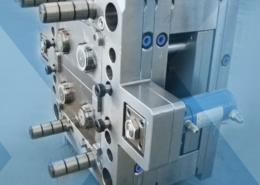
What is IML? In Mold Labeling Process, Benefits, and ... - in mold labeling inje
Author:gly Date: 2024-10-15
The properties of rotationally molded containers or vessels benefit numerous applications within multiple industries, including aerospace, agriculture, automotive, mining, metallurgy, pharmaceuticals, and semiconductor fabrication.
We are thrilled to announce that AIM Processing will be exhibiting at the 2024 Long Beach Manufacturing Trade Show in September! This premier event ...
This seamless interior minimizes weak points where chemicals could potentially penetrate or react with the material. The homogeneous nature of the plastic structure enhances its resistance to various chemicals and corrosive substances.
A mold is mounted to a multi-axis rotational molding machine. Thermoplastic resin is placed inside the mold, and in some circumstances, components such as mounting nuts or brackets are inserted at this time as well.
The mold is rotated inside of an oven. As the mold rotates, the polymer becomes molten and forms an even layer across all internal surfaces.
AIM Processing has acquired Technical Molded Products, solidifying its position as a leading injection molder in the western United States. Key ...
The design and manufacture of custom molded plastic parts can seem simple at first, but there are many details that must be taken into consideration depending on how the part will be used. For example, there are mechanical properties like:
A seamless interior also eliminates cracks or crevices where bacteria or contaminants could accumulate, enabling rotationally molded containers and vessels to serve in high-purity manufacturing operations.
Rotational molding offers manufacturers a cost-effective method to produce hollow, seamless parts using thermoplastic polymers. Polymer resin is placed in a mold, which is then heated and rotated on two axes to evenly distribute the melted plastic resin through the interior of the mold. As it cools, the plastic solidifies into the desired shape, vessel, or container. The rotational molding process yields components with a high strength-to-weight ratio, which also provides chemical resistance and corrosion protection.
We use the rotational molding process to create aerospace parts and high-purity containers. We also have the capability to manufacture a wide range of molded pieces in our ISO Class 7 Clean Room for high-purity applications.
We use a variety of thermoplastic polymers in our rotational molding process, including polyethylene, polypropylene, and PVC. We also offer proprietary resins. Resin selection depends on the specific requirements of each individual project. Factors such as durability, chemical resistance, availability, and cost optimization play important roles to help determine the ideal material.
Rotational molding is a manufacturing method that produces parts fabricated from polymer resins, which can offer excellent chemical and environmental resistance. The resistant properties of selected polymer resins are aided by the seamless interior that results from the rotational molding process.
AIM Processing specializes in small part plastic injection molding. We define "small plastic parts" as roughly the size of your fingernail to the size of your hand. Injection molding is a process in which plastic resin, in pellet form, is heated and sheared until it reaches a viscous state.
Maintaining proper wall thickness is one of the most important aspects of designing custom injection molded parts. Overly thick walls not only waste ...
The mold is removed from the machine and the plastic part is carefully taken out of the mold. The resulting seamless thermoplastic piece can be machined to tight tolerances, painted, or otherwise finished and assembled with other parts.
Overall, rotomolded containers and vessels are valued for their ability to maintain their structural integrity and the durability and impact resistance they can offer, alongside their chemical and environmental resistance. Rotomolding also presents cost advantages compared to other manufacturing methods for an impressive return on investment.
It is then injected under enormous pressure into a steel or aluminum mold, cooled until it hardens, and ejected. With small part injection molding, we are able to manufacture complex, small shapes in a cost-effective, repeatable process.
As a leading small plastic parts manufacturer, we work with engineering grade plastics to create custom molded plastic parts that match the requirements for a part with properties like: chemical resistance, flexural strength, durometer, and yield strength to name a few. There are so many material options, and we can help you make the right choice for your program.
Thin-walled, hollow parts that require tight tolerances can be manufactured using a rotational molding (rotomolding) process. Our consistent manufacturing process gives us the ability to create complex geometries in a single seamless part. We use proprietary resins and cost-effective, affordable tooling.
“We received the charger base and I want you all to know it looks FANTASTIC! Thank you for getting us this one for the BOD meeting.”
Discover AIM Processing's customer small part injection molding services, designed to deliver precise, high-quality components for industries requiring intricate and complex plastic parts.
Then there are factors like the manufacturability of gate locations, draft, and ejector pins. It's enough to make your head spin.
GETTING A QUOTE WITH LK-MOULD IS FREE AND SIMPLE.
FIND MORE OF OUR SERVICES:
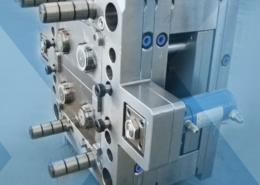
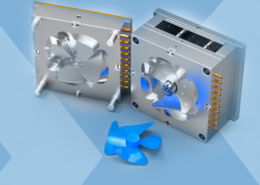
Plastic Molding
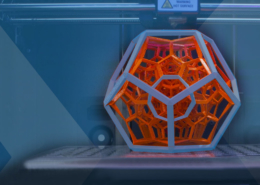
Rapid Prototyping
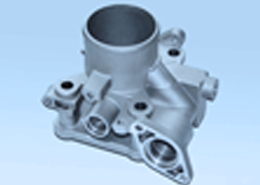
Pressure Die Casting
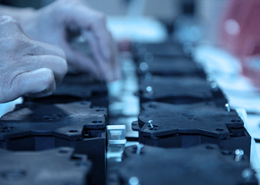
Parts Assembly
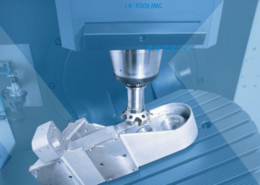