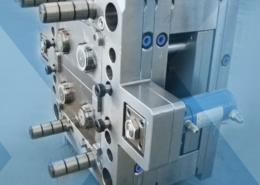
Industrial Injection Molding: Revolutionizing Manufacturing Processes
Author:gly Date: 2024-06-08
Injection molding stands as a cornerstone in modern industrial manufacturing, heralding a revolution in mass production processes. Its significance spans across various sectors, from automotive to consumer goods, owing to its efficiency, versatility, and cost-effectiveness. This article delves into the realm of industrial injection molding, exploring its intricacies, applications, and impact on contemporary manufacturing.
The Essence of Injection Molding
Introduction to Injection Molding
Industrial injection molding entails the process of injecting molten material into a mold cavity, whereupon it solidifies to form the desired product. Initially developed in the late 19th century, it has evolved into a sophisticated technique, fueling the production of intricate components with remarkable precision and consistency.
Operational Mechanics
The process initiates with the melting of raw material, typically thermoplastics, within a heated barrel. The molten material is then injected into the mold under high pressure, conforming to its shape and intricacies. Following solidification, the mold opens, releasing the newly formed product.
Advantages Over Conventional Methods
Injection molding offers a plethora of advantages over traditional manufacturing techniques. Its ability to produce complex geometries with minimal post-processing, coupled with high production rates, renders it indispensable in modern industries seeking efficiency and cost-effectiveness.
Applications Across Industries
Automotive Sector
In the automotive industry, injection molding finds extensive application in the production of interior components, exterior panels, and intricate engine parts. Its capacity to manufacture lightweight, durable components at scale aligns with the sector's pursuit of performance and fuel efficiency.
Consumer Goods
From electronics to household appliances, injection molding permeates the realm of consumer goods manufacturing. Its versatility enables the production of diverse products, ranging from smartphone casings to kitchen utensils, with unparalleled precision and consistency.
Medical Devices
The medical sector relies on injection molding for the fabrication of sterile, high-precision components crucial for diagnostic and therapeutic purposes. The process's ability to maintain stringent tolerances and material purity ensures compliance with regulatory standards and patient safety.
Technological Innovations
Additive Manufacturing Integration
The convergence of injection molding with additive manufacturing techniques, such as 3D printing, promises novel avenues for product development and customization. Hybrid processes enable the rapid prototyping of molds, facilitating iterative design iterations and reducing time-to-market.
Smart Manufacturing
The advent of Industry 4.0 technologies has catalyzed the transformation of injection molding processes into smart, data-driven systems. Integration of sensors, IoT devices, and AI algorithms optimizes production parameters, enhances quality control, and minimizes downtime, ushering in an era of predictive maintenance and efficiency.
Sustainable Practices
Efforts to mitigate environmental impact have spurred the adoption of sustainable practices within the injection molding industry. From biodegradable polymers to closed-loop recycling systems, manufacturers are increasingly embracing eco-friendly alternatives to traditional materials and processes, fostering a greener, more sustainable future.
Challenges and Future Outlook
Material Innovation
The quest for novel materials with enhanced properties, such as improved strength-to-weight ratios and recyclability, poses a significant challenge for the injection molding industry. Research endeavors focus on developing bio-based polymers, composite materials, and advanced additives to meet evolving market demands and regulatory requirements.
Supply Chain Resilience
Global supply chain disruptions underscore the importance of resilience and agility within the injection molding ecosystem. Adoption of digital twin technologies, decentralized manufacturing networks, and localized sourcing strategies mitigates risks associated with geopolitical instability and natural disasters, ensuring uninterrupted production cycles.
Skills Development
As manufacturing processes evolve, the demand for skilled professionals proficient in injection molding technologies intensifies. Collaborative efforts between academia, industry, and government entities are imperative to foster talent development, equipping the workforce with the requisite knowledge and skills to navigate the complexities of modern manufacturing.
Conclusion
Industrial injection molding epitomizes innovation and efficiency in modern manufacturing, offering unparalleled capabilities in producing complex components across diverse industries. As technological advancements continue to redefine the landscape, embracing sustainability, innovation, and adaptability will be paramount in shaping the future of injection molding and its pivotal role in driving global industrial progress.
GETTING A QUOTE WITH LK-MOULD IS FREE AND SIMPLE.
FIND MORE OF OUR SERVICES:
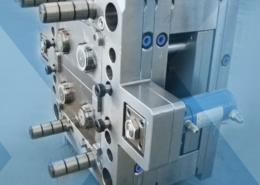
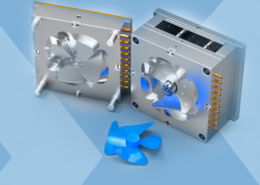
Plastic Molding
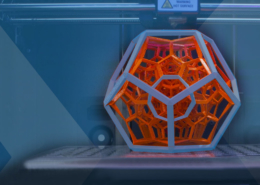
Rapid Prototyping
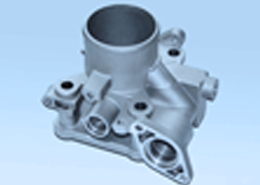
Pressure Die Casting
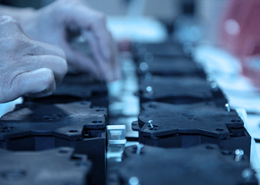
Parts Assembly
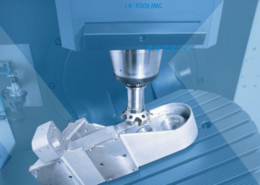