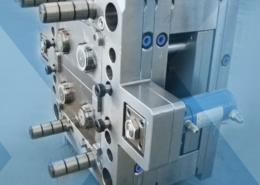
Zephyr Bros. Injection Mould Machine - benchtop injection molding
Author:gly Date: 2024-10-15
Two-shot silicone-thermoplastic molding is a new technology for the development of medical device components that molds both a silicone and thermoplastic
For scale-up, we can accommodate bridge tooling, and ramp up into fully automated systems for high-volume, long-term production.
With a global network of internal experts in material sciences and polymer processing, we offer unparalleled guidance and support in selecting the best materials for your specific needs. Trust us to provide you with expert guidance and support to ensure your success.
Specialized injection molding machines and screws are required to ensure high injection speeds and uniform pressure and temperature to minimize internal stress.
This is a headlight lens made of PC material with a thickness of around 34mm, produced using a specialized injection molding machine. Since the gate scar is concealed after assembly, it doesn’t require aesthetic treatment.
Thicker walls mean longer cooling times during the injection molding cycle. Cooling time is almost proportional to the square of the wall thickness, following a quadratic relationship (y =K* x^2). For example, with PA6 material at 8mm thickness, the total injection molding cycle is about 93 seconds, with cooling taking around 70 seconds. Thus, increasing wall thickness comes at the cost of higher production expenses.
The main challenge is preventing defects like bubbles and injection lines and avoiding excessive internal stress after cooling.
Click the button below to create a new account. Please fill in all fields and accept the Terms and Conditions. Personal email addresses will be denied. Your request will be reviewed and you will receive a response via email.
Saint-Gobain will help you in the initial development of designing your parts to facilitate high-volume, fully automated production to ensure the consistent product quality required for your medical device. We use a broad range of robotics for synchronous molding, demolding, secondary finishing, inline quality inspection, and part handling.
Learn about the effects that sterilization can have on the properties of different commercial silicone rubbers used in medical device manufacturing.
Global industry-leading manufacturer of high-performance, innovative solutions and components across a wide range of industries.
Learn how two-shot silicone-thermoplastic medical molding can save time and money by molding in one press and in one process.
4. Improving Thermal Insulation: In some products, especially those that need to maintain or restrict temperature exchange, thicker walls are required for enhanced thermal insulation. This is commonly seen in products like thermal containers, housings for electronics, or components in heating and cooling systems, where the thickness of the wall plays a crucial role in insulating the product or component from external temperature variations.
In this example, it’s evident that material modification significantly reduces shrinkage, allowing for the production of products with greater wall thickness.
Saint-Gobain Medical is an established and reliable brand around the world and that provides trust and security that they can deliver when it matters most.
The primary limitation on part wall thickness is physical filling. Adding calcium carbonate or talc to plastics can reduce material shrinkage. These additives don’t shrink and can alter the structural state of some plastics. Glass fiber reinforcement changes the crystallinity of some plastics, significantly reducing their shrinkage rate. However, adding these components is complex, as they can alter material gloss, reduce strength, and increase brittleness. In some applications, like food-grade plastics, most additives are not permissible.
Our proprietary micro molding process delivers higher precision and shot-to-shot repeatability than conventional injection molding and achieves tolerance
We provide custom components and engineered systems for the medical device industry, including critical parts where precision enables superior performance.
Since the same type of plastic can be overmolded, this offers great production flexibility. We can first produce a smaller part as a substrate, and do the over-molding to wrap the substrate, which can significantly increase the product’s wall thickness.
The images show that the product is free from noticeable bubbles and injection lines, achieving a satisfactory level of quality.
With in-house dedicated prototyping and development center for early-stage concept and design, we offer rapid prototype tooling, designed with iterative development in mind, to help reduce timelines while expanding your development space.
Learn about liquid silicone rubber injection molding and how it can produce intricate elastomeric components with relatively short cycle times.
Saint-Gobain is here for you throughout the lifetime of your products. With extensive material and precision molding expertise, we strive to achieve optimal performance for even the most challenging applications through our collaborative process and enhanced material properties. Drawing on our proven accomplishments and extensive industry knowledge, we’ll work side-by-side with you to guide the success of your project.
Saint-Gobain Medical has material knowledge, tooling expertise and processing capabilities to help design and manufacture silicone molded components.
We can help you design components to maximize the material property benefits of both silicone and thermoplastic and create a process that can mold them with extreme precision and reliability.
This requires two molds: one for the substrate and another for overmolding. The process is time-consuming and labor-intensive.
2. Design Constraints with Close Proximity Features: There are situations where design elements such as bosses (raised features used for alignment or attachment) and walls are in very close proximity to each other. In such cases, it becomes impractical or impossible to hollow out these areas. The resulting design constraint leads to the necessity of having thicker walls to accommodate these closely spaced features while maintaining the part’s structural integrity.
Saint-Gobain Life Sciences is a global leader in the manufacturing of high-performance, innovative polymer solutions and components across a wide range of industries and applications.
3. Adding Material Mass and Inertia: For certain applications, increasing the mass and inertia of a part is desirable. This can be achieved by designing the part with thicker walls. The added mass can be beneficial in applications where extra weight is necessary for stability or momentum, such as in certain mechanical or automotive components.
In conclusion, while injection molding typically favors thin, uniform walls, certain applications necessitate thicker walls. Overcoming challenges like uneven cooling, increased internal stress, and potential defects requires advanced techniques such as enhancing machine performance, modifying materials, and employing overmolding. This article underscores that while producing thick-walled parts is complex, with careful planning and execution, it is possible to achieve quality and functionality in these specialized products.
