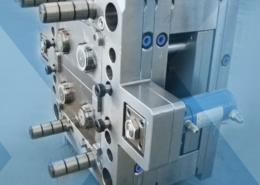
Why Can't PTFE Be Injection Molded? - teflon injection molding
Author:gly Date: 2024-10-15
Polycarbonate injection moulding material typically provides accurate dimension control, lightweight, and outstanding optical characteristics that allow light transmission.
The size of the goods will usually increase the price. Larger pieces are often more expensive since they necessitate a more expensive mould and more material.
And now it's time to reveal the molded model. We can take off the duct tape, open the "seam cut" and start taking off the mold, carefully if you have small parts that stick out, like, in our case, the ears of the cat. Don't worry if some of the layers from the 3d printed mold are visible on the model. This means that the paste sticks very well on the walls otherwise you will see bubbles, cracks etc. As the whole procedure worked well in the first trial, we repeated the process more carefully, taking an almost perfect outcome this time!
The sole disadvantage of ABS is that it is not appropriate for exterior parts due to its high resistance to harsh weather.
This could result in a higher moulding cost. It’s also worth noting that more significant components take longer to produce, resulting in higher prices.
Because of its permitted coefficient of friction, moulded injected nylon is ideal for high friction and wear applications.
The liquified polymer is essentially forced through the nozzle of the moulding machine’s barrel. Usually, the nozzle is seated against the bushing sprue and locating ring on the mould, which serves to centre the nozzle on the mould.
Polymer 3D printing is usually an additive process of manufacturing whereby the whole process is made by adding material layer by layer.
This polymer injection moulding machine component permits the plastic to flow through the sprue, bushing onto the specific rollers that transport the ingredients to the gates.
When you're printing lots of ABS supports, rafts, brim etc go to waste without being able to reuse them. This instructable shows how to easily turn ABS waste in molded objects, without just throwing it away and litter the planet even more. This instructable can be used by professionals, as well as amateurs users, cause it's quite easy and all the consumables are easy to find.
For example, if the polymer is perfect for manufacturing kitchen equipment but tends to have higher polymer density, it may not be a viable choice.
ABS is a technical thermoplastic with a low melting point, making it easy to mould. This substance is an impenetrable polymer that allows colourants to be used.
The capacity to bend and mould under stress without wastage and tear is typically used to assess the material’s flexibility.
The only drawback of a stack injection mould is that it usually needs a press with a much larger inlet to fit the height mould.
It typically eliminates any need for manual removal and separation, and the runner system and sprue can be fed straight to the recycling system.
Inaccurate calibration is one of the causes of short shots, as the plastic material may be insufficient to fill the voids.
All aspects of part design, including design moulding, are frequently studied to ensure that thin wall geometry holds up without causing quality difficulties.
Also, you could fix your model with all the known post processing and painting 3d printing techniques, lots of which you can find in various Instructables.
The penultimate stage of the polymer moulding injection process is often ejection. It is always accomplished using a machine’s ejection system.
It is particularly critical since cost must be considered because the material will be used for polymer moulding mass manufacturing.
Polyamide is a substance that has a big group and can be synthetic or natural. Nylon is always an artificial kind of polyamide in this circumstance.
We have a complete guide and support for every level of your ordering processes until it delivers safely to the place and time we have agreed. We have responsible sales staff who are willing to talk and tackle to you the prices and requirements.
They are highly flexible materials commonly utilized in automobile components, healthcare manufacturing, gaskets, and electronics, among other applications.
One thing we added to our mold, is what we called a "seam cut". That is actually a vertical "guide" to help you cut open your mold, like a zipper, which helps very much in taking off the molded object. This can prevent the object from breaking or cracking while taking it out of the mold, especially when the objects have difficult geometries.
This liquid crystal polymer injection molding has a mold lifespan of 5,000,000 to 30,000,000 shots. Inox Cast assures your well-protected importing.
It provides advantages such as strong tensile strength, the ability to hold tight tolerances during the injection moulding process, and the ability to resist smells.
