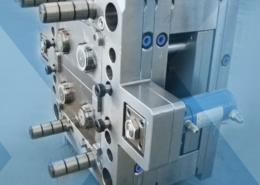
Why Gas-Assisted Injection Molding Simulation? - gas assist injection molding
Author:gly Date: 2024-10-15
This combines the advantages of hydraulic power transmission with the control quality and dynamics of energy-efficient electric drive technology in conjunction with intelligent software. A great deal of energy can be saved with this configuration. In the field of plastic injection molding machines, the servo-hydraulic drive has already established itself as a standard.
Global warming and the measures introduced by politicians to meet global climate targets are giving the issues of sustainability and the circular economy a considerable boost. The processing of recyclate, the design and use of thin-walled products in order to reduce the use of material or, for example, the substitution of heavy metallic materials with plastics in the area of e-mobility are being implemented with ever greater consistency. These and other measures should help to reduce carbon emissions.
Optionally, a capacity module can be integrated into the DC link for the intermediate storage of excess energy. This means that energy can be stored and freed up again as needed in the event of a power failure or when braking the drive axes. Furthermore, after a power failure or malfunction, it is possible to move the drive axes to a defined position depending on the available residual energy. This prevents damage and accelerates a machine restart.
Baumüller offers a wide range of system solutions for the injection molding industry. The best choice of system depends primarily on the product manufactured by the machine and thus on the machine configuration. The number of axes to be electrified also plays an important role.
The use of ProSimulation also enables efficient drive dimensioning, shortened commissioning times, and improved service quality for the topologies mentioned above. Simultaneous engineering allows development times to be reduced and acquisition and life cycle costs to be lowered.
Injection molding is a method to obtain molded products by injecting plastic materials molten by heat into a mold, and then cooling and solidifying them. The method is used for mass production of products with complicated shapes and plays a large part in plastic processing. Injection molding for medical devices can be performed by using many sorts of materials such as metals, confections, and most commonly thermoplastic and thermosetting polymers.
The controller function “PWM frequency switching” is also useful for the injection process. It is used during the pressure or torque holding process at low speeds and extends the service life of the IGBT units. Further advantages are reduced IGBT losses and an extended torque or pressure holding duration. Shifting the standard pulse width modulation down from 4 to 2 kHz allows the torque to be held longer.
The topic of digitalization is also an important catalyst for achieving climate targets. Networking allows the potential of the drive technology and thus of injection molding machines to be fully realized. State-of-the-art communication interfaces are particularly important in this regard. Ethernet-based fieldbuses, for example, enable vertical integration into the machine’s control architecture. b maXX servo drives can be used for all commonly used bus systems.
For servo-hydraulic machines with one electric axis, a powerful mono unit is used in combination with a compact and dynamic servo motor.
For many years now, Baumüller has placed an increased focus on the development of energy-efficient drive concepts for the injection molding industry. The efficient use of resources has always been an important issue at Baumüller. This is reflected not only in pioneering work in the field of direct drive technology, but also in the development of the first fully electric injection molding machine in Europe. This was implemented at the end of the 90s with drive technology from Baumüller. At that time, servo drives that were interconnected via a common DC link were already in use, allowing highly energy-efficient operation.
Hybrid or fully electric machines are also used, for example, to produce high-voltage components of electrical connection technology and also complex plastic parts for interiors or exteriors for the automotive industry. Such solutions are of critical importance for e-mobility. Replacing heavy, metallic components like steel with plastic is important for lightweight construction. It makes it possible to increase the ranges of electric vehicles. This is also an important contribution to climate protection.
The module system combined with a mono unit in a DC link system is useful, for example, for the electrification of a few axes in combination with a high-performance drive axis. The starting point is often an already implemented servo-hydraulic drive, which is supplemented by additional electric axes. In this case, the large, powerful mono unit is linked directly to the module system via intelligent connection technology. This saves space in the control cabinet and is easy to implement, as both unit types use the same firmware. The degree of electrification of servo-hydraulic machines can thus be increased in an economic way thanks to the limited engineering work required and the elimination of a separate power feed.
