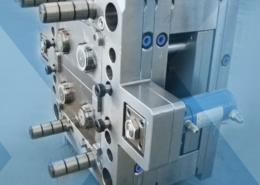
Zephyr Bros. Injection Mould Machine - injection mold press
Author:gly Date: 2024-10-15
Large-part injection molding in China is designed to satisfy unique applications. Whether they are plastic decking or electronic casings, large-format items can be carefully made to accentuate every feature. Every intricate design can be emphasized in its production, ensuring your specifications are met. This technique makes certain of the quality and performance of every product.
The electronic industry uses this type of injection molding for the mass production of large-part electronic components. These could be battery encasings, generator shells, computer monitor bezels, and more. Plastic is the ideal material since it seals water off and resists UV rays. These two qualities are essential to make electronic products safer to use.
Large-part injection molding in China is a specialized field in plastic manufacturing. It offers numerous advantages in producing large-scale plastic components. It is an innovative solution for any plastic item, from plastic pallets to car bumpers. As a sought-after service for making sizeable products, it is an ideal choice for businesses across various industries looking for reliable production capabilities.
Large-part injection molding is a prominent technique for making high-quality large-sized items. It is a reliable method in plastic manufacturing, meeting the many unique demands of various industries. With many advantages tied up to its name, it is one of the groundbreaking processes in the industry.
The prototype injection moulding process begins with the creation of a detailed design of the product. This design is then used to create a mould, which is typically made from metals like steel or aluminum. The chosen material, often a type of plastic, is then heated until it becomes molten. This molten material is injected into the mould under high pressure.Once the material has been injected into the mould, it is allowed to cool and solidify. After the material has fully solidified, the mould is opened, and the prototype is removed. This process can be repeated multiple times, allowing for the production of multiple prototypes in a relatively short period of time.
At Richfields Corporation, you can experience exceptional services for any large plastic components. Our large-part injection molding in China is one of the best in the industry. With over two decades in the field, we take pride in our accumulated knowledge and experience in plastic manufacturing.
ACIS®, Autodesk Inventor®, CATIA® V5,Creo™ Parametric, IGES, Parasolid®, Pro/ENGINEER®,Siemens PLM Software’s NX™, SolidEdge®, SolidWorks®, STEP
If you’re in need of high-quality prototype injection molding services, consider reaching out to FOWMould. With years of experience in the industry, we offer reliable and efficient prototype injection moulding services that can help bring your product ideas to life.
China sits at the center of the global plastic manufacturing industry. It is only expected that their companies have the best tools. When you work with them, your product is made with advanced technology. These pieces of equipment are developed specifically to make processes more efficient without sacrificing quality. With their high technology, you can easily meet stringent standards.
When working with this specialized method, it is only right to partner with the best team. Our experts at Richfields Corporation are highly knowledgeable about large-part injection molding in China. Whether you are looking to satisfy automotive or consumer goods specifications, you are thoroughly guided by our professionals. Equipped with advanced technologies and powerful machinery, your product can easily take shape with us.
Design Complexity: If your design is complex with intricate details, methods like Stereolithography (SLA) or Selective Laser Sintering (SLS) may be more suitable due to their high precision. For simpler designs, Fused Deposition Modeling (FDM) or CNC machining might be sufficient.Material Requirements: The choice of prototyping method can also depend on the material choice you intend to use. For example, if you plan to use thermoplastics, FDM or prototype injection moulding might be the best choice. For metal prototypes, you might opt for CNC machining or Direct Metal Laser Sintering (DMLS).Quantity: If you need a large number of prototypes, methods like rapid injection moulding or FDM can be more cost-effective due to their scalability. For a small number of highly detailed prototypes, SLA or SLS might be more suitable.Budget and Time Constraints: Faster methods like FDM or rapid injection moulding can be more suitable if you’re working under tight deadlines. However, if budget is a concern, you might need to balance the speed of production with the costs involved.End-Use: If the prototype is for functional testing or end-use, you might need a method that produces durable and functional parts, like prototype injection moulding or CNC machining.
