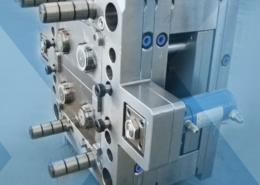
Unveiling the Potential: Mini Injection Molding
Author:gly Date: 2024-06-08
Introduction:
Mini injection molding stands at the forefront of innovation, revolutionizing the manufacturing landscape with its compact yet powerful capabilities. In this article, we embark on a journey to explore the realm of mini injection molding, delving into its origins, applications, and transformative potential. From intricate components to personalized products, mini injection molding unveils a world of possibilities, captivating manufacturers, entrepreneurs, and enthusiasts alike.
Background:
Injection molding, a manufacturing process dating back to the 19th century, has evolved into a cornerstone of modern production, enabling the mass production of intricate components with unparalleled precision and efficiency. Traditionally associated with large-scale manufacturing, the emergence of mini injection molding introduces a paradigm shift, catering to the growing demand for smaller, more intricate components across various industries. Leveraging advancements in materials, technology, and design, mini injection molding empowers manufacturers to explore new frontiers of innovation and customization.
Compact Design and Versatility
The compact design of mini injection molding machines heralds a new era of versatility and accessibility in manufacturing. Unlike their larger counterparts, mini injection molding machines boast smaller footprints, making them ideal for space-constrained environments such as laboratories, research facilities, and small-scale production facilities. Despite their diminutive size, these machines offer impressive capabilities, facilitating the production of micro-components with micron-level precision. From medical devices to consumer electronics, mini injection molding machines cater to a diverse array of industries, offering a cost-effective solution for prototyping, small-batch production, and specialized applications.
Cost-Effectiveness and Rapid Prototyping
The cost-effectiveness of mini injection molding machines opens doors to rapid prototyping and iterative design processes, empowering manufacturers to bring concepts to fruition with minimal investment and lead time. By minimizing material wastage, energy consumption, and setup costs, mini injection molding facilitates agile product development cycles, allowing designers and engineers to iterate designs, test prototypes, and refine products in a fraction of the time compared to traditional manufacturing methods. This agility not only accelerates time-to-market but also mitigates risks associated with product development, fostering innovation and competitiveness in dynamic market environments.
Customization and Personalization
In an era defined by personalization and customization, mini injection molding emerges as a catalyst for innovation, enabling manufacturers to tailor products to individual preferences and market demands. The versatility of mini injection molding machines facilitates the production of bespoke components, ranging from intricate cosmetic parts to functional prototypes, with unparalleled precision and repeatability. By leveraging advanced materials, multi-cavity molds, and digital design technologies, manufacturers can offer a diverse range of customizable products, catering to niche markets and consumer segments with unique preferences and requirements.
Sustainability and Environmental Impact
Despite their compact size, mini injection molding machines champion sustainability and environmental stewardship, offering eco-friendly alternatives to traditional manufacturing processes. By optimizing material usage, reducing energy consumption, and minimizing waste generation, mini injection molding aligns with the principles of sustainable manufacturing, mitigating environmental impact without compromising on performance or quality. Furthermore, the scalability of mini injection molding facilitates localized production, reducing carbon emissions associated with transportation and logistics, and promoting regional economic development.
Conclusion:
In conclusion, mini injection molding epitomizes the convergence of innovation, efficiency, and sustainability in modern manufacturing. From its compact design and versatility to its cost-effectiveness, customization capabilities, and environmental benefits, mini injection molding unlocks a world of possibilities for manufacturers seeking to stay ahead in an increasingly competitive and dynamic market landscape. As technology continues to evolve and consumer preferences evolve, the potential of mini injection molding remains boundless, paving the way for new applications, industries, and opportunities on the horizon.
GETTING A QUOTE WITH LK-MOULD IS FREE AND SIMPLE.
FIND MORE OF OUR SERVICES:
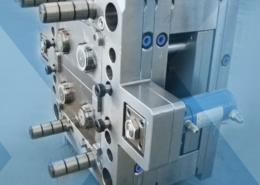
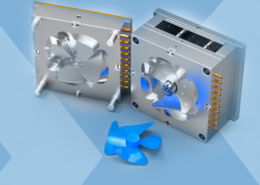
Plastic Molding
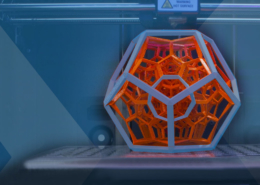
Rapid Prototyping
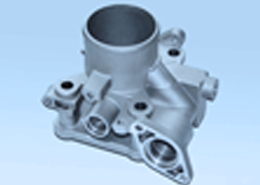
Pressure Die Casting
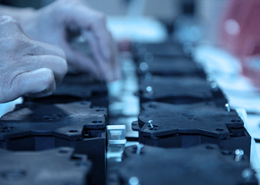
Parts Assembly
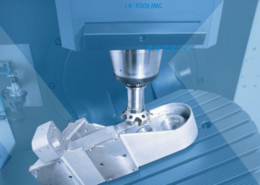