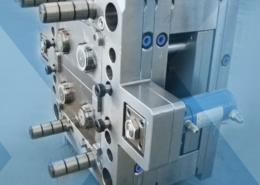
What is ejector stroke of the injection molding machine - ejector rod injection
Author:gly Date: 2024-10-15
Thin-wall injection molding technology is also known as thin-wall plastic injection molding technology. There are three types of definitions:
2K injection molding finds widespread applications across various industries, including automotive, electronics, medical devices, and consumer goods. Some common applications include:
Filling and cooling processes of conventional injection molding are intertwined. When polymer melt flows, front of melt encounters a core surface or cavity wall with a relatively low temperature, and a condensation layer is formed on the surface. Melt continues to flow forward in condensate layer. As thickness of condensate layer increases, actual cavity flow channel becomes narrower. Thickness of condensate layer has a significant effect on polymer flow. Because thickness of plastic part is thicker in conventional injection molding, influence of condensation layer on injection molding is not great at this time. However, in thin-wall injection molding, when ratio of thickness of condensing layer to thickness of plastic part gradually increases as thickness of plastic part becomes thinner, this effect is great. Especially when sizes of the two can be compared with each other.
You can change inlet, add cold material wells, open vent grooves, or bite male mold surface, or increase material temperature, mold temperature, etc.
Thin-walled injection molding is defined as a thin-walled injection molding when wall thickness of molded plastic part is less than 1 mm (or 1.5 mm), or t/d (thickness t of plastic part, diameter d of plastic part, for disc-shaped plastic parts) is less than 0.05 .
Slender pieces, large-area thin-walled pieces, or large finished products with asymmetric structures are caused by uneven cooling stress or uneven ejection forces during molding.
2K injection molding stands out as a popular choice for its ability to combine two or more different materials in the same mold before injection, offering unique advantages and applications. Here, we delve into the world of 2K injection molding, exploring its uses and benefits and showcasing its successful deployment in various industries.
At present, commonly used thin-wall injection molding materials are: polycarbonate (PC), acrylic-butadiene-styrene (ABS), PC / ABS blends, and PA6. As wall thickness decreases, plastics with better physical properties are needed to maintain product strength.
It can be processed by modifying core, ejector pin, and sandblasting of mother mold surface. It can reduce brightness of mold surface, reduce injection speed, and reduce injection pressure.
Occurs at confluence of two streams, such as confluence of two inlets, confluence of bypass bypassing core, is due to decline in material temperature and poor exhaust.
2K injection molding, also known as dual injection molding and two shot injection molding, is a manufacturing process in which two materials are simultaneously injected into the mold cavity. This technique allows for the production of complex plastic parts with varying colors, materials, or properties in a single operation. Typically, the first material is a rigid substance like polypropylene, while the second material is often an elastomeric material such as TPE or TPV. This combination of materials allows for more intricate designs and improved functionality compared to traditional single-material injection molding.
It often occurs in uneven wall thickness or flesh thickness of molded product, which is caused by difference in cooling or curing shrinkage of hot-melt plastic. Such as back of ribs, edges with side walls, back of BOSS column.
It often occurs on the back of a reduced bosom column or ribs, or stress marks are reduced due to high core and thimble design.
Analysis of common defects: Although there are many advantages to thin walled plastic parts, formability of plastic parts is reduced, so that these thin walled plastic parts cannot be molded by conventional injection molding methods. When forming thin walled plastic parts, following common problems exist:
Welding line is boundary formed when two or more melt flow fronts within a cavity are fused. Stress concentration is easy to occur at welding line, which weakens mechanical strength of plastic part, which is particularly detrimental to mechanical properties of plastic part, especially thin-walled plastic part. Plastic part is very easy to crack at welding line after external force.
While both overmolding and 2K injection molding allow the combination of multiple materials into a single product, they are different. The key difference between them lies in the process and timing of combining the materials.
It can be seen that critical value defined by thin-wall injection molding will also change, and it should be a relative concept.
Injection molding method where thickness of molded plastic part is less than 1 mm, and projected area of plastic part is above 50 c㎡;
Compared to overmolding, two shot injection molding injects both plastic materials simultaneously, so it is better at handling more materials and larger production volumes and offers greater utility and efficiency.
Increase R angle at the corner, increase demolding angle, increase ejector pin or increase its cross-sectional area, polish mold surface, polish ejector pin or oblique pin, reduce shooting rate, reduce injection pressure, reduce holding pressure and time.
