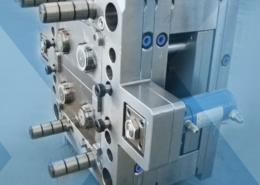
Understanding Injection Extrusion: Revolutionizing Manufacturing Processes
Author:gly Date: 2024-06-08
Injection extrusion, a cutting-edge technique in manufacturing, has revolutionized the production of various products across industries. This method involves the forced passage of a material through a specially designed nozzle or die to create intricate shapes and forms. In this article, we delve into the depths of injection extrusion, exploring its mechanisms, applications, benefits, and future prospects.
Mechanisms of Injection ExtrusionInjection extrusion operates on the principle of forcing a material through a small orifice under high pressure to shape it into a desired form. The process begins with the material being heated to a molten state, ensuring it is malleable and can flow easily. Then, the molten material is injected into a specially designed mold or die, where it takes the shape of the cavity. Finally, the material is cooled and solidified, resulting in the final product.
This method offers precise control over the shape and dimensions of the product, making it ideal for manufacturing complex components with tight tolerances. Moreover, injection extrusion allows for high production rates, making it a cost-effective solution for mass production.
Applications of Injection ExtrusionInjection extrusion finds applications across a wide range of industries, including automotive, aerospace, medical, and consumer goods. In the automotive sector, it is used to manufacture components such as fuel lines, seals, and gaskets with exceptional durability and performance.
In the aerospace industry, injection extrusion is employed to produce lightweight yet robust parts for aircraft and spacecraft, contributing to fuel efficiency and overall performance. In the medical field, this technique is utilized to fabricate precision instruments, implants, and prosthetics with high biocompatibility and dimensional accuracy.
Advantages of Injection ExtrusionThe advantages of injection extrusion are manifold. Firstly, it allows for the production of complex geometries with minimal material wastage, enhancing efficiency and sustainability. Additionally, injection extrusion offers excellent surface finish and dimensional accuracy, eliminating the need for secondary machining operations.
Furthermore, this method enables the incorporation of reinforcements and additives into the material, enhancing its mechanical properties and functionality. With its ability to process a wide range of materials, including metals, polymers, and ceramics, injection extrusion provides unparalleled versatility in manufacturing.
Future Perspectives and ChallengesLooking ahead, the future of injection extrusion holds immense potential for innovation and advancement. Researchers are exploring new materials and formulations to expand the capabilities of this technique further. Additionally, efforts are underway to optimize process parameters and enhance automation to improve productivity and reduce costs.
However, several challenges must be addressed to fully realize the potential of injection extrusion. These include optimizing energy consumption, minimizing material waste, and developing robust quality control measures to ensure consistent product quality.
ConclusionIn conclusion, injection extrusion stands as a cornerstone of modern manufacturing, offering unparalleled precision, efficiency, and versatility. With its wide-ranging applications across industries and ongoing advancements in materials and processes, injection extrusion is poised to shape the future of manufacturing. By understanding its mechanisms, applications, and benefits, we can harness the full potential of this transformative technique to drive innovation and progress in the years to come.
GETTING A QUOTE WITH LK-MOULD IS FREE AND SIMPLE.
FIND MORE OF OUR SERVICES:
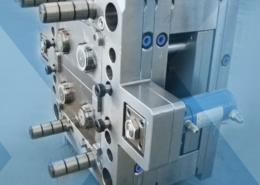
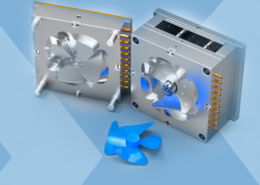
Plastic Molding
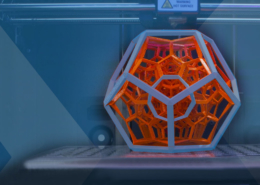
Rapid Prototyping
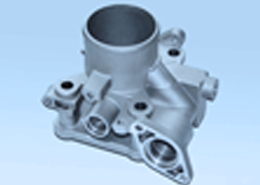
Pressure Die Casting
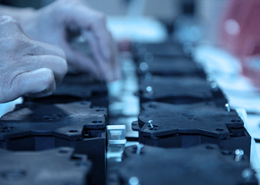
Parts Assembly
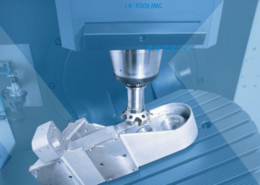