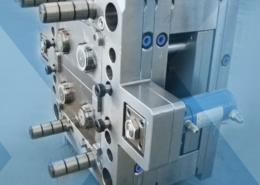
What Is LSR 2-Shot? Your Guide To Multishot LSR Molding - double shot injection
Author:gly Date: 2024-10-15
Known for their viscosity and elasticity, elastomers are polymers generally of a rubbery texture. Elastomers get their names from elasticity; they can be stretched and regained in shape. Synthetic elastomers, often made of petroleum, come into various industrial use, such as manufacturing over-molded parts. Apart from elasticity, elastomers are also known for their resistance.
Much similar to injection molding, compression molding is a time-tested process of manufacturing that is very versatile and is used in creating plastic parts of various shapes and sizes. Compression molding machines are used in mass production and often use materials like rubber, elastomeric plastics, silicone, EPDM, etc.
Finding an ideal plastic prototype manufacturing company that promises quality products and services is incredibly challenging among thousands of choices. Seaskymedical is leading in plastic prototype manufacturing, and its primary focus is to serve clients with high-quality plastic molded products at affordable rates.
Our team uses three techniques to decorate the plastic products that we manufacture in Sydney. These techniques are screen printing on plastic, adhesive and heat transfer labelling. You can choose whichever option best suits your requirements and budget when it comes to grease cartridge decorations. Screen Printing Adhesive Labels Heat Transfer Labels
When it comes to sevice delivery, we rank second to none. Our company has completed thousands of custom projects in Sydney since we started our business way back in 1964. Here are the top reasons why companies, distributors and small scale enterprises love working with us! We have an experienced team working at our site, enabling us to deliver high-quality plastic tooling manufacturing services in Sydney. You can talk to our customer service if you have any questions related to our plastic tooling manufacturing services. Plastic Tooling Manufacturing will provide you with a free quote for grease cartridges, plastic buckets and any other custom product you want.
Before beginning production on a full scale, prototyping helps manufacturers gain an idea about how the physical product is going to be. This helps avoid common and major mistakes in production and makes it easier to produce the most efficient plastic parts with perfect finishings.
A highly economical manufacturing method commonly used in plastic prototype production, extrusion involves the melting and molding of materials by applying huge force. Extrusion is commonly used in high-volume production, and the process begins with melting plastic and ends with a well-shaped finished product.
Mainly the quality of work of a manufacturing company depends majorly on the types of tests conducted, such as step-by-step product inspections, time-to-time machine maintenance, board certification, etc.
Often, a company’s work quality can be assumed from the various procedures for testing manufactured products, the types of raw materials chosen, and the time taken for production and delivery. In some cases, client reviews also help portray the overall quality of the manufacturer’s product and services.
At Plastic Tooling Manufacturing, we have top of the range machinery, assembly, and resources to mass-produce plastic products. Place your order today for 450g grease gun cartridges or plastic buckets, and we will manufacture these items as per your requirements.
Seasky Medical serves you with medical injection molding solutions from design to tooling to material selection and manufacturing. Contact our specialized team and solve your problem now.
Choosing a trustworthy plastic prototype manufacturer amongst the crowd is challenging. However, the quality of the products, the production speed, and the company’s overall experience matter the most.
Grease Cartridges: Lubrication manufacturers and suppliers who are looking for high quality and reliable solutions to their packaging needs should look no further than Plastic Tooling Manufacturing. With over 50 years of experience in mould design and construction while also being responsible for the production of the first Grease Cartridges in Australia (450g variant). Produced locally in our Sydney factory you can be assured of competitive pricing, the highest quality and rapid delivery time frames. Fortunately, you are at the right place because Plastic Tooling Manufacturing can fulfil your requirements when it comes to plastic grease cartridges.
From using the most advanced technology to providing quality assurance, Seaskymedical is one of those accredited and trustworthy medical device molding companies that any business can rely on. Seaskymedical is based in China and is also ISO-certified; therefore, you can be assured about the products you receive.
The tests are performed virtually with the help of CAD or 3D visualization and PDM tools. These help in creating physical mockups of products and finding out errors. Therefore, while prototyping plastic parts, testing and validation processes are significant.
While looking for partners who will enhance your business with advanced prototyping methods and the latest industry trends, quality assurance matters the most.
Plastics are one of the most flexible materials that can be molded in several ways to create the most useful equipment, parts, or devices. From the medical industry to the automobile, electronic, toy, or food packaging industries, numerous industries rely on plastics to manufacture their products today.
Plastic prototype manufacturing involves several combinations of complex technologies that enable the rapid production of plastic parts required by various industries. Prototype plastic molding or manufacturing is mostly in demand in the medical industries, where advanced technologies and manufacturing processes are used for manufacturing plastic parts such as syringes through specific methods like injection molding.
