filling it up.
For your plastic parts, RapidDirect can help you become more competitive in your market through our specialized injection molding services!
Now that you know about the ins and outs of gas assisted injection molding, it is time to know who does it best. RapidDirect is your best choice in injection molding services. Our ever-growing establishment boasts a talented team of professional engineers and technicians, supported by powerful manufacturing capabilities. For our esteemed clientele, we offer plastic manufacturing services in a wide variety of plastic materials.
Prototype injection moulding is a versatile and efficient method for creating detailed and functional prototypes. It plays a crucial role in product development, allowing for thorough testing and evaluation before a product goes into full-scale production.
In this article, we dive deep into this manufacturing process and discuss what it is and its types, applications, and materials.
Internal gas assisted molding is more widely used than the external process, so we shall discuss it first. Initially, molten plastic resin enters the mold through spruce channels. Then, the gas enters through a nozzle and forms a bubble inside the molten resin. The pressure of the growing gas bubble forces the resin against the walls of the mold, giving the parts their shape.
ACIS®, Autodesk Inventor®, CATIA® V5,Creo™ Parametric, IGES, Parasolid®, Pro/ENGINEER®,Siemens PLM Software’s NX™, SolidEdge®, SolidWorks®, STEP
Prototype injection moulding is utilized across a wide range of industries due to its versatility and efficiency. In the automotive industry, it is used to create prototypes of parts such as dashboards, door handles, and engine components. The medical industry also heavily relies on this process for the development of medical devices and equipment, such as surgical tools and diagnostic devices.Other industries that commonly use prototype injection moulding include electronics, where it is used to create prototypes of components for devices like smartphones and computers, and the aerospace industry, where it is used in the development of parts for aircraft and spacecraft. The consumer goods industry also benefits from this process, using it to create prototypes for products ranging from kitchen appliances to toys.
Design Complexity: If your design is complex with intricate details, methods like Stereolithography (SLA) or Selective Laser Sintering (SLS) may be more suitable due to their high precision. For simpler designs, Fused Deposition Modeling (FDM) or CNC machining might be sufficient.Material Requirements: The choice of prototyping method can also depend on the material choice you intend to use. For example, if you plan to use thermoplastics, FDM or prototype injection moulding might be the best choice. For metal prototypes, you might opt for CNC machining or Direct Metal Laser Sintering (DMLS).Quantity: If you need a large number of prototypes, methods like rapid injection moulding or FDM can be more cost-effective due to their scalability. For a small number of highly detailed prototypes, SLA or SLS might be more suitable.Budget and Time Constraints: Faster methods like FDM or rapid injection moulding can be more suitable if you’re working under tight deadlines. However, if budget is a concern, you might need to balance the speed of production with the costs involved.End-Use: If the prototype is for functional testing or end-use, you might need a method that produces durable and functional parts, like prototype injection moulding or CNC machining.
It is a very popular method to manufacture large, hollow molded plastic parts. It enjoys numerous advantages such as remarkable surface finish and geometric accuracy.
Prototype injection moulding is a manufacturing process that involves the use of injection moulds to create prototypes of a product. This process is often used in the early stages of product development to test the design, functionality, and feasibility of a product before it goes into mass production. The prototype injection moulding process involves injecting molten material, often plastic, into a mould which then cools and solidifies to form the desired shape. This method allows for a high degree of precision and is ideal for creating complex shapes and designs.
The resin melts due to external heating and friction while the constantly decreasing pitch of the screw compresses it to pressurize it. For gas assist molding, pressure is lower than conventional injection molding as there is less material to pack into the mold due to hollow sections. Also, since the pressure comes from gas rather than a thick, viscous liquid, there are lower viscosity-based frictional losses inside the pressurized media itself.
If you want to produce high-quality machined parts with a sleek appearance, it’s essential to consider some critical factors related to CNC machining.
At first, the mold clamps shut, and raw resin is fed into the hopper of the injection molding equipment. Just as in a regular injection molding process, the machine melts and pressurizes the resin in its screw-feed section.
