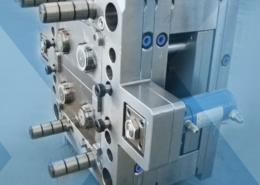
Exploring Plastic Bucket Mould: The Backbone of Manufacturing
Author:gly Date: 2024-06-08
Plastic bucket moulds play a crucial role in the manufacturing process, enabling the production of a wide range of plastic buckets used in various industries, from construction and agriculture to household and retail. These moulds serve as the backbone of the manufacturing industry, facilitating the efficient and cost-effective production of durable and versatile plastic buckets. In this article, we will delve into the world of plastic bucket moulds, exploring their design, manufacturing process, applications, and impact on the industry.
Understanding Plastic Bucket Moulds
Design and Construction
Plastic bucket moulds are meticulously designed and engineered to produce buckets of consistent quality and dimensional accuracy. The design process involves considering factors such as bucket size, shape, thickness, and handle placement to ensure optimal performance and functionality.
Material Selection
The choice of mould material is critical in determining the durability and longevity of plastic bucket moulds. High-quality steel, such as P20, H13, or S136, is commonly used for mould construction due to its excellent wear resistance, hardness, and machinability, ensuring prolonged mould life and minimal maintenance requirements.
Manufacturing Process
The manufacturing process of plastic bucket moulds typically involves several stages, including machining, heat treatment, and surface finishing. Advanced machining techniques, such as CNC milling and EDM (Electrical Discharge Machining), are employed to achieve precise and intricate mould cavities and cores, while heat treatment enhances the hardness and strength of the mould com
Exploring Plastic Bucket Mould: The Backbone of Manufacturing
Plastic bucket moulds play a crucial role in the manufacturing process, enabling the production of a wide range of plastic buckets used in various industries, from construction and agriculture to household and retail. These moulds serve as the backbone of the manufacturing industry, facilitating the efficient and cost-effective production of durable and versatile plastic buckets. In this article, we will delve into the world of plastic bucket moulds, exploring their design, manufacturing process, applications, and impact on the industry.
Understanding Plastic Bucket Moulds
Design and Construction
Plastic bucket moulds are meticulously designed and engineered to produce buckets of consistent quality and dimensional accuracy. The design process involves considering factors such as bucket size, shape, thickness, and handle placement to ensure optimal performance and functionality.
Material Selection
The choice of mould material is critical in determining the durability and longevity of plastic bucket moulds. High-quality steel, such as P20, H13, or S136, is commonly used for mould construction due to its excellent wear resistance, hardness, and machinability, ensuring prolonged mould life and minimal maintenance requirements.
Manufacturing Process
The manufacturing process of plastic bucket moulds typically involves several stages, including machining, heat treatment, and surface finishing. Advanced machining techniques, such as CNC milling and EDM (Electrical Discharge Machining), are employed to achieve precise and intricate mould cavities and cores, while heat treatment enhances the hardness and strength of the mould components.
Production of Plastic Buckets
Injection Moulding Process
The production of plastic buckets using plastic bucket moulds primarily relies on the injection moulding process. During injection moulding, molten plastic material is injected into the cavity of the mould under high pressure, where it cools and solidifies to form the desired bucket shape. This process allows for high-volume production of plastic buckets with consistent quality and dimensional accuracy.
Quality Control Measures
Ensuring the quality of plastic buckets produced using plastic bucket moulds requires stringent quality control measures. Advanced technologies, such as automated inspection systems and quality management software, are employed to detect defects, monitor production parameters, and maintain product consistency throughout the manufacturing process.
Customization and Innovation
Plastic bucket moulds offer flexibility and versatility in producing buckets of various sizes, shapes, colors, and features to meet diverse customer requirements. Manufacturers continuously innovate and incorporate new technologies, such as multi-cavity moulds, in-mould labeling, and biodegradable materials, to enhance product functionality, sustainability, and market competitiveness.
Applications and Impact
Industrial and Commercial Use
Plastic buckets produced using plastic bucket moulds find widespread applications across industries, including construction, agriculture, food processing, chemical, and retail. They are used for storage, transport, and packaging of liquids, powders, granules, and solids, showcasing their versatility and utility in diverse industrial and commercial settings.
Environmental Considerations
While plastic buckets offer numerous benefits in terms of durability, versatility, and cost-effectiveness, their environmental impact, particularly in terms of plastic waste and pollution, cannot be overlooked. Manufacturers and consumers alike are increasingly adopting sustainable practices, such as recycling, using biodegradable materials, and reducing single-use plastics, to minimize the environmental footprint of plastic buckets and their production processes.
Conclusion
In conclusion, plastic bucket moulds play a vital role in the manufacturing industry, enabling the efficient and cost-effective production of plastic buckets used in various applications. By understanding the design, manufacturing process, applications, and impact of plastic bucket moulds, manufacturers can optimize their production processes, enhance product quality, and address environmental concerns. Looking ahead, continued innovation and collaboration across the industry are essential to drive sustainability, efficiency, and innovation in plastic bucket moulding technologies.
GETTING A QUOTE WITH LK-MOULD IS FREE AND SIMPLE.
FIND MORE OF OUR SERVICES:
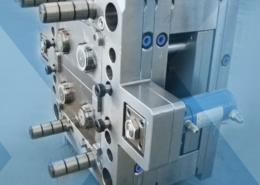
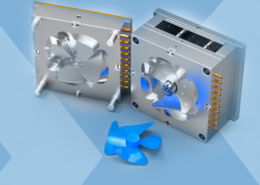
Plastic Molding
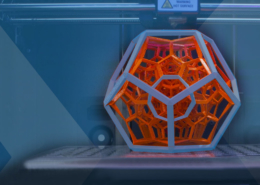
Rapid Prototyping
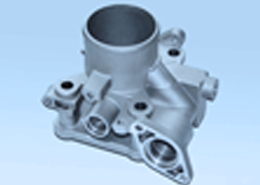
Pressure Die Casting
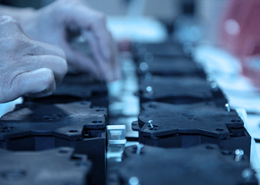
Parts Assembly
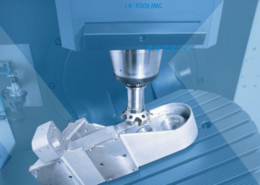