Transparent finished PC material is easy to appear. Because gas is not exhausted during injection process, improper mold design or improper molding conditions can have an impact.
Requirements for raw materials: large flow length, high impact strength, high thermal deformation temperature, high thermal stability, low directivity, and good dimensional stability; also consider low temperature impact rigidity, flame retardancy, mechanical assembly and appearance quality of plastic materials.
2K injection molding is a highly versatile and efficient manufacturing process that offers numerous benefits for producing complex, multi-material parts with high precision and tight tolerances. By understanding the process, requirements, and design guidelines, manufacturers can leverage the advantages of two shot injection molding to create high-quality products for various industries, including medical, automotive, consumer electronics, and more. When choosing a 2K injection molding machine service provider, it's essential to consider factors such as certification, experience, and service offerings to ensure a successful and cost-effective manufacturing process. Huarong Group is an experienced injection molding machine manufacturer; if there is a need for 2K injection machines or automation, please feel free to contact Huarong.
Selecting the appropriate materials is crucial for achieving optimal results in 2K injection molding. While this process offers significant design freedom, it's essential to consider fundamental factors to ensure compatibility and performance.
Increase exhaust, change gate (inlet gate increases), PC flow path must be polished, strict drying conditions, increase injection pressure, reduce injection speed, etc.
Correct ejector pin, set tensioning pin, etc. If necessary, adjust deformation of male mold with bite adjustment, adjust temperature of male and female mold to reduce holding pressure, etc. Adjustment of deformation of small parts mainly depends on pressure and time, and adjustment of large pieces of deformation generally depends on mold temperature.
3K injection molding, or three-shot molding, is an advanced manufacturing process that involves injecting three different materials or colors into a single mold to create a complex, multi-material product. This technique allows for the combination of materials with varying properties, such as hardness, flexibility, and color, in a single production cycle.
During design, you can reduce or change position of welding line by reducing number of gates or changing position of gates to meet design requirements of plastic parts.
It is easy to occur at the corner of thin wall of molded product or at the root of thin wall RIB. It is caused by poor force during demolding, improper setting of ejector pin or insufficient draft angle.
Mold correction, mold re-clamping, increase clamping force, lower material temperature, reduce injection pressure, reduce holding time, reduce holding pressure.
When flow length is 300mm and wall thickness of plastic part is 3.0 mm, L / T is 100 at this time, which is easily achieved by conventional injection molding technology; but when wall thickness of plastic part drops below 1.0mm, this once-to-be-achieved flow-length-thickness ratio (100) becomes very difficult to achieve.
Increase draft angle, polish mold surface, increase or change pull pin when sticking female mold surface. Pay attention to horn diameter when feeding horns, add bite to male mold, reduce injection pressure, reduce holding pressure and time.
When thickness of plastic part is reduced, influence of condensate layer on flow will increase exponentially, which also explains influence of condensate layer in thin-wall injection molding. If only considering injection molding, it is necessary for injection molding machine to have a high injection rate, so that rate at which plastic melt fills cavity exceeds growth rate of condensation layer (or growth rate of condensation layer is slowed), so that filling action can be completed before flow section is closed, thin-walled plastic parts are injection molded.
The 2K molding process is ideal for parts with complex geometries, as it allows for precise placement of the second material. Additionally, it reduces production times and costs by eliminating the need for separate molding and assembly operations.
1K injection molding, or single-shot molding, is a conventional molding process that involves injecting a single material into a mold cavity to produce a plastic product. Unlike multi-shot molding processes such as 2K and 3K injection molding, 1K injection molding uses a single injection unit to inject the material into the mold.
Occurs at joints of male and female modules, sliders, oblique pins, etc., which appear as uneven levels of joint surface, etc., due to improper mold clamping or problems with mold itself.
Warping deformation defects of plastic parts can be improved by balancing cooling system, adjusting cooling time, holding pressure and holding time.
Appears as poor demolding, mold damage, or pull. Mainly because draft angle is not enough or mold surface is rough, molding conditions also have an influence.
It occurs at the gate, because mold temperature is not high, injection speed and pressure are too high, gate is not set properly, and plastic encounters spoiler structure during feeding.
Reduce thickness, but keeping at least 2/3 of thickness, can be improved by thickening runner, increasing gate, increasing exhaust, increasing material temperature, increasing injection pressure, and extending holding time.
