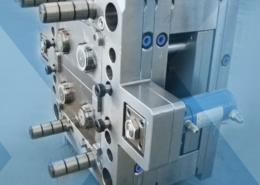
What is Overmolding? | Richfields Blog - plastic overmolding
Author:gly Date: 2024-10-15
Flash is what happens when the plastic injection material seeps into the mold seams during the injection process. The excess material will need to be removed in post-processing. This post-processing can be expensive depending on the amount of flash and the work required to remove it. Aluminum molds for injection molding are prone to flash. Aluminum is a soft metal and is therefore easier to deform and allow the injected material to leak out of the machined cavity. Steel is a harder material, which reduces the chance for flash. Steel molds will not deform as easily as an aluminum mold.
Are you a product designer or engineer that is looking for more information on how to make your plastic part design more efficient in regard to cost and production time? One important consideration during the part design process is to have a good understanding of plastic injection press basics including the size of machine needed for your part.
Steel molds are much more durable and can last up to 100,000 cycles or more. While aluminum molds may be cheaper to machine, the steel mold will last ten times as long – producing parts long after the aluminum mold has been scrapped and replaced several times. The cost of machining a new aluminum mold after every 10,000 cycles will add up quickly.
An aluminum injection mold will last 3,000 to 10,000 cycles. Each cycle represents the mold closing, the mold being filled, the mold opening, and the part being ejected. If the mold has a single cavity, customers can expect to get up to 10,000 parts from an aluminum mold.
Regular injection mold maintenance can help your mold last longer, run with less interruptions & will ultimately save you time, money & frustration.
ICOMold’s fast-turn, low-cost, high-value injection molding enhanced by joining Fathom’s manufacturing platform. Learn More
Injection molded material can impact the life expectancy of the tool. Aggressive materials like ASA/glass-filled Nylon and Ultem can reduce the lifespan of injection molds. Steel injection molds can be hardened through heat treatment to become extremely durable. The heat treatment will allow steel molds to handle the aggressive material without issue. Aluminum molds for injection molding cannot be hardened and will not be able to handle the high injection pressure and temperature required when injecting these aggressive materials.
Steel molds offer more options for surface finishes. The high-density nature of steel allows more texture selections. Custom, tall, or deep details in the tooling can be achieved by adding steel inserts. The number of surface finishes possible with an aluminum mold is limited and custom finishes are not available. The difference in available surface finishes is based on the mold material. This limitation affects all mold makers, not just ICOMold.
Your plastic injection molder should help you determine the size of the machine needed to help you achieve the best result for your product. Knowing an approximate size of what will be needed can help you determine the best injection molding partner based on the press capacity they have available. For example, larger presses cannot accommodate smaller molds because they can’t close far enough and the injection process will not work.
“Bigger the better” is not always the case when determining the press size needed. In the molding process, plastic is injected into the mold at an exceptionally high-pressure rate, which creates a natural pull to force the mold open. A press is designed to keep the mold shut with larger parts requiring more tonnage and force, and smaller parts requiring less. A general calculation for determining press size needed is as follows:
Aluminum can be used to make molds for the injection molding process. Aluminum is an affordable material that is easy to work with and has many applications. However, aluminum molds, while slightly cheaper to produce, are considered inferior to steel molds. ICOMold by Fathom uses only high-strength steel to manufacture injection molds.
The most successful parts are created when there is constant communication between a part designer, tool designer and manufacturer.
Aluminum molds have a limited manufacturing life span. Aluminum is a soft metal and cannot with stand the repeated pressure and temperature of the injection molding process. Aluminum molds will produce 3,000 to 10,000 cycles before needing to be replaced. Steel molds are more resilient and will produce 30,000 to 100,000 cycles before needing to be replaced or repaired.
Consistent quality parts start with a quality, well-made and maintained mold. What expectations should you have for the care of your investment?
Designing a plastic part for manufacturability from the outset involves several considerations that can have a significant impact on key variables
Aluminum injection molds cannot be used for complex parts. Aluminum is a softer metal that can only be used for simple injection molded designs. Designs with complex geometry will need to be made with a steel mold. The steel is better able to handle complex designs and any thin walls in the design. Aluminum molds cannot handle thin walls or complex geometry because the metal is not as structurally strong as steel and will deform during the molding process. This is a universal limitation for all mold makers – not unique to the ICOMold by Fathom manufacturing process.
Having a general understanding of how to calculate press size is a good first step in determining what injection molding partners are available to you. Strong partners will make recommendations on how to appropriately tweak your part to ensure the final design fits your manufacturing needs and reduces upfront tooling costs. Nicolet Plastics has press sizes up to 610 tons.