In larger injection molding machines, two gantry axes are often employed to execute the movement of the injection axes. This allows the force to be divided between two axes. If one axis fails and the other continues to move, the injection axis will tilt. This can cause mechanical damage, bringing high repair costs and production losses in its wake. The “gantry function with synchronous error response” prevents tilting. Even if a fault occurs, both axes always act synchronously, i.e. they execute identical movements simultaneously. This happens automatically after an error is detected and with no time delay. As soon as the error has been eliminated, the axes can resume gantry operation. This fully excludes the possibility of mechanical damage.
In addition to supplying power to the power modules, the use of a regenerative feed unit also enables the sinusoidal feedback of excess braking energy into the mains. This regenerative system thereby makes an additional contribution to reducing energy consumption.
Module systems with a feed / regenerative feedback unit is the ideal solution for fully electric injection molding machines. The reason for this is the little space it requires in the control cabinet. In addition, the system benefits from high power density, flexible expandability, precise control, and high overload capability. The high-performance power units are available with air, water and cold plate cooling types. An integrated drive connect system allows individual modules to be easily removed or added without disconnecting the drive system. Machine manufacturers thus benefit from low installation costs and short commissioning and service times.
Protecting the machine operator is the top priority. The machine is therefore monitored with the aid of drive-integrated safety functions. In the event of danger, the controller allows the machine to be shut down and switched off in a controlled way. In addition to the available STO function, there is also a Safe Limited Speed (SLS) function, for example, which enables the speed to be safely limited. These and other safety functions can be controlled by way of the hardware wiring or a safe protocol of the fieldbus (FSoE = Fail Safe over EtherCAT).
Processing and reusing plastics while reducing the use of resources is a sustainable solution, yet it also poses a number of challenges. In this article, you will learn how energy-efficient, precise and dynamic automation solutions can help you to reduce the consumption of energy and materials.
Thanks to its scalability, the compact drive system with multiple drives can be optimally adapted to the power requirements of the injection molding machine. Moreover, it is no longer necessary to draw the short-term peak power required for individual drives from the mains. Instead, the energy can be distributed within the DC link system. This ultimately improves the energy efficiency of the entire system. Thanks to the reduction in the amount of power drawn from the mains, feed units can be made with smaller dimensions. Minimizing thermal power loss, e.g. by eliminating or downsizing brake resistors, enables an optimal design of the cooling units. It also saves space and reduces the costs for the control cabinet and the feed unit.
Gilero provides a range of manufacturing services, including plastic injection molding and injection mold tool building. We focus solely on the medical device and drug delivery markets. Our medical injection molding facilities follow strict design protocols and process controls to ensure that all products meet the required specifications. Depending on client needs and product requirements, we can offer manual or fully automated production lines for molding and assembly.
Plastic injection molding is widely used in the medical device industry. Plastics are often used alongside the injection molding process to produce prototypes and full-production units of medical devices and equipment components. As newer plastic materials and component designs are developed, injection molding medical devices has increasingly contributed to lower infectious disease rates, and lower medical costs.
Medical device injection molding also has many other advantages, such as compliance with industry standards and regulations. Engineering-grade plastics can be used in the process to create parts that enhance patient safety and comply with FDA (Food and Drug Administration) guidelines. There is flexibility with injection molding, as the parts can be fully customizable to fit the user. The ability to fulfill high-volume orders with high accuracy and precision is also an advantage of injection molding medical devices. In addition, injection molding is a cost-effective manufacturing method. With automation technology and energy-efficient equipment, we further reduce our labor and utility costs.
If the encoder fails during the process of closing the injection mold, major damage may occur to the cost-intensive closing tool of the injection molding machine as a result of the uncontrolled movement of the closing mechanism. Depending on the specific damage, this can result in a prolonged and expensive production downtime. The patent-pending “error response to encoder failure” function was developed to solve this very problem. The controller firmware in the servo converters checks the status of the encoder every microsecond.
The result is a broad range of servo converters combined with regenerative systems, intelligent software and simulation solutions, as well as synchronous technology and direct drive technology. The products of drive technology make an important contribution to the energy-efficient and precise production of even highly complex plastic parts.
For large power requirements, several feed units can be connected in parallel. This solution is suitable for powerful injection molding machines.
In addition, numerous controller functionalities help to ensure that the injection molding machine delivers perfect results around the clock. High machine availability, better repeat accuracy during production, and a reduced use of materials thanks to shorter start-up times after tooling are solid advantages.