The intense heat surrounding the barrel then melts the granules. The shot is the volume of injected materials in most cases.
Because this guide covers all information you need about polymer injection molding process, benefits, and techniques, among other vital aspects.
Typically, the hydraulic system in the machine controls and determines the injection rate and pressure that can be reached at this step.
Softer plastic is more malleable and is utilized to create things that require many patterns while being resistant to high temperatures.
Inox Cast manufactures this high-grade polymer composites injection molding with reliable materials to make possible its lasting lifespan.
Inox Cast is the best partner you can always rely on especially with our offered high-quality polymer injection moldings. Perfect finish products are what Inox Cast can assure you when you use our polymer injection molding for your applicable business.
This polymer electronic switch injection molding is widely purchased by a lot of electronics-related plants and businesses. Inox Cast offers you with competitive cost.
This full trim polymer injection molding is widely applicable in molding electrical products and plastic products. We offer molding at a reasonable cost.
So now, that you have your mold and paste you are ready to go! For the third step you need to secure your "seam cut" with some strong duct tape and start pouring your paste. Our advice is to pour it in steps, depending on the mold's architecture... So in our case we poured paste in 3 steps, each time slightly tapping the mold so that the air bubbles come up and escape the mold. We also turn the mold a bit, so that the paste sticks on the mold's walls in the difficult parts, creating a cylindrical skin that gets filled with paste afterwards. This helps to ensure that you get a good model in the end of the procedure. This was the second very important solution that we followed to fill the difficult parts of our mold. We waited 12 hours for each part to harden, and for the last part, we left the mold for 3 days to harden as much as possible!
Polymer injection moulded parts are frequently required in homes, particularly in the kitchen. Plastic plates, plastic food containers, and various utensils are included.
The larger the number of cavities, the higher the production cost. In general, cavities require less tool work and time, lowering costs.
The portion is pushed out when the mould opens. Because the pieces generally attach and shrink to the mould walls, force is required.
In the end of this instructable, we'd like to add that, another great procedure that you could add to this technique, that really helps a lot, is putting the mold with the paste in an air vacuum, so that you are 100% sure that you have no air in your mold. In this case, you should fill all your mold with less thick paste than we use in this paradigm, vacuum it, refill it if needed, vacuum it again and leave it to dry again for at least 2 days. This should be enough in this case. If not simply repeat the refill-revacuum procedure.
In contrast, Polymer injection moulding involves heating a polymer material, filling it with liquid, and then chilling it before ejecting the solid shape part.
It includes injecting pressurized nitrogen gas into the mould and pushing the plastic into the extremities while hollowing out thicker parts.
So, what you first need to do is to collect in a box all your wasted ABS prints. Secondly, you could (or not) categorize them by color. Thirdly, you need enough ACETONE to create the ABS paste. Last but not least, get acquainted with the casting/molding procedures, which you could easily learn through the instuctables lessons.
This 2 shot polymer injection molding is suitable for all kinds of products with raw materials, including specific households, electronic parts, and many others.
One of the most common causes is the variable speed at which the plastic molten flow changes direction as it passes through the curves within the moulding machine.
An injectable process produces a plastic component with a very thin wall. It’s primarily found in electrical containers, test instruments, tubes, and similar items.
It is a distortion that develops when unequal shrinkage occurs in different moulded components. It usually produces uneven results with no twisted or bent shape.
PMMA (polymethyl methacrylate) is a simple material that provides a lightweight, shatter-resistant alternative to glass.
This customized rugged polymer injection molding is securely delivered. You can expect no damaged products from Inox Cast.
Although it has similar qualities to PMMA, polycarbonate material maintains its physical properties over an extensive temperature range.
It is a moulding manufacturing process for parts production in which molten polymer can be injected into a hollow mould through an aperture under high pressure.
Ths polymer injection shaping molding is widely applicable in product designing, mold development, and many other applications.
Keep on updating and visit our page for more upgraded models and designs that exactly suit your desired finish products. We are open 24/7 for your anytime question and ordering our best polymer injection moldings. Approachable staff will accommodate your orders immediately.
