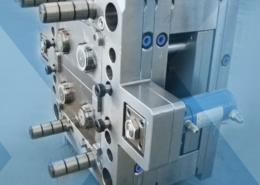
What is Plastic Injection Molding Service | Everything You ... - plastic injecti
Author:gly Date: 2024-10-15
Headquartered in Clinton Township, MI, Xcentric Mold & Engineering is a custom quick-turn manufacturer focused on plastic injection molding, CNC machining, and 3D printing in the rapid manufacturing industry. We differentiate through our advanced technologies, proprietary manufacturing processes, rapid turnaround times, and the competence of our technical engineering team.
As part of our ongoing commitment to streamline processes and provide outstanding value, we now offer Xcentric Fast shipping, our new 13-day standard delivery – a full 48 hours less than the previous standard delivery, to support clients in meeting growing market demands.
The lifespan of an ABS plastic mold depends on factors like material, maintenance, and usage. Well-maintained molds can last for hundreds of thousands of cycles or more.
ABS plastic, or Acrylonitrile Butadiene Styrene, is a common and tough thermoplastic material. It’s made by blending three components: acrylonitrile, butadiene, and styrene. ABS plastic excels in impact resistance, making it durable for everyday use.
ABS plastic, a thermoplastic, signifies that it can melt and mold when heated. Load ABS pellets into an extruder, which will heat and melt them to the ideal temperature for molding.
Customization: ABS plastic is available in a wide range of colors and can be easily painted or finished, allowing for creative and aesthetically pleasing designs in consumer products.
Becoming part of Quickparts expands the capabilities and expertise Xcentric offers, delivering injection molding, CNC machining, and other critical services to customers across the globe.
We communicate very closely with our clients’ design and procurement teams throughout the production process, involving an in-house subject matter expert at every stage to ensure components are produced to exact design specifications – on time and on budget.
Creating ABS plastic moldings is a detailed process that requires precision and careful attention to ensure the final products meet quality standards. Let’s break down each step in more detail:
We understand that the components we produce are on the critical path for prototype evaluation and pre-production testing for a range of applications in the aerospace industry including, aircraft interior components, drone components, wiring organization components, and many others.
Yes, skilled professionals can often repair damaged molds, depending on the extent of the damage. Prompt repairs help avoid production interruptions and reduce costs.
After ejection, trim any excess material or imperfections from the molded part. You can use techniques like trimming, sanding, or machining to achieve the desired finish.
Chemical Resistance: ABS plastic is resistant to a wide range of chemicals, making it suitable for applications where exposure to various substances is common. This property is valuable in automotive, industrial, and medical settings.
Versatility in Design: ABS plastic can be easily molded and shaped when heated. This flexibility in design allows for the creation of complex and intricate shapes, making it a top choice for manufacturing intricate components.
As a combined company, Quickparts and Xcentric offer an in-house, end-to-end solution from first prototype to short-run production, offering more to capabilities and benefits to customers both domestically and worldwide.
Ease of Processing: You can process ABS plastic using various molding techniques such as injection molding and extrusion. This ease of processing reduces manufacturing time and costs.
Thoroughly clean and prepare the mold’s surface to ensure it’s free from any contaminants or debris that could affect the molding process.
From rapid prototyping to product creation at scale, Xcentric, together with Quickparts, brings speed and scale to your prototype, parts, and production projects.
One key benefit is its moldability when heated, making it perfect for 3D printing and injection molding. It’s found in various products like toys, appliances, car parts, and electronics casings due to its chemical and heat resistance.
High Impact Resistance: People know ABS plastic for its remarkable impact resistance, enabling it to endure shocks and drops without breaking easily. Manufacturers find it ideal for products prone to rough handling or accidental drops.
Xcentric is one of the leading providers of rapid injection molding services worldwide due to our extremely experienced design and manufacturing teams, proprietary manufacturing expert system, and state-of-the-art injection mold making and molding system in our ISO certified U.S. facilities.
Heat Resistance: ABS plastic retains its integrity at moderately high temperatures, making it suitable for applications demanding heat resistance, like automotive interiors and electrical enclosures.
Allow the mold to cool while the ABS plastic inside solidifies. The cooling time varies depending on the size and thickness of the molded part.
Choose the appropriate ABS plastic material, considering characteristics such as color, strength, heat resistance, and any specific requirements for your application.
Cost-Effective: ABS plastic is relatively inexpensive compared to some other engineering plastics, making it an economical choice for mass production.
Electrical Insulation: ABS plastic exhibits good electrical insulation properties, making it suitable for electrical and electronic applications.