An integral part of rapid prototyping manufacturing, laser cutting and etching is used to cut, and engrave on plastic parts, often to shape them. The most common example of laser cutting and cutting is shaping the glasses of eyewear. Not just plastic, this method is applied to wood, glass, fabric, and so on. Laser cutting and etching methods are controlled by CNC machining.
Equated with rapid prototyping manufacturing, thermoforming involves melting thermoplastics into extruded plastic sheets by applying massive force and vacuuming the presence of air inside molders.
Prototyping before producing plastic parts is the best way of saving time and money. Simply put, prototypes are virtual models that give manufacturers a glimpse of how it will be in its physical form. This model is ready for mass production, but before testing and validating them is a waste of time and money in production. If any errors arise, it will be a total loss producing defective plastic parts.
Testing and validation are one of those initial steps before beginning mass production. The testing and validation process enables the elimination of existing errors in the prototype designs. Usually, validation and testing are carried out through three prototyping processes, including engineering validation testing (EVT), production validation testing (PVT), and design validation testing (DVT).
Plastic prototyping methods are most common in the medical, packaging, automobile, and electronics industries. The global rapid prototyping market is increasing rapidly and is expected to reach USD 32.4 billion by 2031. This market is progressing with a growth rate of 14.9%, and thus, choosing plastic prototype marketing can be profitable for businesses.
In other words, you get access to world-class injection molding and plastic part prototyping solutions at Seaskymedical. From product development to the selection of materials, custom mold making, and exploring the best injection prototype plastic moulding, every process and service of the company meets industry standards. Each product is verified and tested before delivering it to the clients.
Plastic Tubs/Buckets: Aside from multi-purpose grease cartridges, we also manufacture plastic tubs/buckets. We have many size options to suit your individual needs.
Plastic prototype manufacturing is a lucrative market, and the growing demand for plastic parts is evident. Even if the world is inclining more toward switching to eco-friendly materials, certain parts cannot be manufactured without the use of processed plastics. Therefore, plastic prototype manufacturing has a bright future ahead.
Thermoplastics are appreciated for their versatility and their ability to be recycled for reuse. Thermoplastics are very commonly used in plastic prototype manufacturing processes. They are melted and injected into pre-made molds to produce efficient and fully functional parts.
When using complex manufacturing methods like injection molding, special importance is paid to the mold design and the material. And even before that, the prototype design of the mold and the plastic part is passed through various tests to ensure there are no risks involved that can degrade the quality of production or the product.
Ever since the introduction of rapid prototyping, the production of plastic parts has become simpler with the help of high-speed casting, molding, and machining. If your business needs the most upgraded plastic prototype solutions, you must contact Seaskymedical and get your hands on high-quality product development, 3D printing, and injection molding solutions. In return, you get quality assurance and timely deliveries at affordable rates.
Prototype designs are undoubtedly flexible and customizable. With prototyping plastic parts, manufacturers and their clients can introduce new changes in the models or molds. Almost every plastic prototype manufacturer allows flexible customizations. For instance, manufacturing companies help their clients design custom plastic injection moldproduced according to the requirements.
Whereas a company delaying the deliveries is likely less successful, having limited resources and backdated technologies. Therefore, the faster a company’s production, the more technologically advanced they are.
Thermoforming uses extremely high temperatures to melt the thermoplastic pipes and tubes and pour them to form durable plastic sheets that are pliable. These extruded plastic sheets can be cut and shaped in multiple ways to form different plastic parts.
The experience of a manufacturer matters the most; the more years the company has served clients, the more experience it has in providing prototype solutions. Also, more experience means the manufacturer is aware of the industry standards.
Depending on your requirements, you can order buckets of 250ml or 375ml, 500ml, 3L or 20L. More importantly, they are food safe and come with a screw cap and snap lid option. Plastic Tooling Manufacturing can supply these plastic buckets in any colour that you require.
Similarly, a manufacturer who has expertise in plastic prototype manufacturing makes sure each product is passed through several quality inspections and each manufacturing process is carefully inspected to avoid faults. These quality inspection processes include strength tests, durability tests, temperature tests, etc. An expert manufacturer abides by the necessary regulations and offers products that are certified.
From factories to day-to-day necessities, plastic is readily available and the cheapest resource for industries to make the best quality products. A common practice of plastic prototype manufacturing is much more evident in the medical industry. Using complex manufacturing processes like injection molding, a plastic injection molding company can apply high-quality plastic parts to various machines and purposes.
CNC machining is suitable for various industries that need prototypes, such as the medical and automobile industries. CNC stands for Computer Numeric Control. Therefore, investing in tooling is unnecessary because everything is computerized.
It is obvious that a trusted manufacturer with mass production will take the least time to deliver customized orders to the clients. The speed of production depicts the quality of the product and how much they are in demand.
