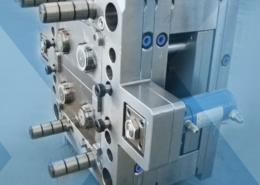
Unraveling the Relationship Between Mold and Plastic: A Comprehensive Exploratio
Author:gly Date: 2024-06-08
The intricate dance between mold and plastic lies at the heart of modern manufacturing processes, shaping industries, economies, and daily lives. This article aims to unravel the symbiotic relationship between mold and plastic, delving into its origins, applications, techniques, challenges, and future prospects.
Introduction: The Dynamic Duo of Manufacturing
Mold and plastic constitute an inseparable duo in the realm of manufacturing, with each playing a crucial role in shaping the other's destiny. The marriage of these two elements has given birth to a myriad of products that have revolutionized industries and transformed societies. From automotive components to consumer electronics, from medical devices to packaging materials, the influence of mold and plastic permeates every aspect of our modern world.
Background and Evolution
The history of mold and plastic intertwines with the evolution of human ingenuity and technological advancement. The origins of molding can be traced back to ancient civilizations, where craftsmen utilized rudimentary techniques to shape clay, metal, and other materials into functional objects. With the advent of the Industrial Revolution, the development of mechanized molding techniques paved the way for mass production, democratizing access to goods and fueling economic growth.
The Art and Science of Plastic Injection Molding
Plastic injection molding stands as a cornerstone of modern manufacturing, offering unparalleled versatility, efficiency, and precision in the production of plastic components.
Process Overview
The plastic injection molding process begins with the creation of a mold, typically made of steel or aluminum, which is precision-machined to the desired geometry. Molten plastic resin is then injected into the mold cavity under high pressure, where it cools and solidifies to form the final product. The ability to produce complex shapes with tight tolerances makes injection molding ideal for a wide range of applications.
Material Selection and Compatibility
Choosing the right plastic resin is essential for achieving desired mechanical, thermal, and aesthetic properties in the final product. Factors such as melt flow characteristics, shrinkage behavior, and chemical resistance must be carefully considered to ensure optimal performance and durability. Additionally, compatibility between the plastic resin and mold material is critical to prevent issues such as adhesion failure, warping, and mold corrosion.
Design Considerations
Effective design for plastic injection molding requires careful attention to factors such as part geometry, wall thickness, draft angles, and gating locations. Optimizing these parameters helps minimize manufacturing defects, such as sink marks, weld lines, and air traps, while maximizing part strength, surface finish, and dimensional accuracy.
Challenges and Innovations in Mold Design and Fabrication
The design and fabrication of molds present unique challenges and opportunities for innovation in the realm of plastic manufacturing.
Complexity and Precision
Designing molds for intricate or multi-component parts requires advanced CAD/CAM software and precision machining techniques. Complex geometries, tight tolerances, and multi-cavity configurations demand meticulous attention to detail to ensure uniform material distribution and part quality.
Tooling Materials and Durability
The choice of tooling materials, such as steel, aluminum, or high-performance alloys, depends on factors such as production volume, part complexity, and budget constraints. While steel molds offer superior durability and longevity, aluminum molds provide faster turnaround times and lower upfront costs. Innovations in mold coatings, surface treatments, and heat treatments enhance wear resistance, corrosion resistance, and part release properties, prolonging mold life and reducing maintenance requirements.
Rapid Prototyping and Iterative Design
Advancements in rapid prototyping technologies, such as 3D printing and CNC machining, enable manufacturers to accelerate the design iteration process and reduce time-to-market for new products. By rapidly producing functional prototypes and conducting iterative design evaluations, engineers can identify and address potential issues early in the development cycle, saving time and resources in the long run.
Future Directions and Emerging Trends
As technology continues to evolve, the future of mold and plastic manufacturing holds promise for exciting innovations and advancements.
Sustainability and Circular Economy
The growing emphasis on sustainability and environmental stewardship is driving demand for eco-friendly materials, biodegradable plastics, and closed-loop recycling processes. Innovations in material science, such as bio-based polymers, compostable resins, and chemical recycling technologies, pave the way for a more sustainable and circular economy, reducing reliance on finite resources and mitigating environmental impact.
Digitalization and Industry 4.0
The integration of digital technologies, such as IoT sensors, artificial intelligence, and cloud computing, into mold and plastic manufacturing processes enables real-time monitoring, predictive maintenance, and data-driven decision-making. By leveraging digital twins, virtual simulations, and predictive analytics, manufacturers can optimize production workflows, minimize downtime, and improve overall operational efficiency.
Customization and Personalization
The rise of mass customization and personalized products is reshaping consumer preferences and market dynamics. Advancements in digital design tools, additive manufacturing techniques, and on-demand manufacturing platforms empower consumers to tailor products to their individual needs and preferences, driving demand for flexible, agile manufacturing processes that can adapt to changing market trends and customer demands.
Conclusion: Forging the Future of Manufacturing
In conclusion, the interplay between mold and plastic continues to shape the landscape of modern manufacturing, driving innovation, efficiency, and sustainability. As we navigate the complexities of a rapidly changing world, embracing emerging technologies, fostering collaboration, and embracing a spirit of continuous improvement will be essential for unlocking the full potential of mold and plastic manufacturing. By harnessing the power of creativity, ingenuity, and human ingenuity, we can build a brighter future where mold and plastic serve as catalysts for progress, prosperity, and sustainable development.
GETTING A QUOTE WITH LK-MOULD IS FREE AND SIMPLE.
FIND MORE OF OUR SERVICES:
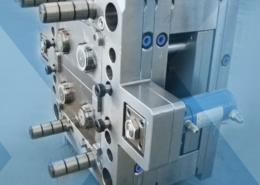
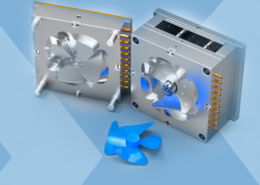
Plastic Molding
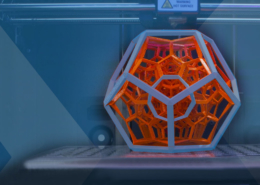
Rapid Prototyping
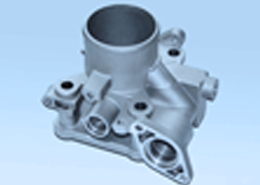
Pressure Die Casting
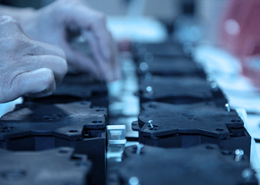
Parts Assembly
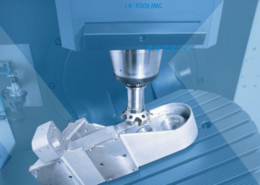