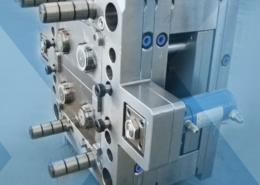
Exploring the World of Medical Device Plastic Molding
Author:gly Date: 2024-06-08
Medical device plastic molding stands at the intersection of innovation, precision, and patient care. This article aims to delve into the intricacies of medical device plastic molding, shedding light on its importance, applications, challenges, and future prospects.
Introduction
Medical device plastic molding represents a critical aspect of modern healthcare, facilitating the production of a wide range of devices and components used in medical diagnostics, treatment, and patient care. From syringes and catheters to implantable devices and surgical instruments, plastic molding plays a vital role in shaping the landscape of medical technology. Its ability to produce complex, high-precision parts with biocompatible materials has revolutionized the medical industry, enabling advancements in patient care, cost-effectiveness, and device functionality.
Importance in Healthcare
The importance of medical device plastic molding in healthcare cannot be overstated. It serves as the backbone of medical device manufacturing, providing the necessary components and tools for diagnosing, treating, and managing various medical conditions.
Precision and Customization
Medical device plastic molding enables the production of intricate components with tight tolerances and complex geometries, allowing for precise fit and functionality. This level of precision is crucial for devices such as prosthetics, orthopedic implants, and dental restorations, where even minor discrepancies can impact patient outcomes.
Biocompatibility and Safety
Biocompatibility is paramount in medical device manufacturing to ensure compatibility with biological systems and minimize the risk of adverse reactions or infections. Medical-grade plastics used in molding processes undergo rigorous testing to meet regulatory standards, ensuring the safety and efficacy of the final products. From disposable syringes to implantable devices, maintaining biocompatibility is essential for patient safety and well-being.
Cost-Effectiveness and Scalability
Plastic molding offers a cost-effective and scalable manufacturing solution for medical devices, allowing for high-volume production at relatively low unit costs. This scalability is particularly advantageous for disposable and single-use devices, where mass production is necessary to meet the demands of healthcare facilities while keeping costs manageable.
Challenges and Considerations
Despite its numerous benefits, medical device plastic molding poses unique challenges and considerations that must be addressed to ensure quality, safety, and regulatory compliance.
Material Selection and Compatibility
Choosing the right material for medical device molding is critical, considering factors such as biocompatibility, sterilization compatibility, and mechanical properties. Manufacturers must carefully evaluate the performance characteristics of various plastics and elastomers to ensure they meet the specific requirements of each application while adhering to regulatory guidelines.
Design Complexity and Tooling
The design complexity of medical devices often necessitates intricate molds and tooling, which can increase production costs and lead times. Balancing design requirements with manufacturing feasibility is essential to optimize part quality, minimize defects, and ensure efficient production processes.
Regulatory Compliance and Quality Assurance
Medical device manufacturing is subject to stringent regulatory requirements, including ISO standards, FDA regulations, and international quality management systems. Ensuring compliance with these standards requires robust quality assurance processes, documentation, and traceability throughout the manufacturing lifecycle.
Applications in Healthcare
The applications of medical device plastic molding are diverse and encompass a wide range of medical specialties and disciplines.
Diagnostic Devices
Medical diagnostic devices, such as blood glucose monitors, imaging equipment, and diagnostic assays, rely on precision-molded components to deliver accurate and reliable results. From microfluidic channels to sensor housings, plastic molding enables the fabrication of complex geometries and functional features essential for diagnostic accuracy.
Surgical Instruments
Surgical instruments play a critical role in modern healthcare, facilitating minimally invasive procedures, precision surgeries, and patient care. Medical device plastic molding allows for the production of lightweight, ergonomic instruments with intricate features, enhancing surgeon comfort, maneuverability, and procedural efficiency.
Implantable Devices
Implantable medical devices, including pacemakers, orthopedic implants, and drug delivery systems, benefit from the biocompatibility and durability of plastic molding materials. By precisely shaping biocompatible polymers and ceramics into implantable components, manufacturers can create devices that integrate seamlessly with the body, promoting healing and improving patient outcomes.
Future Directions and Innovations
Looking ahead, the future of medical device plastic molding is ripe with opportunities for innovation and advancement.
Advanced Materials and Technologies
The development of advanced materials, such as bioresorbable polymers, shape memory alloys, and nanocomposites, holds promise for the next generation of medical devices. These materials offer enhanced biocompatibility, mechanical properties, and drug delivery capabilities, paving the way for novel treatment modalities and implantable technologies.
Additive Manufacturing and 3D Printing
Additive manufacturing techniques, such as 3D printing, are revolutionizing medical device production by enabling rapid prototyping, customization, and on-demand manufacturing. From patient-specific implants to anatomical models for surgical planning, 3D printing offers unparalleled design freedom and manufacturing flexibility, opening new possibilities for personalized healthcare solutions.
Digital Twin and Smart Manufacturing
The integration of digital twin technology and smart manufacturing principles promises to streamline the medical device manufacturing process, from design optimization to production planning to quality control. By creating virtual replicas of the molding process and leveraging real-time data analytics, manufacturers can optimize process parameters, minimize defects, and ensure regulatory compliance, driving efficiency and innovation in healthcare.
Conclusion
In conclusion, medical device plastic molding plays a pivotal role in advancing healthcare by enabling the production of safe, effective, and innovative medical devices. Its importance in patient care, cost-effectiveness, and scalability cannot be overstated, making it a cornerstone of modern medical technology. As the healthcare landscape continues to evolve, embracing new materials, technologies, and manufacturing practices will be essential for driving innovation and meeting the evolving needs of patients and healthcare providers alike.
GETTING A QUOTE WITH LK-MOULD IS FREE AND SIMPLE.
FIND MORE OF OUR SERVICES:
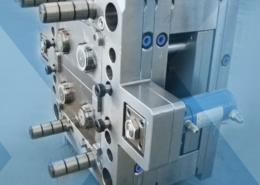
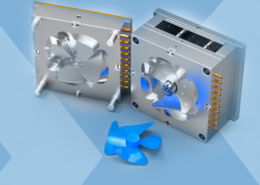
Plastic Molding
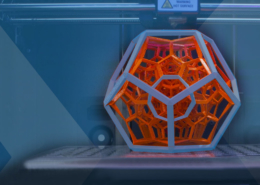
Rapid Prototyping
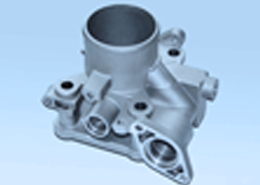
Pressure Die Casting
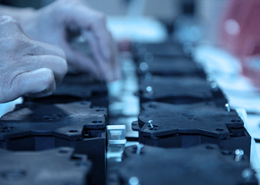
Parts Assembly
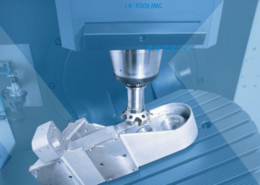