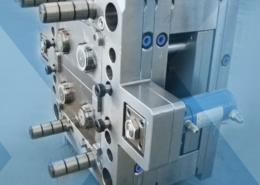
The Transformative Power of Medical Injection Molding
Author:gly Date: 2024-06-08
Medical injection molding stands as a cornerstone of modern healthcare, facilitating the production of intricate and high-performance medical devices that have revolutionized patient care and treatment outcomes. From surgical instruments and implantable devices to diagnostic equipment and drug delivery systems, the applications of medical injection molding are vast and diverse. This article delves into the realm of medical injection molding, exploring its significance, applications, challenges, and future prospects.
Unveiling the World of Medical Injection Molding
Medical injection molding encompasses the manufacturing process of producing precision-engineered plastic components used in various medical applications. It involves injecting molten thermoplastic materials into a mold cavity, where they solidify to form intricate and functional parts with exceptional precision and repeatability. This process enables the mass production of medical devices with complex geometries and tight tolerances, meeting the stringent regulatory requirements and performance standards of the healthcare industry.
Materials Selection and Biocompatibility
The choice of materials in medical injection molding is critical, considering the stringent biocompatibility and sterilization requirements of medical devices. Engineers must select medical-grade thermoplastics that are compatible with the intended use, ensuring patient safety and regulatory compliance. Materials such as polyethylene, polypropylene, polycarbonate, and various elastomers offer a balance of mechanical properties, chemical resistance, and biocompatibility, making them ideal for medical device applications.
Biocompatibility Testing
Before selecting a material for medical injection molding, thorough biocompatibility testing is essential to assess its compatibility with biological systems and potential risks to patient health. Regulatory bodies such as the FDA provide guidelines and standards for conducting biocompatibility tests, including cytotoxicity, sensitization, and irritation assessments, to ensure the safety and efficacy of medical devices.
Sterilization Compatibility
Medical devices manufactured through injection molding must withstand various sterilization methods, including steam autoclaving, ethylene oxide (EtO) sterilization, gamma irradiation, and hydrogen peroxide gas plasma. Material selection plays a crucial role in determining the compatibility of the device with these sterilization methods, ensuring that it maintains its structural integrity, functionality, and biocompatibility throughout its lifecycle.
Design for Manufacturing (DFM) Principles
Design for Manufacturing (DFM) principles are paramount in medical injection molding to optimize the manufacturability, functionality, and cost-effectiveness of medical devices. Collaborative efforts between design engineers, mold designers, and injection molding experts are essential to ensure that the design meets the requirements of both the end-user and the manufacturing process.
Complex Geometry and Micro-Molding
Medical devices often feature intricate geometries and micro-scale features that pose challenges in traditional manufacturing processes. Medical injection molding offers the capability to produce complex parts with high precision and repeatability, enabling the miniaturization of medical devices and the integration of multiple functionalities into a single component.
Mold Design Optimization
The design of the injection mold plays a crucial role in the success of medical injection molding processes. Factors such as gate location, cooling channel layout, and parting line design must be carefully optimized to minimize defects, improve cycle times, and enhance part quality. Advanced mold technologies, such as hot runners, multi-cavity molds, and conformal cooling, enable the production of high-quality medical components with reduced lead times and production costs.
Applications in Medical Devices and Healthcare
Medical injection molding finds applications across a wide spectrum of medical devices and healthcare products, ranging from disposable consumables to implantable devices and surgical instruments. Its versatility, precision, and scalability have paved the way for innovations in patient care, medical diagnostics, and therapeutic treatments.
Disposable Medical Devices
Disposable medical devices, such as syringes, catheters, and IV tubing sets, are commonly manufactured using injection molding due to its cost-effectiveness, high throughput, and design flexibility. Single-use disposable devices help prevent cross-contamination, reduce the risk of infection, and improve patient safety in clinical settings.
Implantable Devices
Implantable medical devices, including orthopedic implants, cardiovascular stents, and dental prosthetics, benefit from the precision and biocompatibility offered by medical injection molding. Advanced materials and manufacturing techniques enable the production of custom-designed implants tailored to individual patient anatomy, enhancing implant integration, longevity, and patient outcomes.
Drug Delivery Systems
Drug delivery systems, such as insulin pens, inhalers, and transdermal patches, rely on injection-molded components to ensure accurate dosing, ease of administration, and patient compliance. The precise control of component dimensions, surface finishes, and drug compatibility achieved through medical injection molding contributes to the effectiveness and reliability of drug delivery devices.
Challenges and Future Directions
Despite its numerous benefits, medical injection molding faces challenges related to material innovation, process optimization, and regulatory compliance. Addressing these challenges and embracing emerging technologies will be crucial in unlocking new opportunities and advancing the field of medical device manufacturing.
Material Innovation and Sustainability
The development of novel materials with enhanced biocompatibility, mechanical properties, and sustainability profiles is essential to meet the evolving needs of the healthcare industry. Bio-based polymers, recyclable thermoplastics, and biodegradable materials offer promising alternatives to traditional plastics, reducing environmental impact and supporting circular economy initiatives.
Additive Manufacturing Integration
The integration of additive manufacturing technologies, such as 3D printing, with injection molding processes holds potential for accelerating product development cycles, enabling on-demand manufacturing, and customizing medical devices to individual patient needs. Hybrid approaches combining the design flexibility of additive manufacturing with the scalability and efficiency of injection molding offer new avenues for innovation and personalization in healthcare.
Conclusion
In conclusion, medical injection molding plays a pivotal role in shaping the landscape of modern healthcare, enabling the production of advanced medical devices that improve patient outcomes and quality of life. By leveraging materials science, advanced manufacturing techniques, and collaborative innovation, medical injection molding continues to drive progress in medical device manufacturing, paving the way for transformative advancements in patient care and treatment modalities. As the healthcare industry evolves and technology advances, embracing the challenges and opportunities presented by medical injection molding will be essential in realizing the full potential of medical device innovation and improving global healthcare delivery.
GETTING A QUOTE WITH LK-MOULD IS FREE AND SIMPLE.
FIND MORE OF OUR SERVICES:
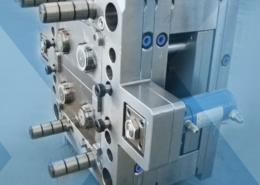
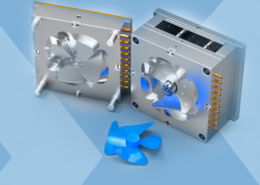
Plastic Molding
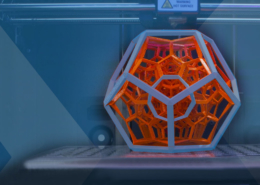
Rapid Prototyping
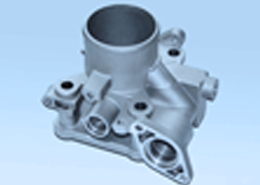
Pressure Die Casting
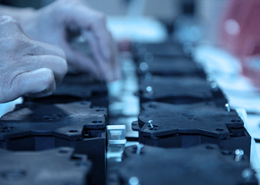
Parts Assembly
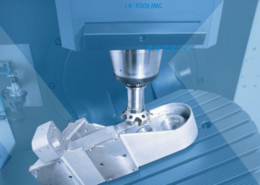