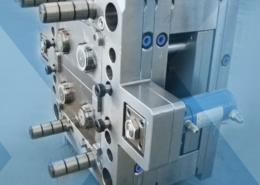
What is EDM in Manufacturing - edm injection molding
Author:gly Date: 2024-10-15
When is it used? In a 3-plate mold, gates can be placed on the sides of the part and the top or bottom of the part. For this reason, 3-plate molding is most useful for more complex geometries where consistent mold flow and cooling might be more challenging to attain in a traditional 2-plate mold.
Because of their difference in process as well as quantity of materials, overmolding usually takes longer to produce. This detail is important to note when considering the timeline and production size.
Though the quantity of the materials may differ, they use roughly the same materials. Materials like ABS and Polypropylene are compatible with both processes. Despite this, choosing the right materials for your product is important to understand. This is because materials should be complementary to each other to ensure quality.
Common applications of overmolding are found in construction, beauty, medical industries, and more. Products like toothbrushes, syringes, wrenches, and makeup brushes are made with this technique. Conversely, 2k molding products are bicycle handle grips, dual-colored phone cases, remote control buttons, gaming controllers, etc.
What is it? A rotating-core mold, or an unscrewing mold, includes a component within the mold that is rotated by a motor or other means into the plastic material as it cools. It is then rotated out of the cooled part once it has solidified.
Through UnitedHealthcare, UMR creates and publishes the Machine-Readable Files on behalf of Crescent Industries, Inc. To link to the Machine-Readable Files, please click on the URL provided: https://transparency-in-coverage.uhc.com/
It is best to consult with experts in the industry to ensure the proper bonding and shrinkage rates of the materials. This makes certain that the product you designed will meet the highest standards of quality.
When is it used? Side-action molds are used for any feature that would prevent the easy ejection of a part. As mentioned, overhangs or undercuts are the most common application of side-action molds.
2k molding machines are designed to efficiently produce two-material products. They can also come in rotary platen, index platen, horizontal and vertical injection, and more.
Choosing between overmolding and 2K molding is important to ensure the quality of your product. This is because they create entirely different items with different purposes. Learning their differences is key to creating unique products that can improve the lives of your target market.
Opting for overmolding means that you want more functionality in your products. This is because they are the best option for products with handles. They are the ideal methods of designing products with grip and texture.
What is it? These molds add an extra plate to the traditional 2-plate design (where the mold parting line occurs (usually) down the middle of the part, and material is injected into the cavity via gates located on the sides of the part. In 3-plate injection molding, the mold separates at not one but two locations (since there are not two but three plates), allowing for more flexibility in the mold — and product — designs.
One of the details they need to learn is the differences between overmolding and 2k molding. From procedures and purposes to materials and machines, read on to learn which method is ideal for your designs.
When is it used? This type of mold is used to create internal threads in parts. It would otherwise be difficult or impossible to eject a part with a threaded feature since threading is a series of small overhangs in the part (which cannot be efficiently achieved with a standard mold).
What are the benefits? In addition to more complex geometries, 3-plate molds will typically result in higher quality due to more consistent material flow. These molds can also be used to enable separate ejection of the part and the runners — since the runners can be contained entirely in one of the plates — which can accelerate production cycles.
The plastic injection industry is the medium used to produce innovative products. Understanding their techniques is pivotal, as it allows companies relying on them to stay competitive in the market.
What are the benefits? Rotating-core molds facilitate fast, efficient production of threaded parts, a feature that is otherwise difficult, costly, and time-consuming to create (whether through machining or other means).
The process sequence of overmolding and 2k molding differs due to the number of materials they use. The method of overmolding involves a first layer with a substrate material, supporting the primary layer. The most common materials for this initial layer are PC/ABS, Nylon, and PBT. They are more rigid or have a higher melting point so that they can easily accept the other materials.
These two types of molding procedures differ in the number of materials used. 2K molding generally only uses exactly two materials for one part. On the other hand, one of the benefits of overmolding is it can mold two or more materials for a single part.
