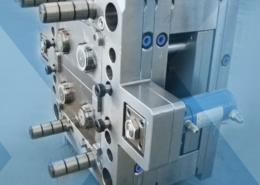
What Is LSR 2-Shot? Your Guide To Multishot LSR Molding - double shot injection
Author:gly Date: 2024-10-15
Quantifiable benefits extend beyond cost reduction. Improved product quality, a significant decrease in waste generation, and a positive response from consumers all contribute to the success of manufacturers embracing recycled plastics.
1. Reduced Environmental Footprint: Utilising recycled plastics significantly diminishes the demand for new raw materials, alleviating the strain on our ecosystems.
In these success stories, there is a common thread of adaptability, open-mindedness, and a willingness to experiment. Embracing recycled plastics requires a cultural shift within the organisation, with employees at all levels understanding and championing the cause.
In the dynamic landscape of manufacturing, the call for environmental sustainability has become increasingly resonant. As a seasoned professional in the field of plastic injection moulding, I am eager to guide environmentally conscious manufacturers, on the transformative journey of incorporating recycled plastics into their injection moulding processes.
Allow me to share a notable success story from my own experience. A mid-sized manufacturing firm, initially hesitant to adopt recycled plastics, witnessed a remarkable transformation. After implementing recycled materials, they not only contributed to environmental conservation but also experienced a 15% reduction in production costs.
We can advise on the design of your product to suit the manufacturing processes required. We can organise tooling for you and manage the project for you so that you receive conforming parts at a competitive price. And we’ll keep doing that for you for as many years as you need us to.
3. Enhanced Corporate Image: Embracing recycled plastics showcases a commitment to environmental responsibility, enhancing brand reputation and resonating with conscientious consumers.
I urge manufacturers, particularly those with a keen eye on sustainability, to consider the transformative power of recycled plastics. In doing so, we not only safeguard the environment but also future-proof our businesses, ensuring they thrive in a world that values ecological responsibility.
Mould design plays a crucial role in the successful implementation of recycled plastics. Consult with experienced mould designers who understand the unique characteristics of recycled materials. Adjustments may be necessary to optimise the performance of recycled plastics in the moulding process.
During my tenure, I’ve observed that regulatory compliance, when approached as an opportunity rather than a burden, fosters long-term business sustainability. Adhering to eco-friendly practices is not merely a legal requirement; it is an investment in the company’s future resilience.
Recycled plastics offer a compelling alternative, addressing both environmental concerns and the need for sustainable manufacturing. Contrary to misconceptions, recycled plastics have evolved into high-quality materials suitable for injection moulding, offering a plethora of advantages.
I recall a project where initial scepticism was replaced by amazement as a state-of-the-art injection moulding machine effortlessly processed recycled plastics, producing components of exceptional quality. Technological progress is propelling the industry towards a future where recycled plastics are not just viable but preferable.
Let’s delve into real-world examples of manufacturers overcoming challenges. In a recent case study, a forward-thinking company integrated recycled plastics into their injection moulding processes, witnessing a 20% reduction in material costs without compromising product quality. These success stories underscore the tangible benefits awaiting those willing to embrace change.
As industry leaders, we bear a collective responsibility to shape a sustainable future. Collaboration, knowledge-sharing, and the pursuit of cutting-edge technologies will define the next chapter in injection moulding. By fostering an environment of continuous improvement, we ensure the longevity of our industry and the planet.
To get your components or sub-assemblies manufactured by us, you can call our team on 01543 462 561 or send an email enquiry to [email protected]. Our team of experts will be in contact within hours to help you with your project.
We regularly mold grades ranging from empty general-purpose grades to fiber-reinforced grades. At Veejay Plastic, we always ensure accurate dimension control while polycarbonate injection molding to avoid the mold shrinkage. In addition, we provide plastic injection molding for a wide variety of FDA approved, UV resistant, flame retardant, and lubricated plastic grades.