Prototyping is imagining a model before it is manufactured and produced physically. It is much like giving ideas the shape of a product design that will be converted into a physical form with the help of advanced engineering technologies. Prototyping is no less than art; it drives innovation and creativity and turns it into reality in the form of prototype plastic parts.
Injection Moulding Specialists: The quickest and most cost-effective method to mass-produce plastic products is arguably the injection moulding technique. Be it grease gun cartridges, plastic buckets or other similar products, this technique yields fantastic results which are much cheaper than alternative methods.
Plastic rapid prototyping is one of the most common methods of manufacturing adapted by companies today for faster production and better quality maintenance. Rapid prototyping methods are the most modern techniques; they include:
Prototyping helps assume accurate dimensions and reveal the flaws that the product possesses. Designing parts is undoubtedly an exceptional combination of innovation and creativity which gets converted to real-world efficient parts. Modern technologies like 3D printing models enable clients to imagine how the product will look and feel.
A manufacturer is very likely to offer its products at a rate that is comparatively low than that of the price of retailers. Most manufacturing companies sell their products at wholesale rates. Hence, the cost of production is also an important factor to consider. This doesn’t mean every manufacturer offering low-cost products is trustworthy, but the cheapest price can also degrade the overall quality.
Elastomers are perfect for molding; they are mostly available in the forms of silicone, isoprene rubber, synthetic rubber, natural rubber, EDPM, and so on. Elastomers are very common in the medical, consumer products, and aerospace industries. They are introduced to complex manufacturing methods like injection molding to make the most flexible plastic or rubber parts.
Even if technology is rapidly advancing, the traditional methods of prototyping plastic manufacturing are still prevalent. Many manufacturing companies worldwide, even to this date, stick to the traditional techniques that are equally efficient as upgraded ones.
If you would like to make an enquiry, please call us on (02) 9427 4455 or send an email to sales@plastictooling.com. Alternatively, you can reach us by filling out our online contact form and our friendly team will get back to you promptly. We look forward to hearing from you, and we hope to do business with you soon!
The rapid growth in plastic prototype manufacturing benefits various industries, including the medical industry. There are usually two prototype techniques, traditional and rapid. Each of these manufacturing methods has variations and is applied to different types of production.
Decoration On Plastic: The next step is decoration. A company that’s in the business of lubrication distribution or production needs to differentiate their range from others by using a grease container that’s appropriately decorated. At Plastic Tooling Manufacturing, we have just the right tools and resources to decorate our plastic products.
Plastic prototype manufacturing is adapted mostly by any medical plastics manufacturer aiming to deliver top-notch plastic molding solutions to businesses and medical organizations. Mass production help cope with huge demands, and customizations improve the results.
Precision injection moulding is a specialized process that offers unique benefits to various industries requiring high-precision …
As a cost-effective modern plastic rapid prototyping method, Vacuum Casting is fast, but it is only ideal for small-scale production, for instance, 20 units at a time. Several types of rubber and plastic components are used in this manufacturing process to fill them in casts and shape them. The vacuum feature removes the air bubbles inside the casts and molten materials.
Welcome to Plastic Tooling Manufacturing Pty Ltd, your premier partner in plastic packaging solutions. With a passion for high quality plastic packaging and a commitment to provide the best customer support. Our extensive facilities, backed by decades of expertise, enable us to deliver packaging solutions that exceed your expectations. Discover the difference of working with a trusted partner who values quality, reliability and performance.
Rotational molding uses massive force and high temperature to let the plastic powder stick to the walls of the mold and form a hollow shape. This type of manufacturing is common in the mass production of plastic containers and bottles of various shapes and sizes. Rotational molding is most flexible for producing the smallest and the most intricate designs.
Extrusion is a lengthy production process, and the production results are shaped in the form of a continuous profile. This most widely used manufacturing method uses common plastic materials like polyethylene, nylon, PVC, polystyrene, and polypropylene. In some cases, the material used in extrusion manufacturing can also be thermoplastic or elastomer. All these materials are filled in the hopper and melted at temperatures between 350 to 520°C.
We are the plastic tooling manufacturing specialists who can manufacture custom ordered products without any difficulty. Importantly, we can produce them in large quantities, to suit your needs. 400g Grease Cartridges 450g Grease Cartridges
Also recognized as roto casting, roto molding, or rotational molding, this traditional manufacturing process occurs in low-pressure and high-temperature conditions. Rotational molding is applied in manufacturing hollow plastic parts containing a shell-like mold where the plastic powders are added.
Seasky Medical serves you with medical injection molding solutions from design to tooling to material selection and manufacturing. Contact our specialized team and solve your problem now.
