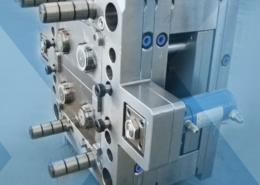
What Is LSR 2-Shot? Your Guide To Multishot LSR Molding - double shot injection
Author:gly Date: 2024-10-15
We excel at creating unique solutions for you by first understanding your product's applications. Let us become your single source for plastic products — contact us to learn more.
ICOMold by Fathom has the expertise to help meet your ABS injection molding needs. We offer fast and dependable service, low prices, quick quotes, and an online project management system. ICOMold by Fathom can handle projects of any size – from small part or prototype runs to extended part runs in the thousands or even millions.
ABS injection molding offers numerous benefits over other plastic materials. ABS plastic is easy to mold and has good machinability. It has high impact and tensile strength, dimensional stability, stiffness, and excellent stability under load. ABS can maintain its characteristics and performance in extreme temperatures but also has a low melting temperature — making it easy to use when injection molding. ABS can be alloyed with other polymers to achieve desired characteristics. ABS can also be colored for custom pieces and is easy to paint and glue, making it a good candidate for secondary processing.
The seamless plastic products we make within our rotational molding facility are numerous and ever growing. From water-tight tanks to mudguards and toolboxes, the possibilities are endless — and we are proud to be a part of that advancement. Whether you designed a new product headed for prototyping, or are searching for a better production solution for an existing one, Advanced Plastics Rotomolding is the first place to start.
Family owned and operated with nearly two decades of rotomolding experience, you can count on our company to meet the requirements of yours. Here are some of the reasons others choose Advanced Plastics Rotomolding, LLC…
ABS plastic is recyclable. Using a combination of virgin ABS plastic mixed with recycled ABS can help customers reduce overall costs. The ABS is shredded and then purified to remove any undesirable metals or plastics during the recycling process. The leftover product is then analyzed and combined with virgin ABS to produce a new product that is ready for injection molding.
ABS injection molding done at a high temperature produces resistance to heat and a smooth, gloss finish. ABS injection molding done at a lower temperature will result in better strength and impact resistance. The final properties and strength of any ABS injection molding product will be influenced by the condition parameters used during the manufacturing process. The experts at ICOMold can help customers select the correct parameters for their next ABS injection molding project.
ABS plastic begins as a pellet. The pellet is then melted into a moldable state and injected into the cavity of a two-part mold. The plastic will solidify almost as soon as the mold has been filled. The part then cools to the shape of the mold. The mold opens once the plastic has fully cooled and the part is ejected. The mold is closed and the process starts over.
ABS plastic should not be used under direct sunlight or near an open flame. Fire-retardant and heat-resistant grades of ABS are available. Some ABS components can emit toxic fumes after heating.
Acrylonitrile butadiene styrene (ABS) is a rigid, lightweight plastic that is both durable and impact resistant. ABS is made up of the three monomers – acrylonitrile, butadiene, and styrene – hence the abbreviation ABS. Each of the monomers plays an important role in the composition of the final plastic. The acrylonitrile gives the final product heat and chemical resistance. The butadiene is used for impact resistance. The styrene provides extra strength and a glossy finish. ABS is used to make appliances, toys, medical supplies, musical instruments, computer parts, and more. One of the most recognizable examples of ABS injection molding is the little plastic LEGO® brick. LEGO® bricks exhibit all the qualities that makes ABS an ideal material for a wide array of projects. LEGO® bricks are tough, scratch resistant, impact resistant, and have a smooth, glossy finish.
ICOMold by Fathom is an expert at ABS injection molding and can provide customers of all sizes with a seamless manufacturing process from prototype to production.
Our custom rotational molding capabilities allow us to create a wide variety of products to meet your exact resin type, size, thickness, and color specifications.
ABS is a thermoplastic polymer widely used for injection molding. ABS is durable, budget -friendly, and is easy to machine. ABS can be used in conjunction with a metal coating since many metals will adhere strongly to the surface of ABS plastic. ABS plastic has good resistance to extreme temperature and humidity. ABS is perfect for projects that demand strength, stiffness, and impact resistance. ABS is an ideal candidate for secondary processing as it can easily be painted or glued. ABS is also very easy to recycle.
Plastics have become a part of everyday life, with more and more product developers opting for the benefits of rotationally molded components. The manufacturing process we specialize in — rotational molding — affords inventors, designers, and product manufacturers enhanced flexibility when compared to other forms of manufacturing.
ICOMold’s fast-turn, low-cost, high-value injection molding enhanced by joining Fathom’s manufacturing platform. Learn More
Jason Dickinson (President)… 320-630-3571 James Dickinson (Vice President)… 320-360-4437 Jim Dickinson (Mold Builder)… 320-232-3559
GETTING A QUOTE WITH LK-MOULD IS FREE AND SIMPLE.
FIND MORE OF OUR SERVICES:
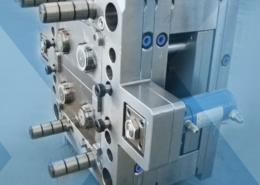
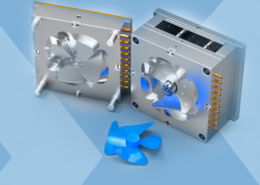
Plastic Molding
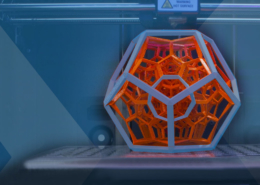
Rapid Prototyping
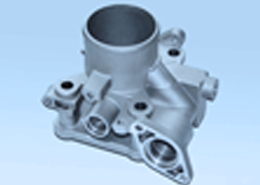
Pressure Die Casting
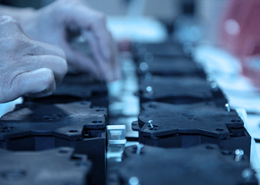
Parts Assembly
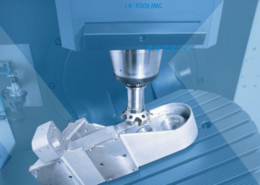