External gas assisted injection molding is fundamentally different from the internal process. The gas does not penetrate the material to create hollow sections. Rather, it enters into the mold through microchannels from one side only. It packs the molten resin against the mold’s walls by applying pressure from the backside/non-aesthetic side of the part.
If you’re in need of high-quality prototype injection molding services, consider reaching out to FOWMould. With years of experience in the industry, we offer reliable and efficient prototype injection moulding services that can help bring your product ideas to life.
This process is well-suited to manufacture hollow, lightweight geometries. Additionally, the gas exerts constant pressure on the resin, which helps to minimize shrinkage and distortion/warpage. These factors are usually the main reason for the deteriorating dimensional accuracy of thin walls. Thus, thin-walled parts are another special application of this process.
In the realm of product development, prototype injection moulding serves as a critical tool for testing and validating product designs. It provides a cost-efficient way to identify potential design flaws or issues early in the development process, thereby saving time, resources, and reducing the risk of costly errors in the later stages of production.Prototype injection moulding allows for the creation of a physical model that can be used for various types of testing, including functional, durability, and user experience tests. By testing a physical prototype, companies can gain valuable insights into how the final product will perform and interact in its intended environment. This process also allows for any necessary design modifications to be made before the product goes into mass production, ensuring a higher quality final product.
The manufacturing sector is one of the most innovative in today’s fast-paced world, setting new standards with each stride. Gas assisted injection molding is one such novel plastic manufacturing technique that offers great product quality.
Moreover, parts with large surfaces and curved profiles are tackled quite efficiently. The gas channels are in line with the entire surface, allowing the gas to apply pressure all over the wide surface area. As a result, manufacturing large surfaces is not a considerable issue.
Towards the end of the primary gas penetration phase, the resin starts to cool down and contract. Due to the gap created by this thermal contraction, the gas pressure slightly decreases. This can cause part deformations and induce geometric errors, which are never desirable.
Selective Laser Sintering (SLS): SLS is a type of 3D printing technology that uses a laser to sinter powdered material, typically nylon or polyamide, forming a solid structure. This method is beneficial for creating complex and detailed prototypes that require high durability. SLS does not require any support structures, which makes it ideal for designs with intricate geometries.Stereolithography (SLA): SLA is another form of 3D printing that uses a laser to cure a photosensitive resin layer by layer. SLA is known for its high resolution and accuracy, making it suitable for prototypes that require fine details and tooling. However, SLA prototypes may not be as durable as those created with other methods.Fused Deposition Modeling (FDM): FDM is a common 3D printing method that uses a continuous filament of thermoplastic material. The material is fed through a heated nozzle, which melts it and deposits it layer by layer to build the prototype. FDM is a cost-effective method that can use a wide range of materials, but it may not offer the same level of detail as SLS or SLA.CNC Machining: While not a form of 3D printing, traditional CNC machining is another method used for prototyping. It involves the use of computer-controlled machines to remove material from a solid block to create the desired shape. CNC machining can work with a wide range of materials and is known for its high precision, which can help reduce tooling costs.Rapid Injection Moulding: This is a method that uses aluminum molds, allowing for faster and more cost-effective production of prototypes compared to traditional injection molding. It’s ideal for low-volume production runs.Each of these methods has its own strengths and is best suited to different types of projects, depending on factors such as the complexity of the design, the required durability of the prototype, the materials being used, and the project’s budget and timeline.
A major advantage of this manufacturing technique is that it can handle a wide range of plastic materials. We will discuss below the main plastic materials compatible with this process.
Plastic manufacturing is a versatile field that is continually developing. When it comes to complex geometries and top-of-the-class manufacturing capabilities, gas-assisted injection molding is one of the number one options.
This molten resin then enters the mold cavity. However, the resin injection mechanism does not fill up the mold since the product has hollow sections. The amount of injected resin material depends upon the volume of the part. It typically depends on geometrical factors like wall thickness, ribbed features, holes, etc. Usually, around ~70%-80% of the mold fills up with plastic material.
Gas assisted molded parts to have various applications. Generally, it is for injection molding hollow parts with ribbed/boss features and smooth surface finish requirements.