The cheapest and fastest way to produce plastic rapid prototyping is 3D printing. This additive manufacturing process creates three-dimensional prototypes and uses low-cost materials like thermoplastic and polylactic acid or PLA for production. Manufacturing companies seeking faster production often switch to 3D prototyping. Precisely, 3D printing allows you to explore plastic rapid prototype designs in the best possible way.
All of these validation and testing processes have one purpose, testing the functionality of the prototype design before mass production is carried forward. Prototype testing and validation combine usability, functionality, and reliability to enhance the design process and production. Generally, these testing and validation processes are most applicable and useful for engineering designs.
If you need custom plastic packaging made, we can get the job done. Our service include injection moulding, screen printing, pressure-sensitive labels, heat transfer labels and tool making. With our wide range of capabilities, we’re sure we can take care of your projects to your satisfaction. If you have questions or aren’t sure how we can help you, just ask.
Plastic Tooling Manufacturing has served customers since 1964, giving us many years of experience in the industry. You can rely on us for quality plastic products and services for your business.
Since a force of air is blown inside the mold cavity to create a hollow component, the manufacturing method is known as blow molding. Not just bottles and containers, blow molding, is also used for manufacturing hollow plastic parts used for several industrial purposes. This process is used for mass production and is the best choice for manufacturing hollow products with the most complex geometries.
The most common material used in plastic prototypes to create the best kinds of prototype plastic parts is thermoplastics. This variety of plastic is available in solid form, mostly in the form of colored pipes that can be melted and molded. Thermoplastics are mostly plastic polymers that can melt down in elevated temperatures and, at the same time, can be cooled easily to form a shape.
We provide ready-made products from our grease cartridge manufacturer, including tubs, buckets and cartridges. These products are leak-free, available in a variety of colours and made right here in Australia. Take a look at what we have to offer, and get in touch with us for more information.
Plastic prototype manufacturing includes flexible processes that involve 3D printing, vacuum casting, injection molding, and CNC machining. Prototyping helps factories design and visualize the parts before beginning the manufacturing process. A virtual model is created before the plastic prototype manufacturing process begins, and an appropriate method is chosen for production. These advanced manufacturing features enable rapid production and produce highly efficient plastic parts.
CNC machining technology is so advanced that it can create the fastest automotive prototypes for production. The CNC machining technology is so fast and efficient that they are often chosen over 3D printing prototypes. Not just plastics, CNC machining, is equally efficient in prototyping metals.
At Seaskymedical, you can expect top-notch services like custom plastic molding, medical plastic injection molding, mold making, 3D prototypes and printing, CNC plastic machining, silicon injection molding, and so much more.
As the name suggests, the molten materials get compressed into the molds to form various shapes. Usually, this manufacturing process is popular in the mass production of plastic parts with similar shapes, sizes, and surfaces.
Extracted from nature, resins comprise synthetic compounds and can be used in several manufacturing processes. Resins are flexible synthetic materials that can be converted to solid or liquid form and mixed with chemicals to harden or soften them. Mostly, resins are used with molds for creating home decor items, jewelry pieces, coasters, furniture tops, and various plastic parts.
FDM or fused deposition modeling is often paired with 3D printing in plastic prototyping. This method is used for manufacturing products layer after layer; the layers are formed by molten materials, mostly plastic.
Plastic extrusions are mostly common in manufacturing prototype plastic parts like tubes and wire insulation or pipes. This manufacturing process is also common in window and door frame-making, window blinds manufacturing, making windshield wipers, and so on.
The manufacturing process of thermoforming interestingly includes a female and a male mold. Both these molds are used for laying molten plastic and pressing them into sheets.
GETTING A QUOTE WITH LK-MOULD IS FREE AND SIMPLE.
FIND MORE OF OUR SERVICES:
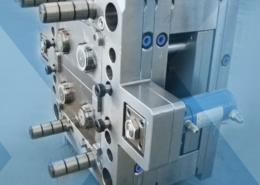
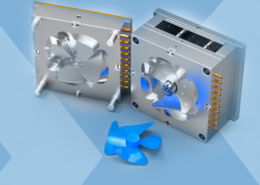
Plastic Molding
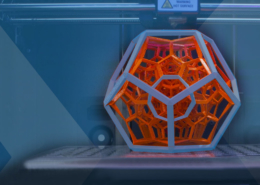
Rapid Prototyping
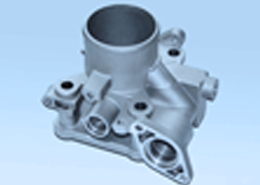
Pressure Die Casting
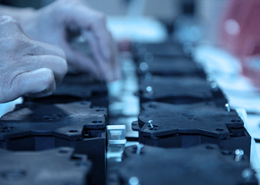
Parts Assembly
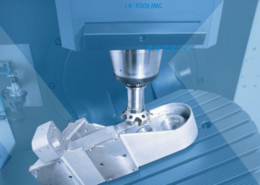