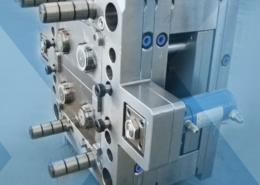
Unveiling the Art of Pallet Moulding
Author:gly Date: 2024-06-08
Pallet moulding stands as a cornerstone of modern logistics and supply chain management, providing a sturdy and reliable platform for transporting goods and materials. From warehouses to factories and distribution centers, pallets play a crucial role in streamlining operations and optimizing storage space. In this article, we delve into the intricate world of pallet moulding, exploring its origins, mechanics, applications, and future prospects.
Origins and Background
The history of pallets can be traced back to ancient civilizations, where wooden platforms were used to facilitate the movement of goods. However, the modern pallet as we know it today emerged in the early 20th century with the rise of industrialization and mass production. With the advent of forklifts and standardized containerization, pallets became essential components of modern logistics systems, enabling efficient handling, storage, and transportation of goods on a global scale.
Mechanics and Operation
Pallet moulding involves the use of specialized moulds and plastic materials to create durable and standardized pallets. The process typically begins with the heating of plastic resin pellets until they reach a molten state, followed by injection or compression into a mould cavity to form the desired pallet shape. Once cooled and solidified, the pallet is removed from the mould and undergoes finishing processes such as trimming, smoothing, and assembly. The choice of moulding technique and material depends on factors such as load capacity, durability requirements, and cost considerations.
Types of Pallet Moulding Processes
Injection Moulding
Injection moulding is a widely used process for producing plastic pallets with high precision and consistency. The process involves injecting molten plastic material into a mould cavity under high pressure, where it solidifies to form the final product. Injection moulding offers fast cycle times, tight tolerances, and excellent surface finish, making it suitable for mass production of standardized pallets.
Compression Moulding
Compression moulding is another common technique used for producing plastic pallets, particularly for heavy-duty applications requiring high strength and durability. The process involves placing plastic resin pellets in a heated mould cavity and compressing them under high pressure until they conform to the shape of the mould. Compression moulding offers advantages such as lower tooling costs, shorter cycle times, and the ability to incorporate reinforcing fibers or fillers for added strength.
Structural Foam Moulding
Structural foam moulding is a variation of injection moulding that produces pallets with a cellular core structure, resulting in enhanced strength and rigidity. The process involves injecting a foaming agent into the molten plastic resin, which expands and creates a cellular structure as the material fills the mould cavity. Structural foam moulding offers advantages such as reduced material usage, improved impact resistance, and enhanced load-bearing capacity, making it suitable for heavy-duty pallets used in automotive, chemical, and construction industries.
Advantages and Benefits
Durability and Strength
Plastic pallets offer superior durability and strength compared to traditional wooden pallets, withstanding heavy loads, impacts, and environmental conditions. Molded plastic pallets are resistant to moisture, chemicals, and pests, ensuring long-term reliability and performance in demanding industrial environments.
Standardization and Consistency
Pallet moulding processes enable the production of standardized pallets with consistent dimensions, weight, and performance characteristics. Standardized pallets facilitate compatibility with automated handling systems, storage racks, and transportation vehicles, streamlining logistics operations and reducing the risk of product damage or loss.
Sustainability and Environmental Impact
Plastic pallets offer advantages in terms of sustainability and environmental impact compared to wooden pallets. Plastic pallets are reusable, recyclable, and can be made from recycled materials, reducing the consumption of natural resources and minimizing waste generation. Additionally, plastic pallets are lightweight, contributing to fuel savings and lower carbon emissions during transportation.
Applications and Industries
Pallet moulding finds applications across various industries and sectors, each benefiting from the unique properties and advantages of plastic pallets.
Logistics and Supply Chain Management
In the logistics and supply chain management sector, plastic pallets are widely used for transporting, storing, and handling goods in warehouses, distribution centers, and manufacturing facilities. Plastic pallets offer advantages such as consistent dimensions, cleanliness, and compatibility with automated handling systems, enhancing operational efficiency and product safety.
Food and Beverage Industry
In the food and beverage industry, plastic pallets are used for transporting and storing food products in compliance with hygiene and safety standards. Plastic pallets offer advantages such as resistance to moisture, chemicals, and bacterial contamination, ensuring product integrity and quality throughout the supply chain.
Pharmaceutical and Healthcare Sector
In the pharmaceutical and healthcare sector, plastic pallets are used for transporting and storing medical devices, pharmaceutical products, and healthcare supplies. Plastic pallets offer advantages such as cleanliness, sterility, and compatibility with cleanroom environments, ensuring product safety and regulatory compliance in critical applications.
Future Directions and Innovations
Looking ahead, the future of pallet moulding holds promise for further advancements and innovations. Researchers and manufacturers are exploring new materials, technologies, and design concepts to enhance the performance, sustainability, and functionality of plastic pallets. Initiatives such as lightweighting, automation, and digitalization aim to optimize pallet design, production processes, and supply chain logistics, driving efficiency, and cost savings.
Conclusion
In conclusion, pallet moulding represents a vital component of modern logistics and supply chain management, providing durable, standardized, and sustainable solutions for handling and transporting goods. From its humble beginnings to its current state-of-the-art technologies, pallet moulding continues to evolve and innovate, shaping the way we move and manage products around the world. By embracing sustainability, standardization, and innovation, the future of pallet moulding holds promise for creating a more efficient, resilient, and interconnected supply chain ecosystem. As we navigate the challenges and opportunities ahead, let us continue to push the boundaries of what is possible and strive for excellence in pallet moulding.
GETTING A QUOTE WITH LK-MOULD IS FREE AND SIMPLE.
FIND MORE OF OUR SERVICES:
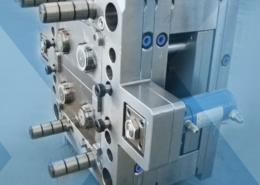
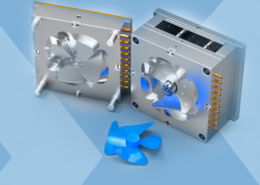
Plastic Molding
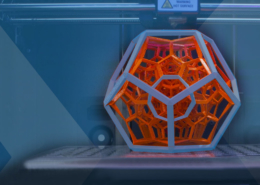
Rapid Prototyping
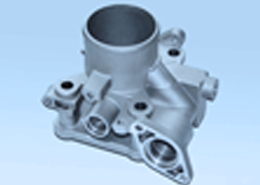
Pressure Die Casting
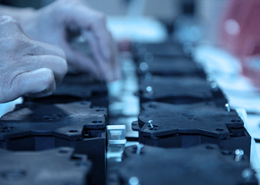
Parts Assembly
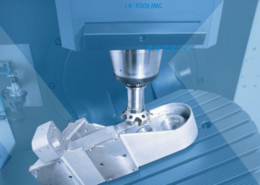