Plastic is a common material in automotive manufacturing. It is known to make car units lighter. Car parts like fenders, hoods, grills, paneling, and door covers are made from this process. These parts are made more efficient to meet the specific preferences of reputable car brands worldwide.
Crafting a sizeable plastic part requires more than one strategy. There are other ways to mold molten plastic into the ideal component. While molds and their designs are pivotal, how it is processed is also necessary. It is the same with large-part injection molding.
Prototype injection moulding is a manufacturing process that involves the use of injection moulds to create prototypes of a product. This process is often used in the early stages of product development to test the design, functionality, and feasibility of a product before it goes into mass production. The prototype injection moulding process involves injecting molten material, often plastic, into a mould which then cools and solidifies to form the desired shape. This method allows for a high degree of precision and is ideal for creating complex shapes and designs.
Large-part injection molding in China also uses hot-runner and cold-runner systems. These two methods are basic techniques in plastic manufacturing, in which both use molten material. The difference is the temperature needed to transfer the viscous polymer. The former method requires intense heated runners. The latter, however, does not need high temperatures to move the molten material.
Innovative solutions are not unfamiliar to large-part injection molding in China. Being the hub of world-class plastic manufacturers, your plastic products have access to many resources. From the best machinery and a diverse range of materials to signature techniques and unprecedented expertise, you are extensively guided throughout the production.
In the realm of product development, prototype injection moulding serves as a critical tool for testing and validating product designs. It provides a cost-efficient way to identify potential design flaws or issues early in the development process, thereby saving time, resources, and reducing the risk of costly errors in the later stages of production.Prototype injection moulding allows for the creation of a physical model that can be used for various types of testing, including functional, durability, and user experience tests. By testing a physical prototype, companies can gain valuable insights into how the final product will perform and interact in its intended environment. This process also allows for any necessary design modifications to be made before the product goes into mass production, ensuring a higher quality final product.
You can choose structural foam molding for your large-part injection molding in China. It involves the combination of a polymer and inert physical gas or a chemical agent, which are thermoset polymers and nitrogen gas. This technique produces a sponge or honeycomb-like core with high-density outer skin. With this texture incorporated into the product, they are lighter than any solid components.
Selective Laser Sintering (SLS): SLS is a type of 3D printing technology that uses a laser to sinter powdered material, typically nylon or polyamide, forming a solid structure. This method is beneficial for creating complex and detailed prototypes that require high durability. SLS does not require any support structures, which makes it ideal for designs with intricate geometries.Stereolithography (SLA): SLA is another form of 3D printing that uses a laser to cure a photosensitive resin layer by layer. SLA is known for its high resolution and accuracy, making it suitable for prototypes that require fine details and tooling. However, SLA prototypes may not be as durable as those created with other methods.Fused Deposition Modeling (FDM): FDM is a common 3D printing method that uses a continuous filament of thermoplastic material. The material is fed through a heated nozzle, which melts it and deposits it layer by layer to build the prototype. FDM is a cost-effective method that can use a wide range of materials, but it may not offer the same level of detail as SLS or SLA.CNC Machining: While not a form of 3D printing, traditional CNC machining is another method used for prototyping. It involves the use of computer-controlled machines to remove material from a solid block to create the desired shape. CNC machining can work with a wide range of materials and is known for its high precision, which can help reduce tooling costs.Rapid Injection Moulding: This is a method that uses aluminum molds, allowing for faster and more cost-effective production of prototypes compared to traditional injection molding. It’s ideal for low-volume production runs.Each of these methods has its own strengths and is best suited to different types of projects, depending on factors such as the complexity of the design, the required durability of the prototype, the materials being used, and the project’s budget and timeline.
Prototype injection moulding is utilized across a wide range of industries due to its versatility and efficiency. In the automotive industry, it is used to create prototypes of parts such as dashboards, door handles, and engine components. The medical industry also heavily relies on this process for the development of medical devices and equipment, such as surgical tools and diagnostic devices.Other industries that commonly use prototype injection moulding include electronics, where it is used to create prototypes of components for devices like smartphones and computers, and the aerospace industry, where it is used in the development of parts for aircraft and spacecraft. The consumer goods industry also benefits from this process, using it to create prototypes for products ranging from kitchen appliances to toys.
