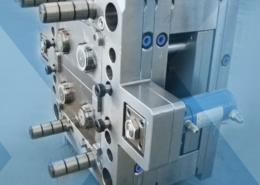
Plastic Cap Mould: Revolutionizing Packaging Solutions
Author:gly Date: 2024-06-08
Introduction:
In the realm of packaging, the plastic cap mould plays a pivotal role in ensuring the safety, freshness, and convenience of a wide range of products. From beverages to cosmetics, plastic caps are essential components that provide a seal, protection, and tamper-evidence. In this exploration, we delve into the world of plastic cap moulds, uncovering their significance, applications, manufacturing process, and future prospects.
Significance of Plastic Cap Moulds
Plastic cap moulds are critical components in the packaging industry, as they enable the mass production of plastic caps with consistent quality, precision, and efficiency. These moulds are designed to create caps of various sizes, shapes, and functionalities to meet the diverse needs of manufacturers and consumers. Whether it's a screw cap for a beverage bottle or a flip-top cap for a shampoo bottle, plastic cap moulds play a crucial role in ensuring product integrity and consumer satisfaction.
Applications Across Industries
The applications of plastic cap moulds span across numerous industries, including food and beverage, pharmaceuticals, cosmetics, and household products. In the food and beverage industry, plastic caps are used to seal bottles and containers for water, juice, soda, and other beverages, preserving freshness and preventing contamination. In the pharmaceutical sector, they serve as closures for medicine bottles, ensuring dosage accuracy and tamper-evidence. Moreover, in the cosmetics industry, plastic caps provide a stylish and functional finishing touch to perfume bottles, lotion containers, and skincare products.
The Manufacturing Process
The manufacturing process of plastic cap moulds involves several steps, including mould design, material selection, injection moulding, and finishing. Mould design is crucial to ensuring the desired shape, dimensions, and functionality of the plastic cap. Material selection depends on factors such as product requirements, environmental considerations, and regulatory compliance. Injection moulding, the heart of the process, involves injecting molten plastic into a mould cavity under high pressure, where it solidifies to form the desired shape. Finally, finishing processes such as trimming, cutting, and assembly may be performed to refine the appearance and functionality of the plastic cap.
Future Prospects and Innovations
Looking ahead, the future of plastic cap moulds is filled with promise and opportunity. With ongoing advancements in materials, technologies, and sustainability practices, plastic cap moulds are poised to become more efficient, versatile, and environmentally friendly. Innovations such as biodegradable plastics, recycled materials, and additive manufacturing techniques offer exciting possibilities for reducing waste, lowering costs, and enhancing product performance. Moreover, digitalization and automation are revolutionizing the manufacturing process, enabling greater efficiency, accuracy, and customization in the production of plastic caps.
Conclusion:
In conclusion, plastic cap moulds play a crucial role in the packaging industry, providing essential components for sealing, protecting, and enhancing the appeal of products. With their significance across diverse industries, precision manufacturing processes, and ongoing innovations, plastic cap moulds are poised to shape the future of packaging solutions. As we continue to explore the possibilities of plastic cap moulds, let us embrace the opportunities for innovation, sustainability, and excellence in the ever-evolving world of packaging.
GETTING A QUOTE WITH LK-MOULD IS FREE AND SIMPLE.
FIND MORE OF OUR SERVICES:
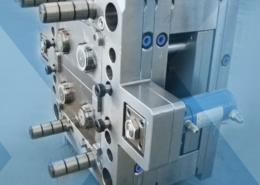
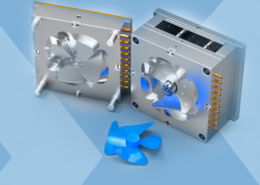
Plastic Molding
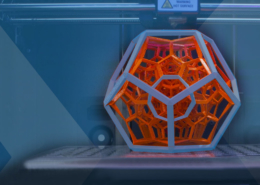
Rapid Prototyping
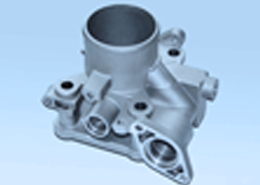
Pressure Die Casting
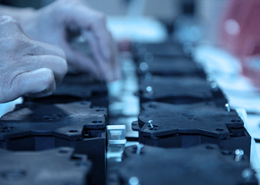
Parts Assembly
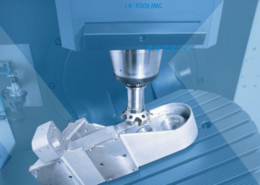