Beyond these basic types of molds, however, more advanced injection molding elements and tactics can be used to create features such as overhangs, internal threads, and more complex shapes. These include 3-plate injection molding, side-action injection molding, and unscrewing injection molds. We will now explore each mold type, including its use and its benefits.
Basic injection mold design is a simple principle: create a mold with cavities representing a “negative” image of the product, with a parting line through the middle so that the mold can open and eject the finished parts. While incredibly versatile, basic injection molding also has some limitations and “ground rules” as far as the geometries that can be achieved.
At Crescent Industries, we offer a wide range of injection mold tooling capabilities, including side-action molds, unscrewing molds, and 3-plate molds. We are ready to share our experience with you to design and build the right injection mold for your product. Visit our website for more information.
One of the key differences between overmolding and 2k molding is their purposes. 2k molding products are usually chosen for their aesthetic or appearance purposes. It can combine two colors in one product in the production process.
2k molding, however, does not need a substrate material. It is also the ideal method to combine hard and soft plastics. This technique is programmed to perform two injections in one cycle. The first injection of material is made into the mold and then it is rotated for the second injection.
Do you have a product in mind? Choose Richfields Corporation to make your idea a reality. We offer various plastic injection services like precision injection molding and mold making. With over two decades of experience and insight, we can help guide you to create high-performing products. Make your design with experts in the industry who understand quality products and services. Contact us and inquire about the quota today!
What is it? In a traditional mold, the mold opens in a single direction, meaning that features such as overhangs and lips cannot be designed into the product since it would then be impossible to eject the part. A side-action mold solves this problem, by adding a tooling feature that moves at a perpendicular angle to the axis when the mold opens and closes. The side action then retracts as the mold opens, allowing for clean ejection.
When considering partnering with reliable plastic injection producers, it is pivotal to know the equipment they use. This will ensure they have the right resources to effectively produce your design. It also shows their commitment to quality when they invest in the right and advanced technology in their production.
What are the benefits? Side-action injection molds allow for geometries that would otherwise be impossible to create in a standard injection mold. Using actions is an inefficient step that is unsustainable at high volumes due to the additional time required. Thus, side-action molds enable the speed and cost benefits of high-volume injection molding for parts that would otherwise need to be created through other processes.
Both methods essentially use plastic injection machines, but they consequently use two different types. Overmolding machines can come in four types. They are vertical, horizontal, rotary table, and multi-station rotary overmolding machines. They have different purposes that allow manufacturers to create vertical, horizontal, multi-component, and complex products for you.
GETTING A QUOTE WITH LK-MOULD IS FREE AND SIMPLE.
FIND MORE OF OUR SERVICES:
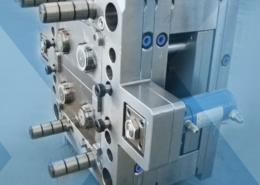
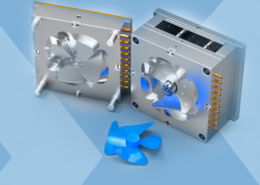
Plastic Molding
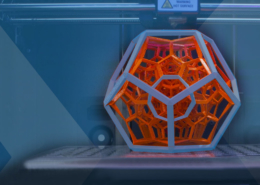
Rapid Prototyping
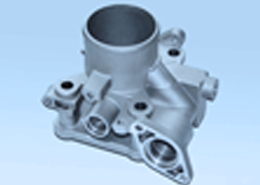
Pressure Die Casting
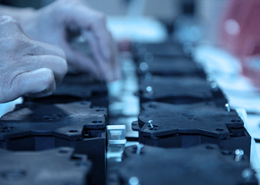
Parts Assembly
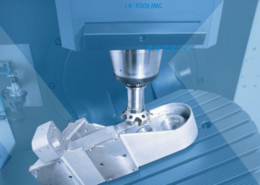