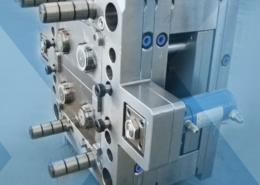
What is Injection Moulding? – Definition, Types and Materials - injection moldin
Author:gly Date: 2024-10-15
Plastic injection molding, or commonly referred to as injection molding, is a manufacturing process used in the mass fabrication of plastic parts. It involves an injection of molten plastic material into the mold where it cools and...
PlasTech Molding Solutions operates from a single location at 50 mellen street, hopedale, massachusetts 01747, united states.
Rotationally molded plastics are crafted using rotomolders, which typically consist of four main components: an oven, molds, mold spindles, and a cooling chamber.
Cross-linked polyethylene boasts excellent impact strength, resistance to environmental stress cracking and abrasion, making it particularly suitable for applications exposed to extremely low temperatures.
As a full-service rotational molding company, Roto Dynamics is your source for high quality, custom rotomolded products. Since our inception, we have continued to earn success by closely working with our customers, developing innovative and tailored solutions. We are with you every step of the way, from design and development to production and assembly. For a complete view of our capabilities and ...
Rotational molding, commonly referred to as "rotomolding", is a plastic casting technique used to produce large hollow, seamless, and double-walled parts. It is a three-stage process that involves a mold on a rotating frame, a heating chamber, and a cooling chamber. Molds for the rotomolding process are specially designed....
The headquarters of PlasTech Molding Solutions are located in 50 mellen street, hopedale, massachusetts 01747, united states.
PlasTech Molding Solutions, formerly R.E.C. Manufacturing Corporation, specializes in custom injection molding with over 70 years of experience. Their expert staff, with a combined experience of over 100 years, excels in developing high-performance products, including thin-wall complex geometry applications. The company operates a modern 40,000 square foot facility with multiple clean rooms and a range of injection molding machines. PlasTech Molding Solutions is ISO 9001 certified, ITAR registered, and prioritizes customer service, engineering, production, and quality assurance. They offer a variety of services to meet the needs of both existing businesses and new product development.
We are a custom manufacturer of rotationally molded products. Our state of the art technology creates precise, cost effective and dependable products. Whether your order is large or small, we want to be sure you are satisfied.
The cornerstone of producing top-tier rotomolded plastic parts lies in selecting a reputable manufacturer. To aid you in this quest, we have curated a list of leading companies in the plastic molding industry. You can explore their profiles conveniently located throughout this page.
Rotomolding is a versatile technique for manufacturing a wide array of products and components. In the realm of sports and recreation, this process is used to create items such as canoes, kayaks, playground slides, footballs, and sports helmets. Beyond these, rotomolding also produces large plastic vessels and storage tanks, safety cones, sizable trash containers, various hollow bins, outdoor furniture, and beverage containers.
Plastic coating is the application of liquid polymers or plastic on the surface of a workpiece by dipping or immersion. The result is a thick plastic finish for protective and decorative purposes. This gives the material additional resistance against...
Molding is a manufacturing process that uses a mold - the latter being a solid container used to give shape to a piece of material. It is a forming process. The form is transferred from the mold to the material by...
Rotationally molded plastics are thermoplastic products fabricated through the rotational molding process, or rotomolding. A thermoplastic is a plastic material that will soften when repeatedly heated and cooled. The rotomolding process is simple and inexpensive, involving only a revolving mold and high heat. Rotationally molded plastics are hollow, with the high tensile strength and uniform wall thickness due to single piece construction. Read More…
Shuttle-type rotomolders shuttle molds between heating and cooling chambers, enabling biaxial mold rotation. These machines are highly customizable and cost-effective, ideal for manufacturing large-sized products.
Customers appreciate rotomoulding for the superior quality of its rotomolded products and the affordability of its tooling costs. Rotomolded plastic parts are known for their high tensile strength, consistent wall thickness, and seamless single-piece construction.
Western Industries Plastic Products, LLC, specializes in large-part plastic blow molding. We provide expertise and services in product design, process improvement, and product assemblies. We offer our customers comprehensive services and turnkey opportunities to achieve their specific project goals. We can assist with: R&D, product design, product improvement, and secondary-fixture design. For...