Inox Cast produces this die maker polymer injection molding with compression mold shaping mode. We assure you a suitable design you desired based on your requirement details.
Now let's take it step by step, if you have (or not) grouped your ABS waist, you need to cut it down in small pieces. Then you should put them in a glass jar (the bigger the better), with an air tight cap if possible, otherwise you could just use duct tape to ensure that. In our paradigm we used a small one (100ml), because of it's opening, which helped us pour it easily in the mold. This actually depends on your mold model, but we'll get back to it later. Now, put the trimmings in the vase and fill it with ACETON until the trimmings are covered. Then close the vase as tight as you can. The time needed to melt the mixture down to a homogenous paste and the analogy of trimmings/ACETON differs depending on the brand and quality of the ABS you're using. In our case it took 24 hours for the mixture to melt down. Keep in mind that the preferred thickness of the paste is to be like honey.
Thanks a lot for your time. We hope that you'll come up with some beautiful designs with even more details, that can help all the community. We'll be waiting on that and your feedback!!!!
Other factors that influence the cost of polymer moulding injection include tolerance, part surface polish, and undercut.
Thanks a lot for your time. We hope that you'll come up with some beautiful designs with even more details, that can help all the community. We'll be waiting on that and your feedback!!!!
A molten polymer is forced under high pressure into a hollow mould through a sprue in this moulding injection technique.
Trusting Inox Cast helps your business productivity increase considering its qualities. Various polymers are being used in injection moldings, including polyethylene, polycarbonate, polyamide (Nylon), and polypropylene.
Nylon polyamide has excellent abrasion resistance, is strong, has excellent fatigue resistance, and has noise dampening characteristics.
Inox Cast gives the best polymer injection molding for our beloved customers. We have been in the manufacturing industry for almost 20 years: enough experience to provide all types and even your customized polymer injection moldings.
When a runner is employed, it usually links to the moulded product and requires hand separation and removal once the parts are ejected.
Polymer is more applicable in injection molding as long as it is advanced ceramics. Inox Cast can lead you to the most suitable type you need. In Inox Cast, you will never regret spending your money to purchase our offered polymer injection molding considering its enduring quality and operation.
In the initial step in polymer moulding injection, clamping is necessary to close both mould halves before injecting the material.
Mould clamps often employ huge bolts to keep them in place, although other machines may use magnets to secure the mould to the platen.
Inox Cast can customize this polymer plastic injection molding according to your preferred specifications. We assure satisfaction when you choose our products.
Inox Cast guarantees you the best operate hot runner polymer injection molding. We introduce its negotiable price depending on the number of your orders.
You can experiment with different thicknesses, depending on the mold design (less thick means you let the air escape easier) and also with PLA paste, as ACETONE also dissolves PLA, but theoretically ABS works better. Lastly, you should always have in mind that, as your paste hardens, by evaporating it's acetone, you volume might decrease. That also depends on how thick you've made your paste and that is why this technique needs to be done in parts, as it prevents from leaving hollow, empty spaces and gaps.
A polymer injection machine comprises several components that allow molten plastic to be moulded and cooled into a distinct part shape.
The material is screw fed forward and forced into the mould spilt, filling the cavity with a feeding system including a sprue runner and gate.
It’s a pattern, streaks, or lines that appear on plastic parts due to the plastic molten’s physical channel and cooling pattern as it flows to the cavity tool mould injection.
The polymer material is injected into the valves as the clamping unit squeezes them together. If you use a larger machine, closing the halves may take along.
They can also occur whenever polymer runs through a part with varying wall thicknesses and when the flow velocity is too slow, resulting in the plastic hardening at different rates.
Extrusion of polymers It’s a technique that involves heating material and forcing it through a pre-cut shaped metal plate.
Also, you could fix your model with all the known post processing and painting 3d printing techniques, lots of which you can find in various Instructables.
For example, certain resins are pretty expensive due to their excellent quality, whilst others with medium or low quality are significantly less expensive.