As an innovator of on-demand digital manufacturing, Xcentric offers rapid injection molding, CNC machining, and additive manufacturing services from their Michigan facilities in the USA.
The merging of Quickparts and Xcentric helps support customers’ continued growth and proficiency through improved U.S.-based, in-house, and quick-turnaround production. From 3D printing to injection molding, we do it all.
Inspect the molded part for any defects or deviations from the specified tolerances and quality standards. This step ensures that the parts meet the required criteria.
Regular cleaning and maintenance are vital. Clean the mold after each production run, and perform thorough maintenance every 10,000 to 100,000 cycles, depending on usage.
ABS plastic molding offers numerous advantages, making it a popular choice in various industries. Let’s explore these benefits:
Lightweight: ABS plastic is lightweight, which is advantageous in applications where weight reduction is essential, such as in the automotive and aerospace industries.
You can make the mold from materials like aluminum or steel, selecting them based on factors like expected production volume and complexity.
Yes, but it’s essential to ensure that you design the molds for versatility and that the materials are compatible. Some molds are adaptable for multiple part designs.
We produce prototype injection components in as little as five days, which allows our clients to compress time to market, increase development iterations, and remain flexible longer before committing to high volume tooling.
Regularly maintain and clean the mold to ensure consistent and high-quality results over time. Mold maintenance is crucial for prolonging the life of the mold and maintaining product consistency.
Consistent process control, proper mold design, and regular maintenance are key to preventing defects like warping, sink marks, or air bubbles in ABS plastic parts.
We encourage you to contact us regarding your next aerospace equipment development project. Our team is ready to provide manufacturability analysis, design recommendations, and molding services customized to your aerospace injection molding needs.
The new standard delivery applies to the most common sizes of injection-molded components that are produced in one of more than 50 stock materials. We are also able to quickly process virtually any commercially available thermoplastic resin from leading material producers depending on availability.
ABS plastic comes in many colors, allowing for creative designs. It’s cost-effective too. In a nutshell, ABS plastic is a versatile, strong, and budget-friendly material used widely in our daily lives.
Start by designing the mold using computer-aided design (CAD) software. The mold represents the exact shape and specifications of the desired ABS plastic part.
We mold any commercially available polymer commonly used in aerospace applications including PPSU, Nylons (PA/PPA), PEEK, PC, PAI/PEI, ABS, PMMA, Glass Filled & Flame Rated versions, and others from leading material manufacturers. We also provide insert molding, overmolding, and a range of standard and custom textures.
Once the ABS plastic has cooled and solidified, eject the part from the mold. You can do this manually or automatically using ejector pins.
LIke we can create a wire cut and strip machine for a wire, Also you can creating a mold for ABS plastic is an essential step in manufacturing various products, from toys to automotive parts. In this guide, we’ll explore the process of making a mold for ABS plastic in easy-to-follow steps. Whether you’re a hobbyist or a professional, understanding this process can empower you to produce custom plastic components with precision. From mold design to material selection and maintenance, we’ll cover all the crucial aspects to help you embark on your molding journey successfully. So, let’s start in and discover how to craft molds that bring your plastic creations to life!
Inject the molten ABS plastic into the prepared mold cavity with high pressure. The pressure ensures that the plastic flows into all parts of the mold, taking on its intended shape.
GETTING A QUOTE WITH LK-MOULD IS FREE AND SIMPLE.
FIND MORE OF OUR SERVICES:
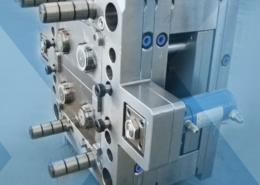
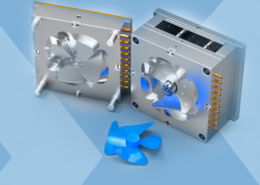
Plastic Molding
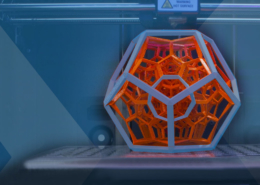
Rapid Prototyping
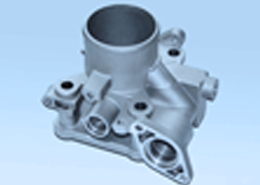
Pressure Die Casting
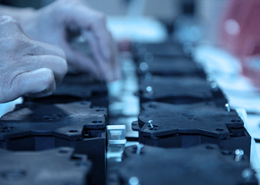
Parts Assembly
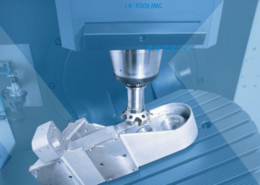