Clamshell machines use a mechanical arm to rotate molds, allowing manufacturers to program rotation along various axes. These rotomolders conduct heating and cooling within a single chamber, making them cost-effective and space-efficient compared to alternative designs.
We recommend studying the profiles of rotational molding companies while holding a list of your application and product specifications for comparison. Seek companies that not only fit your budget but also offer necessary services. An inexpensive product may not suffice if it lacks industry certifications. Identify three or four contract manufacturers that seem best suited for your needs. Then, individually contact each molding company to discuss your application. Ensure they can meet all requirements, including timeline, budget, delivery preferences, custom rotational molding, and safety standards. After these discussions, choose the company that promises to deliver the best product and begin collaboration. Best of luck!
PlasTech Molding Solutions uses a variety of equipment, including Horizontal injection molding machines (29 machines ranging from 22 tons to 310 tons).
Polyurethane molding is the process of fabricating or manufacturing plastic parts by introducing a urethane polymer system into a tool or mold and allowing it to cure. Like any other type of plastic, the excellent processability...
Rotomolding, while slower than other thermoplastic molding techniques, is generally used for shorter production runs. Despite its slower pace, rotational molding provides unique benefits not found in other processes. Firstly, it allows for simultaneous production of various products of similar sizes. Secondly, this method economizes on energy, tooling, and equipment expenses by eliminating the requirement for high-pressure molds. Thirdly, it facilitates quick transitions between different colored plastics without requiring extensive cleaning of production lines. Furthermore, seamless rotationally molded plastics exhibit enhanced durability against higher pressures without risk of fracturing.
In the 1920s, R.J. Powell pioneered the use of rotational molding to shape plaster of Paris, a soft blend of lime, sand or cement, and water. This material, named after the gypsum deposits found in Montmartre, Paris, marked the early days of the technique. By the 1940s and early 1950s, plastic rotational molding experienced another transformation with the advent of plastic molding. This method became popular for producing hollow plastic toys, particularly doll heads. The molding machines of this period were assembled from rear axles and other automobile parts, powered by electric motors, and heated by gas burners. Manufacturers used molds made of copper and nickel, which were cooled in water baths, predominantly working with PVC plastic.
Note: Manufacturers have the option to procure raw materials from external sources or to handle poly processing on-site.
We provide outstanding custom plastic rotational molding. Our teams offer short lead times and we will assist you from concept to production. All of our materials and designs are FDA approved and we can handle the most complex projects. We are your one stop shop for all of your rotational molding needs. Give us a call today to learn more information!
Polyvinyl chloride, often known as PVC or vinyl, boasts exceptional chemical resistance, high transparency, long-term stability, reliable weather resistance, superior flow properties, and consistent electrical performance. It is versatile, available in both flexible and rigid forms.
Vertical machines, alternatively referred to as rotational machines, feature numerous compact cooling and heating chambers. They are loaded and unloaded from the front, and come in a diverse range of sizes, offering both energy efficiency and space savings.
Blow molding, akin to rotomolding, crafts hollow plastic components. In this method, melted plastic is shaped into a tube-like form with a hole at one end, known as a parison. Manufacturers then clamp the parison into a mold and introduce air through the hole. As the air enters, the parison expands until it conforms to the inner walls of the mold. Once cooled and solidified, the mold is opened, and the part is ejected. Primarily, blow molding is employed for manufacturing plastic bottles.
Engineers and manufacturers today employ advanced control and monitoring systems for cooling, initially pioneered in the 1980s at Queen’s University Belfast. They persistently innovate, exploring new materials and reimagining the rotomolding process, continually pushing the limits of what can be achieved.
Our warehouses and equipment are designed to protect the quality and condition of the rotationally molded plastic products we sell and process. Our facilities feature state of the art equipment, and are run by a team of dedicated staff members who will help you find what you need. Contact us today!
Mold Spindles- The mold spindles are affixed to a rotating axis, facilitating consistent coating of parts during production.
High-density polyethylene also excels in cold-weather performance and adaptation. Moreover, this high-flow, high molecular weight thermoplastic enhances product quality with superior interior gloss.