Steel molds can be modified and repaired after initial tooling. Aluminum molds cannot be changed or repaired if there is a problem with the initial design. Steel molds can be modified with welding. If a part re-design requires less plastic in an area, and therefore, more steel in that area of the injection mold tooling, the steel mold can be modified. This is not the case with aluminum. Consider using a steel mold if there is any chance your part may undergo design revisions that will require modifications. Steel molds can also be repaired in some instances. This will save customers thousands of dollars by simply repairing the mold instead of machining a new mold. The ability to repair a mold will depend on the tooling. Not all steel molds will be able to be repaired.
Calculating shot volume to make sure your barrel has enough capacity can be accomplished by working with your injection molder to run a mold flow analysis. On some engineered materials, the increased residence of the material in the barrel can cause the material to degrade, resulting in poor part quality. Mold flow analysis will help you determine the volume of your part and runner while determining any factors that would cause safety issues.
In order to streamline your process, consider these questions before requesting an accurate quote for your part design, development and production.
An aluminum mold will hold up for short part runs and is an ideal choice for small orders. However, steel molds are more durable and suited for extended manufacturing runs. Aluminum molds do not have the corrosion resistance or thermal stability found in steel molds. Steel molds are also better able to resist the constant wear and tear of the injection molding process. These characteristics allow the steel injection molds to achieve higher production cycles and withstand non-conformities in the product. Aluminum molds must be anodized or plated with nickel to reach the same level of hardness as steel molds. Anodizing and plating will increase the tooling cost and negate the benefit of using the less expensive aluminum to machine the mold.
Design is one of the most important factors in avoiding part defects. Avoid mistakes that can be costly both in regard to time and budget later on.
“Safety factor” is an additional percentage added to your calculation as a buffer to help reduce defects in your part. Most injection molders will recommend 2.5 times the surface square inches of the part and an additional 10% as a safety factor. If you have a part that is 120 square inches, you would need a press size with 300 tons of pressure. When you add the 10% safety factor, the required press size would have 330 tons of clamping force.
When determining press size for your plastic part, it’s important to calculate the total projected shut-off area. This area consists of only the space that is 90 degrees to the direction of the injection molding machine platens. Thickness does not have any implication on the clamp tonnage and the general rule is to have 2 to 5 ton of clamp tonnage per square inch of projected area.
Injection molding is a manufacturing process that uses a metal mold to manufacture large numbers of plastic parts. ICOMold by Fathom uses only high-strength steel when making plastic injection molds. Steel molds have several advantages over aluminum molds. Steel molds consistently produce a higher quality product when compared to aluminum molds. Steel molds are built to last — up to ten times longer than aluminum molds. Steel molds may have a higher up-front price but they can save significant time and money down the road.
Pressure plays a significant role in the overall quality of a plastic part. Pressure keeps the mold closed during the injection process. Too much or too little pressure can cause various issues such as flashing and viscosity. One important consideration in regard to pressure is that plastic compounds react differently from one another based on their Melt Flow Index (MFI). MFI measures the ease of flow of a thermoplastic polymer and the higher the MFI, the higher pressure needed to create a successful part.
Aluminum cannot be used as the injection molded material. The manufacturing process of metal injection molding does exist, however, aluminum cannot be injected molded. ICOMold by Fathom specializes in injection molding custom plastic parts. ICOMold can also manufacture custom metal parts with Computer Numerical Control (CNC) machining. As part of the Fathom manufacturing network, ICOMold will work to match customers to manufacturers in order to meet their specific aluminum machining needs.
Additionally, smaller presses have tie bar spacing too narrow to accommodate larger products. If the mold doesn’t fit between them horizontally or vertically, you must move up in press size. Many injection molders offer press sizes ranging from 68 tons up to 400 tons.
GETTING A QUOTE WITH LK-MOULD IS FREE AND SIMPLE.
FIND MORE OF OUR SERVICES:
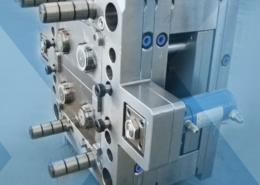
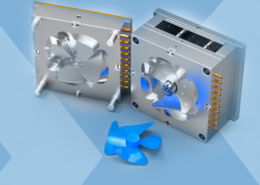
Plastic Molding
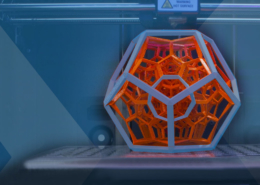
Rapid Prototyping
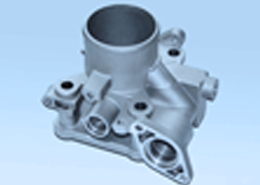
Pressure Die Casting
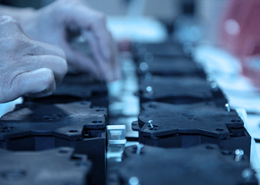
Parts Assembly
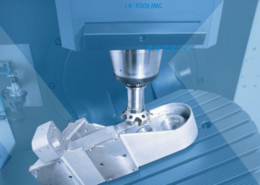