Inox Cast offers samples of this high-quality polymer injection molding that are available for open molds. We made it more beneficial.
These are the mould sections where the pieces are moulded into the desired forms. Moulds must be balanced, with a set number of cavitations permitted.
Moulds are typically manufactured with internal cooling lines that circulate water through the mould to maintain a consistent temperature.
While the trimmings turn into paste in ACETON, prepare your mold's model. What you need is to find or design a model, that prevents the mold from accumulation air blobs and to get easily filled in with paste. In a way designs that approach the geometry of a pyramid (or triangle) are easily turned in to molds for such use. So, in our paradigm we chose this cat, that had 2 "difficult" parts. The first one is the chin and the other on the ears, but we'll tell you more about how we solve that later. And now you need to print your mold, and since flex filaments don't get dissolved by ACETON, you need to use a flex material that has the appropriate elasticity for the mold, so that you can take off your model and also create a water tight mold, with no internal overhangs or stringing, so that you can get a clear model. In our paradigm, we used TPE printed in it's lowest temperature and the fastest speed (that is actually depended on the brand of your filament and your printer). Also we used 3 bottom and top layers, 2 peripheries and 15% infill and 0.15mm resolution to achieve all the necessary characteristics mentioned before. If you use a more elastic flex filament you might need to increase the infill and/or the peripheries and top/bottom layers (these factors depend of your filament, printer and mold model). You may need to make 2-3 prints until you find to the right mold for you.
Inox cast maintains the excellent quality of our offered polymer injection molding and other related products. Considering that we have 2 times a real-time x-ray inspection machine. We also operate immersion and vacuum pressure testing for the best performance of our products. Inox Cast also has 4 times quality polymer injection molding tested by CMM machines with PC DMIS software. We are really your trusted supplier not only for the qualities but also in terms of our gratifying services. Encounter our uncomplicated processes and accomplish finished products by Inox Cast polymer injection molding.
In the cat's mold was the first time we used this guide and we were very excited with the object's quality and the mold's ease of use. Also, we added two "air ducts" in the ears in order to ensure that all the air comes out of the mold. This also appeared to be very helpful and a great impact to the quality of the model.
The runner will instantly separate from the product whenever the mould injection is opened, allowing for separate handling.
It is a portion of the polymer moulding injection machine in which the shot of hot plastic is cooled through cooling channels that allow for conduction cooling of the pieces.
It will be harder to design during the production process if the component is more complicated, and would also be more expensive in the end result.
Inox Cast offers you the customized specifications of any polymer injection molding camera. You can get what you wanted type of the said product.
Inox Cast has great know-how in every stage of sourcing customers, even throughout the country. We are very responsible for providing your exact detailed polymer injection molding.
GETTING A QUOTE WITH LK-MOULD IS FREE AND SIMPLE.
FIND MORE OF OUR SERVICES:
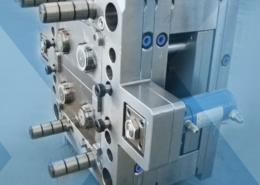
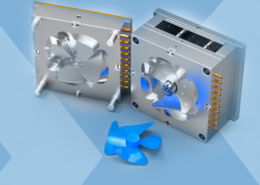
Plastic Molding
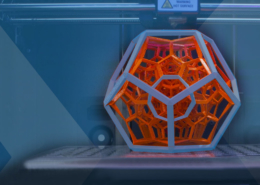
Rapid Prototyping
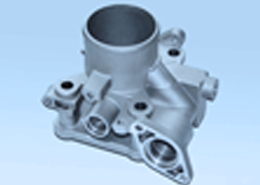
Pressure Die Casting
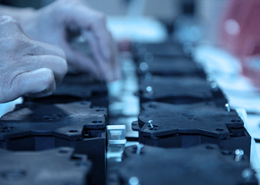
Parts Assembly
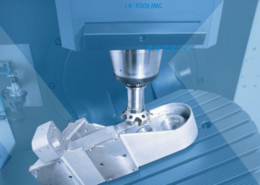