For PC materials, sometimes mold temperature is too high, mold surface has residual glue and oil stains. It is necessary to clean mold surface in time, lighten processing, and reduce mold temperature.
It often occurs at the junction of male and female molds, due to poor mold clamping, or improper processing of corners of mold surface. Molding temperature is often insufficient due to insufficient clamping force, high material temperature, and high pressure.
You can change gate, lighten runner, increase cold area of runner, increase gate, and add bite on the surface (you can also adjust line by adjusting machine or repairing mold). It can solve problems such as mold temperature, reducing injection speed and reducing injection pressure.
In two shot injection molding, specialized equipment plays a pivotal role in ensuring precise and efficient production processes. The primary components of 2K injection molding equipment include:
Depending on the specific requirements of the two shot injection molding process, other supporting equipment such as robots for part handling, material mixers for blending the two materials, and quality control systems may also be necessary.
Overmolding is often used to add a layer of TPE (thermoplastic elastomer) or rubber over a substrate, which can be a plastic, metal, or brass part and then overmolding it with a second material. This process creates a strong bond between the materials, enhancing the product's functionality and aesthetics.
Ratio of flow length to thickness L / T, that is, ratio between flow length L from melt entering mold to the furthest point of cavity where melt must be filled and corresponding average wall thickness T is 100 or 150, which is being called thin-wall injection molding;
The two shot injection molding process is highly efficient, allowing for the creation of complex, multi-material parts with high precision and tight tolerances. Here's a simplified breakdown of how it works:
According to surveys, domestic thin-wall injection molding has been widely used in food containers, medical boxes, cosmetics, stationery and even multimedia packaging. For example: disposable packing boxes, cosmetics bottles and other daily necessities.
Short shot refers to incomplete quality defect of plastic part due to incomplete filling of mold cavity, that is, melt has set before filling is completed.
Generally, changing holding time and injection pressure (second stage) has the greatest effect on size. For example, increasing injection pressure, pressure-retaining and shrinking effect can significantly increase size and lower mold temperature. Increasing inlet can improve adjustment effect.
Small parts and corners of finished product cannot be completely formed. Due to insufficient mold processing or poor venting, design defects (insufficient thickness) are caused due to insufficient injection dose or pressure.
The 2K injection molding machine is the cornerstone of this process. It is programmed to execute two injections in a single cycle. During the first cycle, a nozzle injects plastic into a mold, which is then rotated to allow the injection of a different type of plastic from a second nozzle. This sophisticated machine enables the creation of highly effective end products from disparate polymers.
Warpage deformation is a plastic defect caused by uneven internal stress. Cause of warpage deformation is uneven shrinkage, uneven orientation, and uneven cooling.
Molds at missing parts can be modified, taking or improving exhaust measures, thickening material, improving gate (enlarge gate, increase gate), increasing injection dose, increasing injection pressure and other measures to improve.
The 2K injection mold is another essential component, designed to accommodate the dual-material injection process. This mold features two cavities, each corresponding to one of the materials being used. The design of the mold is crucial in ensuring proper material flow and part formation.
GETTING A QUOTE WITH LK-MOULD IS FREE AND SIMPLE.
FIND MORE OF OUR SERVICES:
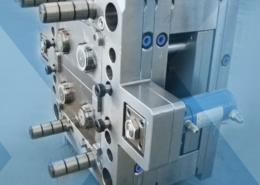
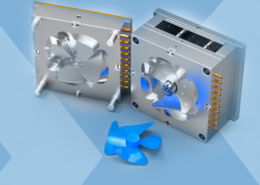
Plastic Molding
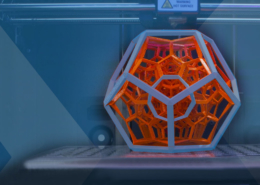
Rapid Prototyping
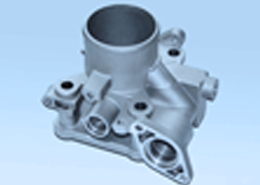
Pressure Die Casting
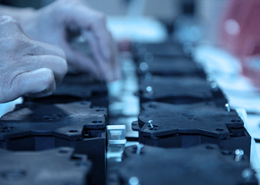
Parts Assembly
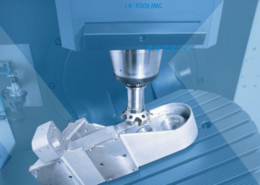