Transitioning to recycled plastics requires a strategic approach. Begin by conducting a comprehensive assessment of your current processes and materials. Identify suitable recycled plastics for your specific applications and gradually integrate them into your production line.
Undoubtedly, the environmental impact of traditional plastic manufacturing cannot be ignored. The proliferation of plastic waste has reached alarming levels, prompting global concern and stringent regulations. As manufacturers, we hold a pivotal role in steering the industry towards eco-friendly practices.
Looking ahead, the future of recycled plastics in injection moulding is teeming with possibilities. Researchers and industry experts are exploring innovative methods to enhance the performance of recycled materials, opening doors to even more sustainable practices.
In conclusion, the journey of recycled plastics in injection moulding is a testament to the industry’s adaptability and resilience. As we stand at the intersection of environmental consciousness and manufacturing innovation, the decision to embrace recycled plastics is not just a choice; it’s a commitment to a future where waste is minimised, and opportunities are maximised.
VVeejay Plastic possesses many years of experience in working on various plastic material for injection molding. Our plastic experts will work with you to identify the polycarbonates, which are best suited for your industrial applications. They will explain you how each polycarbonate will contribute to your application. For more information on our PC injection molding expertise, or to get started with your plastic injection molding project, contact us today.
While the initial investment in transitioning to recycled plastics may raise concerns, conducting a thorough cost analysis reveals the long-term savings potential. Factor in reduced material costs, potential tax incentives for sustainable practices, and the positive impact on brand perception.
Navigating the regulatory landscape is a concern for every conscientious manufacturer. However, the use of recycled plastics aligns seamlessly with existing environmental standards and often exceeds compliance requirements. This alignment not only ensures legal adherence but also positions the company as a responsible industry leader.
Molded polycarbonate parts are becoming fast replacements for metal parts in various industrial applications. Following properties of polycarbonates make them an ideal alternative to metal:
One common hurdle is the perception that recycled plastics compromise product quality. Allow me to dispel this myth. Technological advancements have elevated the quality of recycled plastics, ensuring they meet or exceed the standards set by their virgin counterparts.
Polycarbonate (PC) is a popular industrial-grade thermoplastic, which has a high impact resistance, and strength. This is why it is largely used in various industrial applications that demand close tolerance, and durability. Veejay Plastic provides polycarbonate injection molding services to its clients in electronics, aviation, telecommunications, and several other demanding industrial sectors.
2. Cost Efficiency: Recycled plastics often come at a lower cost, providing manufacturers with a competitive edge while contributing to overall cost reduction.
GETTING A QUOTE WITH LK-MOULD IS FREE AND SIMPLE.
FIND MORE OF OUR SERVICES:
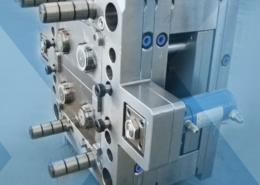
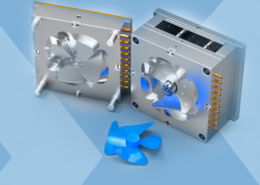
Plastic Molding
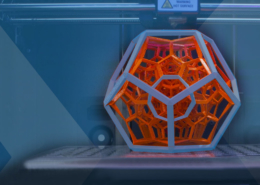
Rapid Prototyping
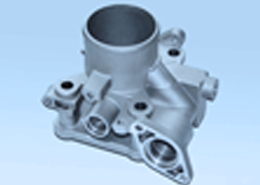
Pressure Die Casting
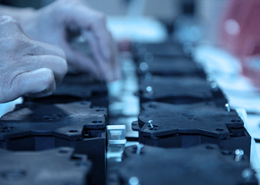
Parts Assembly
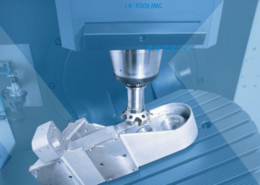