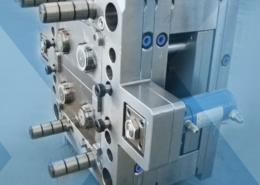
Unveiling the Potential of PBT Injection Molding: Revolutionizing Polymer Manufa
Author:gly Date: 2024-06-08
PBT (Polybutylene Terephthalate) injection molding stands at the forefront of polymer manufacturing, offering a plethora of advantages in producing intricate components with exceptional durability and thermal stability. This article delves into the intricacies of PBT injection molding, exploring its mechanisms, applications, and future prospects.
Introduction: Exploring the World of PBT Injection Molding
PBT injection molding heralds a new era in polymer manufacturing, leveraging its unique properties to create robust and versatile components. With a growing demand for high-performance materials in various industries, PBT emerges as a frontrunner, offering unparalleled mechanical strength, chemical resistance, and dimensional stability.
Mechanisms and Process Overview
The Injection Process
PBT injection molding follows a similar process to conventional injection molding techniques. It begins with the feeding of PBT resin pellets into a heated barrel, where they are melted to a precise temperature. The molten PBT is then injected into a mold cavity under high pressure, where it cools and solidifies to form the desired component. The intricacies of temperature control, pressure regulation, and mold design are crucial in ensuring the quality and efficiency of the process.
Mold Design and Optimization
Mold design plays a pivotal role in PBT injection molding, influencing the part's geometry, surface finish, and mechanical properties. Advanced techniques such as computer-aided design (CAD) and mold flow analysis aid in optimizing mold geometry, gate design, and cooling channels, minimizing defects and cycle times. Additionally, the selection of mold materials with high thermal conductivity enhances heat dissipation, promoting uniform cooling and reducing warpage.
Material Selection and Compatibility
The choice of PBT resin grade is critical in achieving desired part properties and performance. Factors such as filler content, molecular weight distribution, and additives influence mechanical strength, dimensional stability, and processability. Moreover, ensuring compatibility between PBT resin and processing parameters is paramount in mitigating issues such as degradation, flow instabilities, and mold fouling.
Applications Across Industries
PBT injection molding finds extensive applications across diverse industries, catering to a wide range of functional and aesthetic requirements.
Automotive Sector
In the automotive industry, PBT injection molding is utilized in the production of various components such as connectors, housings, and under-the-hood parts. Its exceptional thermal stability, chemical resistance, and electrical insulation properties make it ideal for demanding applications in engine compartments and electrical systems.
Electrical and Electronics
PBT is widely used in the electrical and electronics sector for manufacturing connectors, sockets, and insulating components. Its excellent dielectric properties, flame retardancy, and dimensional stability ensure reliable performance in diverse operating conditions, ranging from household appliances to telecommunications equipment.
Consumer Goods
In the consumer goods industry, PBT injection molding enables the production of durable and aesthetically pleasing products such as tool handles, sports equipment, and kitchen utensils. Its ability to withstand harsh environments, UV exposure, and chemical exposure enhances product longevity and user satisfaction.
Advancements and Future Outlook
PBT injection molding continues to evolve, driven by advancements in material science, manufacturing technologies, and market demands.
Material Innovations
Ongoing research in PBT resin formulations leads to the development of enhanced grades with improved properties such as impact resistance, thermal conductivity, and recyclability. These innovations broaden the application scope of PBT injection molding, catering to emerging trends in sustainability and performance optimization.
Process Optimization
Continuous improvement in injection molding processes, including melt rheology control, mold temperature management, and cycle time optimization, enhances the efficiency and cost-effectiveness of PBT manufacturing. Furthermore, the integration of industry 4.0 technologies such as real-time monitoring, predictive maintenance, and data-driven decision-making fosters productivity and quality assurance.
Conclusion: Embracing the Potential of PBT Injection Molding
In conclusion, PBT injection molding stands as a cornerstone of modern polymer manufacturing, offering unparalleled versatility, reliability, and performance. Its widespread adoption across industries underscores its significance in driving innovation and productivity. Embracing advancements in material science and process optimization will unlock new opportunities for PBT injection molding, shaping the future of manufacturing in a sustainable and efficient manner.
GETTING A QUOTE WITH LK-MOULD IS FREE AND SIMPLE.
FIND MORE OF OUR SERVICES:
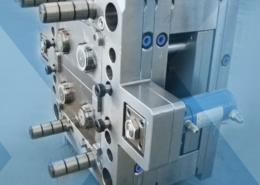
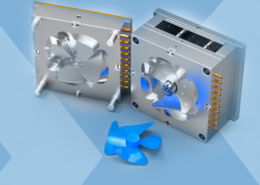
Plastic Molding
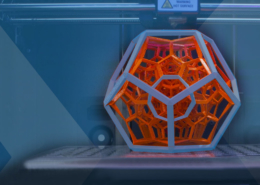
Rapid Prototyping
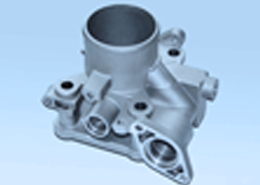
Pressure Die Casting
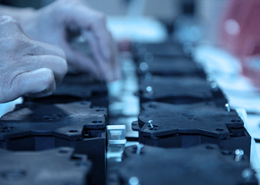
Parts Assembly
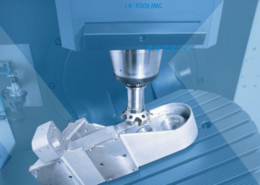