In the event of an encoder failure, it automatically switches from closed-loop control to V/f operation. Depending on the parameterization of the controller, the system is then immediately braked and brought to a standstill. At the same time, information can be sent to the control unit via the fieldbus. This ensures that the machine shuts down in a controlled and synchronized manner. This way, the closing process is completed with no damage and the machine comes to a standstill.
Various simulation tools are used for the efficient design of the individual drive components. This saves time, costs, and energy. This is because the software affords an optimum design of the drive components and the faster commissioning and drive optimization of the injection molding machine, among other benefits.
Baumüller offers a broad portfolio of solutions for the electrification of axes in order to implement hybrid and fully electric injection molding machines. High-speed machines for the production of plastic packaging, for example, are equipped with compact, energy-efficient, and powerful module systems in combination with dynamic servo motors. The precision of the electric drive technology and the short restart times after tooling help to reduce material consumption. This compact drive technology is also used for the manufacture of medical devices under cleanroom conditions. The drive concept also allows the feedback of excess energy.
Processing and reusing plastics while reducing the use of resources is a sustainable solution, yet it also poses a number of challenges. In this article, you will learn how energy-efficient, precise and dynamic automation solutions can help you to reduce the consumption of energy and materials.
Thanks to servo converter intelligence, it is still possible to work with extreme precision in the execution of highly dynamic movements and also to respond extremely quickly to error messages. In addition, the integrated programmable softdrivePLC allows easy links between digital I/Os, technology functions or data analyses to be implemented directly in the drive. One example is the servo hydraulics technology function, which enables highly dynamic and intelligent pressure and flow rate control. The advantages of drive-integrated intelligence and fast control can also be applied to electromechanical axes, such as gantry functions.
There are many diverse types of materials that can be used in injection molding medical devices. Some useful and commonly used materials include:
Building on this foundation, Baumüller continuously developed and expanded its solution portfolio for energy-efficient synchronous drive technology.
All three drive solutions are both compact and scalable and allow high power density. Moreover, thanks to the identical controller firmware, the expenses for project planning, maintenance, and even service are reduced during the life cycle of the machine.
Plastic is used in great quantities worldwide. More than 300 million tons of this material are consumed every year. According to the findings of a recent analysis conducted by McKinsey & Company, this figure could potentially triple by 2050. However, virgin material is becoming increasingly less abundant. More and more plastics processors are rethinking their approach and switching to recycled material. The proportion of “recyclates” is expected to rise to around 50 percent by 2050.
The flexible servo converter portfolio enables the combination of the required drive axes with a feed or regenerative feedback unit. In addition, it is also possible to combine the drive axes of the module system with a mono unit without a separate feed unit if, for example, a very powerful drive axis is required. In this case, the mono unit acts both as a feed unit for the axis group and as a servo drive. The respective systems work together in a common DC link, enabling energy-efficient operation.
GETTING A QUOTE WITH LK-MOULD IS FREE AND SIMPLE.
FIND MORE OF OUR SERVICES:
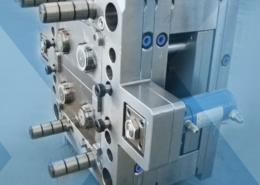
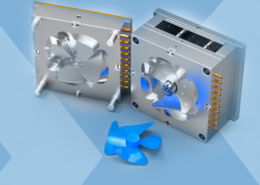
Plastic Molding
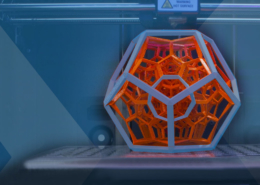
Rapid Prototyping
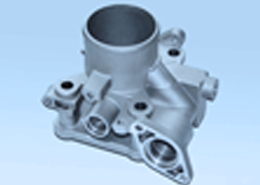
Pressure Die Casting
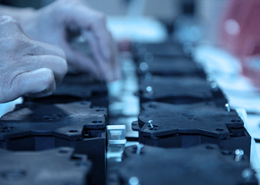
Parts Assembly
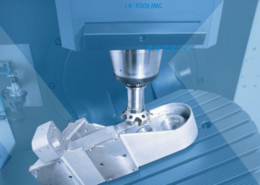