Rotationally Molded Plastic | Home | Request for Quote | Photo Gallery | Privacy Policy/Terms of use | List of Companies | Sitemap
Blow molding is a type of plastic forming process for creating hollow plastic products made from thermoplastic materials. The process involves heating and inflating a plastic tube known as a parison or preform. The parison is placed between two dies that contain the desired shape of the product...
Michiana Rotational Molding provides unparalleled rotational molding services that ensure efficient design, innovation, and functionality. Based in southwest Michigan, the company offers engineering, prototyping, finishing, design consulting, and quality control services. It has experience creating solutions for clients in the marine, home and garden, RV, and material handling industries and more ...
Polyethylene, also known as polythene, stands as the most prevalent type of plastic. Despite its moderate strength, it boasts high impact resistance, hardness, and rigidity. Additionally, it is ductile and resistant to friction. Common products made from rotational molding of polyethylene include bottles, pipes, and bins.
Rock and roll rotomolders are specialized for creating elongated products. These machines are equipped with compact heating chambers and excel in high-volume production, ensuring efficiency. Depending on the specific needs, they may be outfitted with either a single or dual arm configuration. The primary arm rotates the mold 360 degrees around one axis and tilts it 45 degrees along another axis. Machines featuring two arms are referred to as shuttle type machines.
Rotationally molded linear low-density polyethylene parts offer exceptional fit and finish, along with robust impact resistance, tensile strength, and insulation capabilities.
© Rotationally Molded Plastic will keep your information private and secure. We will not share your email address with any third parties.
Despite the brilliance of Peters’ invention, it wasn’t widely revisited until the early 20th century. In 1905, American Fred A. Voelke discovered that rotational molding could be used to create hollow wax objects. Approximately five years later, G.W. Perks and G.S. Baker applied this technique in an unexpected way—producing hollow chocolate eggs.
Injection molding is a versatile process employed for shaping both plastic and metal. It utilizes a ram, hopper, heated barrel, nozzle, and mold. Here’s how it works: molten material is pushed by the ram through the heated barrel and nozzle into a cool mold. Once inside, the material conforms to the mold’s shape under pressure and rapidly solidifies. This method is notably quicker than rotational molding, particularly effective for producing intricate details like sharp threads.
In 1976, delegates from multiple nations convened in Chicago, founding the Association of Rotational Molders (ARM), a global trade organization. Since then, ARM has grown to encompass members from 58 countries, fostering collaborative rotomolding efforts worldwide. Following ARM’s inception, engineers introduced innovative raw materials to its members, such as polycarbonate and nylon. These materials revolutionized industrial mold, water tank, and fuel tank production, enabling manufacturers to achieve significant advancements.
Provide your project details, and we'll connect you to 5-20 qualified rotationally molded plastic companies in your region. 100% free.
In 1855, a British inventor named R. Peters pioneered the first rotational molding process. His goal was to create artillery shells and other hollow vessels with uniform density and wall thickness. To achieve this, he utilized a technique involving biaxial rotation and heat.
Fiberglass molding is a method for forming complex and intricate parts using fiberglass resin. Though there are several reasons for producing parts and components from fiberglass, the most pressing reasons are the...
Rubber molding is a process of transforming uncured rubber or an elastomer into a usable product by transferring, compressing, or injecting raw rubber material into a metal mold cavity...
When crafting a rotationally molded plastic part, manufacturers carefully weigh various application specifications. These include essential product traits such as strength, thermal durability, and flexibility. Additionally, considerations extend to desired product color, shape, size, and compliance with industry standards. Determined by these specifics, decisions are made on material selection—encompassing diverse plastic resins and additives—as well as the type of rotomolder and process employed.
Rotomolded plastics offer several advantages. They can be readily manufactured to comply with FDA standards, making them suitable for pharmaceutical, food, and beverage industries. Additionally, designing molds to incorporate logos, graphics, or labels into rotomolded plastic products is straightforward. These parts are lightweight and highly versatile, allowing for customization in density, color, finish, and texture.
