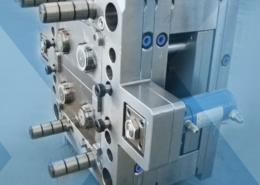
Unveiling the Potential of Plastic Injection Tooling
Author:gly Date: 2024-06-08
Introduction
Plastic injection tooling stands as a pivotal component in the realm of manufacturing, embodying precision, innovation, and efficiency. As a cornerstone of modern production processes, plastic injection tooling holds the key to unlocking a world of possibilities in the creation of intricate and high-quality plastic parts. In this article, we delve into the realm of plastic injection tooling, exploring its significance, functionality, and impact across various industries.
The Essence of Plastic Injection Tooling
Plastic injection tooling, also known as injection molding tooling, comprises intricate molds and dies designed to shape molten plastic into desired forms. These tooling systems serve as the backbone of injection molding processes, enabling the mass production of components with unparalleled precision and repeatability.
Precision Engineering
At the heart of plastic injection tooling lies precision engineering, where intricate molds are meticulously crafted to exact specifications. Advanced machining techniques, including CNC milling and EDM, ensure the creation of molds with precise dimensions and intricate features. This precision is paramount in achieving uniformity and consistency in the produced parts.
Material Selection
The choice of materials for plastic injection tooling is critical to its performance and longevity. High-quality steels, such as P20, H13, and stainless steel, are commonly employed for their excellent thermal conductivity, wear resistance, and machinability. These materials withstand the rigors of high-temperature molding processes, ensuring the durability and reliability of the tooling.
Surface Finish and Texture
Surface finish and texture play a crucial role in the quality and aesthetics of injection-molded parts. Through techniques such as polishing, etching, and texturing, mold surfaces are meticulously finished to achieve desired surface characteristics. This attention to detail enhances the appearance and functionality of the final products, meeting the stringent requirements of diverse industries.
Applications Across Industries
Plastic injection tooling finds extensive applications across a myriad of industries, revolutionizing manufacturing processes and enabling the production of diverse plastic components and products.
Automotive Industry
In the automotive sector, plastic injection tooling is instrumental in the production of interior and exterior components, ranging from dashboards to bumpers. The ability to mold complex shapes and intricate details with high precision makes injection molding indispensable in automotive manufacturing, driving efficiency and innovation.
Consumer Electronics
The consumer electronics industry relies on plastic injection tooling for the fabrication of casings, enclosures, and components for smartphones, tablets, and electronic gadgets. The demand for lightweight, durable, and aesthetically pleasing parts necessitates the use of injection molding, offering manufacturers the flexibility to meet evolving consumer preferences.
Medical Devices
In the medical sector, plastic injection tooling plays a vital role in the production of sterile and biocompatible components for medical devices and equipment. From syringe barrels to surgical instruments, injection molding enables the manufacturing of precision parts that meet stringent regulatory standards for safety and efficacy.
Advancements and Future Directions
The field of plastic injection tooling continues to evolve, driven by advancements in materials, technology, and manufacturing processes. Future trends such as additive manufacturing, micro-injection molding, and sustainability initiatives are poised to reshape the landscape of injection molding.
Additive Manufacturing
Additive manufacturing, or 3D printing, presents exciting opportunities for the fabrication of plastic injection tooling with complex geometries and internal features. This emerging technology offers greater design freedom and shorter lead times, revolutionizing the traditional mold-making process.
Micro-injection Molding
The demand for miniaturized components in industries such as electronics and healthcare has led to the development of micro-injection molding techniques. These processes enable the production of small, intricate parts with high precision, opening new avenues for innovation in product design and manufacturing.
Sustainability Initiatives
As environmental concerns mount, the plastics industry is embracing sustainability initiatives to minimize waste and reduce carbon footprint. From recycled materials to biodegradable resins, injection molding is evolving to meet the demands of a more eco-conscious market, paving the way for greener and more sustainable manufacturing practices.
Conclusion
In conclusion, plastic injection tooling represents a cornerstone of modern manufacturing, enabling the mass production of intricate plastic components across various industries. With precision engineering, advanced materials, and continuous innovation, injection molding drives efficiency, quality, and competitiveness in today's global market. As we embrace future advancements and trends, the role of plastic injection tooling will continue to expand, shaping the way we design, produce, and interact with plastic products in the years to come.
GETTING A QUOTE WITH LK-MOULD IS FREE AND SIMPLE.
FIND MORE OF OUR SERVICES:
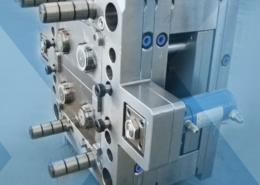
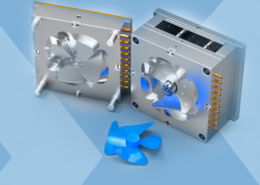
Plastic Molding
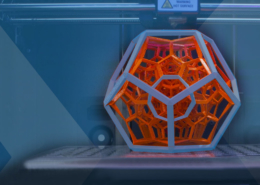
Rapid Prototyping
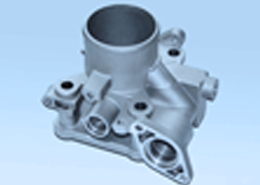
Pressure Die Casting
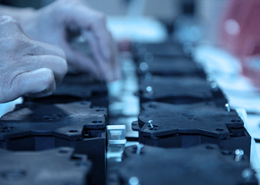
Parts Assembly
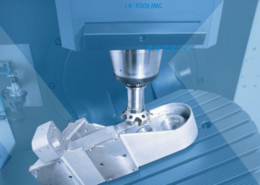