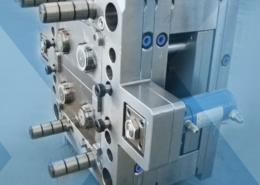
What Is LSR 2-Shot? Your Guide To Multishot LSR Molding - double shot moulding
Author:gly Date: 2024-10-15
Like most plastics manufacturing processes, injection molding has its share of problems and solutions. Same goes for two-shot injection molding — and there’s even more complexity. The key areas to consider when troubleshooting injection molding defects are captured in our Two-Shot Injection Molding Design Guide. Be sure to download your copy today. In the meantime, here are some common two-shot molding defects – and how to avoid them.
Incorporate an accent groove, 1.5 mm – 2.0 mm deep and 0.8mm – 1.0mm wide, in the first shot profile along the edge of the second-shot.
Food-grade containers can also be made using acrylic as it is chemical-resistant and doesn’t have a toxic composition (BPA-free). For this reason, it is used for refrigerator drawers and food containers.
Cause: Usually a poor seal between the first shot and the second shot mold. Or, the material is too thin in the shut-off area.
Acrylic, also known as polyacrylate, is a transparent thermoplastic. It may be known more commonly as ‘PMMA’ or its trade name plexiglass. Its characteristics are strong, lightweight, highly insulating and optically clear. It is easy to fabricate and with its many properties, it has countless applications.
Two-shot injection molding defects often occur in the shut-off areas where the second shot mold seals against the first shot, or the substrate.
Some of the first applications were in the 1940s for aeroplane windows and are still used in similar ways today for their clarity. It fares similarly to polycarbonate (PC), but does not contain bisphenol-A (BPA) and is not as impact-resilient. However, acrylic is copolymerized so as to double up strength and scratch resistance.
Solution: Create a sharp transition between the first and second shot materials in the shut-off areas. To accomplish this, incorporate a step or accent grove into your design:
Acrylic injection moulding is the process of heating the plastic and injecting it into a custom mould using a high temperature and pressure. It is useful to manufacture small parts but is more costly than thermoforming. Mass-production, however, can bring the cost per unit down.
Cause: Unfortunately, all tab gates produce this defect, known as vestige, on the surface of the part. They’re somewhat of a necessary evil.
As for any engineered plastic part, material selection is paramount. Typical considerations include mechanical and physical properties, , heat, electrical, flammability and chemical and UV resistance. For two-shot, if we’re to avoid defects, we must take it a step further and consider the compatibility between the first shot and second shot material.
Acrylic polymer is unrivalled in the plastic market for its optical clarity, and so it makes an excellent replacement for glass. It is just as clear as glass but weighs a lot less and it’s scratch-resistant it serves best as lenses. It can also filter out UV radiation which makes it a viable option for windows too. Moreover, combining plexiglass with polycarbonate can result in the manufacturing of bulletproof glass and aquarium tanks.
The thermoplastic also possesses thermal stability and is easy to work with. Because of this, it can be easily bonded to other substrates to form stronger, or higher shatter-resistant products. The ease of fabrication and high wearability make it a popular option for various products. From things like retail displays and TV screens to things like paint and false nails.
Thermoforming is the process of heating acrylic sheets until it’s moldable. The plastic is then manipulated to form a custom shape. Thereafter, there are a few popular methods that come into play to finish off the shaping process.
As discussed in our Two-Shot Injection Molding Design Guide, the type of gate, its design, and location must be carefully considered to achieve the ideal cosmetic appearance and dimensions of your part. In single-shot injection molding, the gate is typically located so that the melt enters at the thickest part of the cavity and then flows to the narrower areas. Its placement in two-shot isn’t as straightforward.
Acrylic moulding is also a poor choice when it comes to strength and impact resistance. PC is a better alternative for that but as mentioned before, copolymerisation can solve this issue.
Acrylic polymer is an inexpensive and easily pliable resource on its own, and even stronger when combined with other plastics. Its attributes allow it to service the construction, beauty, medical and food industries. Its non-toxic nature can allow for high-quality food and medical-grade products which can be created via mass injection moulding.
Two-shot design can deliver a competitive advantage far above other molding processes, especially for complex parts. Learn the benefits of the process and explore the special design requirements needed to make it work in this free guide created by engineers, for engineers.
On the other hand, the fumes released from molten acrylic during injection moulding should not be inhaled as they can cause internal harm. To avoid any ill effects, the moulding process should be performed in a well-ventilated area.
If the two materials are somewhat compatible and you simply need to increase the strength of the bond, try maximizing the surface area in the transition zone.
Solution: The solution to the first-shot vestige is quite simple – position it so that the second shot material covers it! The second-shot vestige, however, will require additional processing after the mold cycle. The only way around the vestige all together is to use a hot tip gate, depending on the part design.
GETTING A QUOTE WITH LK-MOULD IS FREE AND SIMPLE.
FIND MORE OF OUR SERVICES:
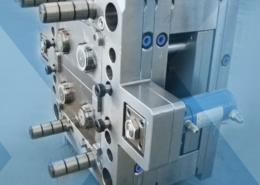
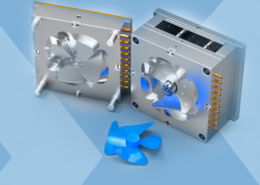
Plastic Molding
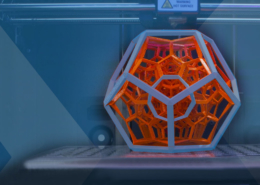
Rapid Prototyping
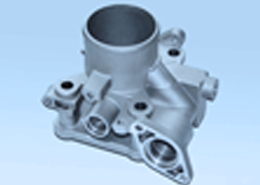
Pressure Die Casting
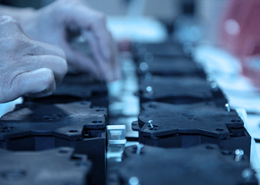
Parts Assembly
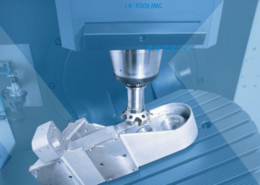