Carousel rotomolders represent the predominant variety of bi-axial rotomolding machines. These machines typically feature either four or six stations. Their synchronized arms enable simultaneous operations across multiple tasks. For instance, while one arm remains at the heating station, another may move to the cooling station, with yet another engaged in loading or unloading processes.
At D&M Plastics Inc, our expertise lies in delivering exceptional rotational molding solutions, elevating the standards of custom plastic manufacturing. With a legacy rooted in innovation and a relentless pursuit of excellence, we stand as leaders in crafting superior-quality plastic products through the rotational molding process.
Rubber injection molding is when uncured rubber is transformed into a usable product by injecting raw rubber material into a mold cavity made of metal. The applied pressure produces a chemical reaction like...
There are five main types of rotational molding machines: carousel types, clamshell types, rock and roll types, vertical types and shuttle types.
For custom rotomolded parts, manufacturers have the flexibility to create bespoke molds. This customization extends to textures, finishes, colors, and labeling options, encompassing logos, graphics, or other distinctive markings.
This manufacturing process is favored across various industries, including road construction, agriculture, plumbing, sporting goods, packaging, material handling, automotive, toy manufacturing, wastewater management, pharmaceuticals, food and beverage processing, fuel and oil, chemical handling, and marine manufacturing.
PlasTech Molding Solutions, formerly R.E.C. Manufacturing Corporation, specializes in custom injection molding with over 70 years of experience. Their expert staff, with a combined experience of over 100 years, excels in developing high-performance products, including thin-wall complex geometry applications. The company operates a modern 40,000 square foot facility with multiple clean rooms and a range of injection molding machines. PlasTech Molding Solutions is ISO 9001 certified, ITAR registered, and prioritizes customer service, engineering, production, and quality assurance. They offer a variety of services to meet the needs of both existing businesses and new product development.
Many plastics are suitable for rotational molding, spanning a wide range such as polyethylene (PE), cross-linked polyethylene, high-density polyethylene (HDPE), linear low-density polyethylene (LLDPE), and polyvinyl chloride (PVC). Among these, polyethylene stands out for its lightweight nature and low modulus of elasticity.
In the 1920s, R.J. Powell pioneered the use of rotational molding to shape plaster of Paris, a soft blend of lime, sand or cement, and water. This material, named after the gypsum deposits found in Montmartre, Paris, marked the early days of the technique. By the 1940s and early 1950s, plastic rotational molding experienced another transformation with the advent of plastic molding. This method became popular for producing hollow plastic toys, particularly doll heads. The molding machines of this period were assembled from rear axles and other automobile parts, powered by electric motors, and heated by gas burners. Manufacturers used molds made of copper and nickel, which were cooled in water baths, predominantly working with PVC plastic.
Extrusion swaps the mold for a die, enabling the machine to craft items with consistent cross-sectional profiles. This process accommodates brittle materials unsuitable for rotational molding, yielding products with superior surface finishes and intricate cross-sectional designs.
GETTING A QUOTE WITH LK-MOULD IS FREE AND SIMPLE.
FIND MORE OF OUR SERVICES:
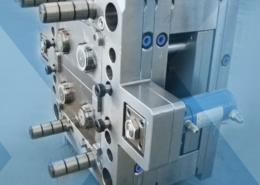
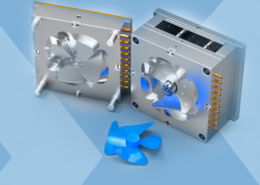
Plastic Molding
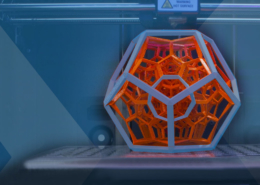
Rapid Prototyping
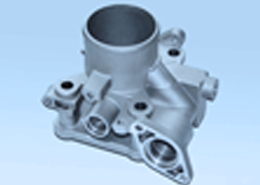
Pressure Die Casting
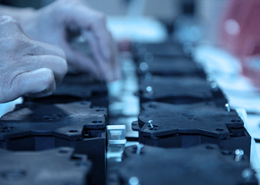
Parts Assembly
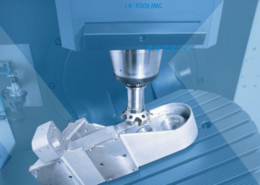