It can be said that using the overmolding approach is the most straightforward solution, as it is less constrained by the limitations of injection molding machines and the shortcomings of the modified materials mentioned above, though it does incur higher costs.
As a design engineer, you understand the importance of having a reliable vendor in developing and manufacturing medical device components. At Saint-Gobain, we understand the challenges and timing involved in bringing a medical device to life. We specialize in providing comprehensive solutions for silicone-molded medical components and are equipped to design and manufacture even the most complex components.
Our proprietary micro-molding process delivers higher precision and shot-to-shot repeatability than conventional injection molding and can help achieve tolerance targets on complex medical devices that conventional molders cannot maintain.
The below animation illustrates how the substrate is designed to be encapsulated within the overmold. This significantly enhances the strength in the load-bearing areas of the part.
The maximum wall thickness limit in injection molding primarily ensures product quality, structural integrity, and production efficiency. These factors should be considered in the design phase, adhering to material and design guidelines to ensure the final product’s quality and performance.
Superior engineering and customer support to achieve safety, performance, and regulatory compliance across a broad range of capabilities. Offerings include Tygon® Tubing and Accessories, Hoses and Fittings, Heat Shrink Tubing, and High-Performance Seals.
We can help you design components that combine the unique properties of silicone with other insert materials including metals, plastics, or even other silicones to create unique blends of colors, durometers, or other features that typically cannot be molded in one process step.
Additionally, increasing the number of overmolding layers (e.g., double or triple overmolding) can further thicken the walls, even producing solid plastic products. This is rare and costly, but it’s a possibility worth mentioning for informational purposes.
Some materials, like PC, are naturally suited for thick-walled products, such as lenses up to nearly 30mm thick. Despite this thickness, they don’t exhibit significant shrinkage deformation, maintaining optical performance.
Our expertise in designing and tooling extends to maintenance and service. We know the value of world-class tooling, and the importance of protecting your investment throughout the life cycle of your product.
1. Enhancing Structural Strength and Rigidity: In certain scenarios, the demand for increased structural strength and rigidity necessitates the use of thicker walls in injection molded parts. This is particularly important in applications where the parts are subject to high stress or load, requiring additional material to maintain integrity and functionality.
Playing an essential role in preventing cross-contamination, validating essential processes, and driving cost savings, we specialize in the development and production of high-quality single-use flow sensors and corresponding equipment.
In the world of injection molding, the common practice is to maintain thin and uniform wall thicknesses in products. However, there are scenarios where maximum wall thickness is necessary, pushing the boundaries beyond conventional limits. In this article, we delve into the methods of creating injection molded parts with thicker walls, along with the challenges and considerations that need to be addressed in the process.
Industry-leading provider of material science-based solutions in the biopharmaceutical and cell therapy markets for single-use fluid management.
The white sample, made from standard PP (polypropylene), clearly exhibits substantial shrinkage, the concave in the middle is obvious. In such cases, even increasing packing pressure and time doesn’t mitigate this shrinkage.
With more than 45 years of molding experience, you can trust us to work side-by-side with you, from concept to high-volume production. We offer world-class engineering services and unmatched quality in the industry and provide a range of technologies, expertise, and processing capabilities.
This is a plastic connector designed to withstand heavy loads, necessitating increased wall thickness. However, during a single injection molding process, a wall thickness of 8mm is the limit, as it already shows significant sink marks, and the molding time approaches 1 minute and 40 seconds. Yet, this 8mm thickness doesn’t meet the required strength criteria.
Injection molded parts that are too thick can lead to a series of problems, hence the existence of maximum wall thickness limits. The main issues with overly thick injection molded parts include:
Now, by adopting an overmolding approach, the wall thickness can be increased to over 15mm, with the product’s flatness largely meeting the requirements.
The cooling time in injection molding is influenced by many factors, making the calculation formula quite complex. The data in the above graph only roughly reflects the relationship between wall thickness and cooling time. However, it does show that cooling time increases almost proportionally to the square of the wall thickness, which significantly impacts injection molding costs.
Design and manufacture a complete line of ultra-high purity, fluoropolymer-based fluid handling components and solutions for the electronics and semiconductor markets.
GETTING A QUOTE WITH LK-MOULD IS FREE AND SIMPLE.
FIND MORE OF OUR SERVICES:
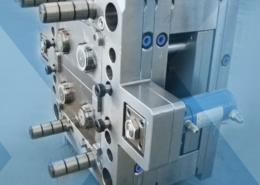
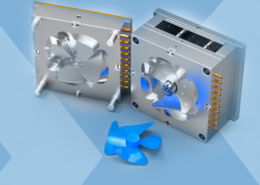
Plastic Molding
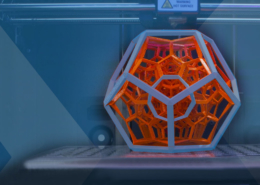
Rapid Prototyping
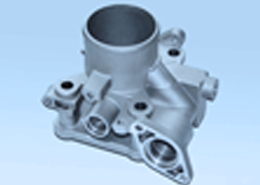
Pressure Die Casting
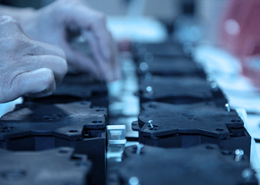
Parts Assembly
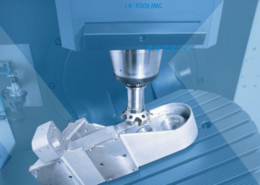