Gas assisted injection molding is a plastic molding process that combines principles of conventional injection molding with the application of pressurized inert gas. It uses mold cavities in the form of the product’s shape. The mold is partially filled with ~70%-80% molten plastic raw material. Injecting Nitrogen gas fills the remaining volume to pack the plastic material against the mold’s walls.
The gas assisted injection molding process has two main types, external and internal. It also follows a specific workflow with three steps. In the following sections, we distinguish between the two types and explain the step-by-step procedure.
The gas assist injection molding process takes place in three stages (refer to the injection molding diagram below). Each stage constitutes an important step of the process and requires design sense and practical skill from the manufacturing team.
Cycle times are also significantly lower for internal gas assisted molding. Due to the geometries having hollow portions and thin cross-sections, they cool down quickly in comparison to solid parts.
To facilitate our customers, we have developed an efficient online quotation platform that provides rapid quotes based on the design files you upload. Augmenting these quotes is a detailed design feasibility analysis and DFM feedback, which is just one example of the personalized attention you will get here at RapidDirect. Contact us to get in touch with our team for your custom plastic manufacturing needs.
The extremely high level of precision needed within the aerospace industry makes CNC machining a suitable manufacturing process for the sector.
In addition to good surface quality, this technique also allows for thicker sections due to better packing and shrinkage-countering ability. Especially, for ribbed/boss features the rib/wall ratio can be up to 1, which is much better than some other methods. This lends strength and stability to the molded part.
Our state-of-the-art equipment and years of experience guarantee that you will get high-quality plastic parts that will help you beat the competition.
Hence, there is a secondary gas penetration phase where more gas flows into the mold to fill up these gaps. This maintains uniform pressure and guarantees a neat fill.
The prototype injection moulding process begins with the creation of a detailed design of the product. This design is then used to create a mould, which is typically made from metals like steel or aluminum. The chosen material, often a type of plastic, is then heated until it becomes molten. This molten material is injected into the mould under high pressure.Once the material has been injected into the mould, it is allowed to cool and solidify. After the material has fully solidified, the mould is opened, and the prototype is removed. This process can be repeated multiple times, allowing for the production of multiple prototypes in a relatively short period of time.
Gas assist has several pros that make it the go-to technique for many manufacturers. Summarized below are all of its main advantages and disadvantages.
This process is well-known for its fine surface finish quality. Since the gas pressure acts uniformly on the non-aesthetic side, the opposite end tightly packs into the mold extremities, taking its exact shape. The resultant surface is so precise that it also includes fine textures and patterns of the mold. Consequently, external gas assisted molding is preferable if the part has surface patterns and imprints.
After the required amount of resin enters the mold, the process of primary gas penetration begins. A pressurized gas source releases nitrogen into the spruce network, which forms a bubble inside the resin material.
GETTING A QUOTE WITH LK-MOULD IS FREE AND SIMPLE.
FIND MORE OF OUR SERVICES:
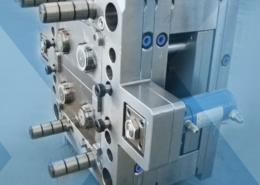
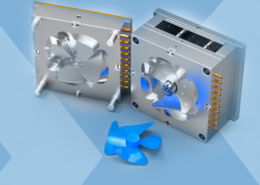
Plastic Molding
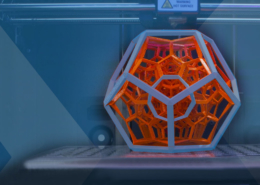
Rapid Prototyping
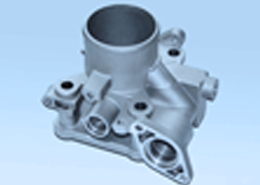
Pressure Die Casting
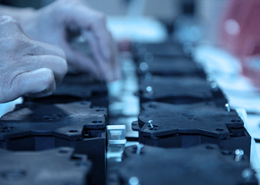
Parts Assembly
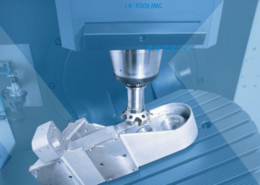