Discover the advantages of large-part injection molding with Richfields Corporation in China. Our state-of-the-art facilities and experienced team ensure the highest quality and precision for your large-scale projects. Contact us today to learn more about our services and how we can meet your specific molding needs. Let's bring your vision to life with expert craftsmanship and reliable solutions!
Various pieces of sports equipment are manufactured from large-part injection molding in China. It can mostly be seen in gears needed for water sports, such as kayaks, canoes, surfboards, and rowing shells. A combination of polyethylene, high-impact ABS, and acrylic are typically involved in making these sports materials.
Insert molding requires the addition of inserts in the molding process. These inserts are metal material and are placed into position in the cavity before injecting the molten plastic. When the general process is done, the metal insert is not removed. Rather, it becomes a part of the plastic component. It is the ideal process in creating strong, durable, and lightweight plastic components.
Large-part injection molding in China is a cost-effective method. It is designed to meet every need of the product. That is why it is often done with vigorously developed machinery. With its equipment, it can take care of most of the steps required for a high-stand plastic component. It is a great investment and reduces long-term labor costs.
Large part injection molds are significantly focused areas in plastic manufacturing. Due to the high volume of materials needed and the use of robust equipment, there are many at stake in its production.
Careful consideration is important to create the ideal plastic item, whether it is used for automotive or consumer goods industries, understanding various methods to make large plastic parts is important.
Large-part injection molding is specifically developed to produce massive-sized components. It involves injecting molten plastic into a mold reflecting your ideal design. Robust machinery is required for this technique. Pieces of equipment must withstand the great tonnage or weight of the material. Using and handling these resources makes it a specialized service in manufacturing.
Prototype injection moulding is a versatile and efficient method for creating detailed and functional prototypes. It plays a crucial role in product development, allowing for thorough testing and evaluation before a product goes into full-scale production.
The gas-assisted technique is a low-pressure process. It combines conventional injection molding and the application of pressurized inert gas. The molten material does not completely fill up the size of the mold. The empty space is used to allow the gas to manipulate the material from the inside. Through strategically placed gas channels, the molten plastic is shaped by the gas to reach the mold’s walls.
Plastic is a durable material since it withstands elements from corrosion to impact. It is the perfect material to make appliances including washing machine bodies, fridge interior and outer shells, air conditioning casings, and more. With large-part injection molding in China, your lifestyle is further enhanced with convenience.
Large-part injection molding in China offers flexibility and precision. It offers high-quality plastic parts for every purpose across many industries in global markets.
GETTING A QUOTE WITH LK-MOULD IS FREE AND SIMPLE.
FIND MORE OF OUR SERVICES:
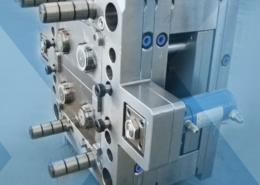
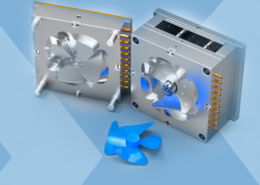
Plastic Molding
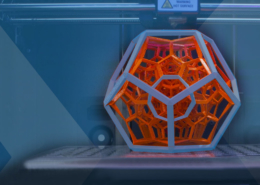
Rapid Prototyping
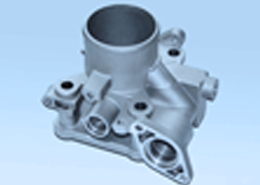
Pressure Die Casting
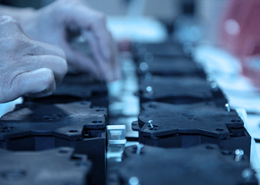
Parts Assembly
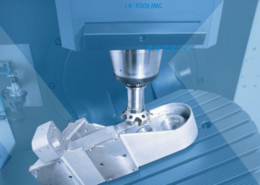