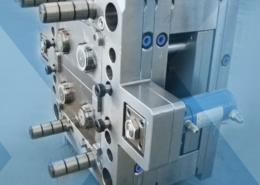
Plastic Molding 1 2: Revolutionizing Manufacturing
Author:gly Date: 2024-06-08
Plastic molding 1 2 represents a pivotal advancement in the realm of manufacturing, reshaping industries and redefining possibilities. This revolutionary process combines cutting-edge technology with innovative techniques to create intricate plastic components with unparalleled precision. Delving into the nuances of plastic molding 1 2 reveals a world of limitless potential and transformative impact.
Revolutionizing Manufacturing
Plastic molding 1 2 stands at the forefront of modern manufacturing, offering unparalleled efficiency, flexibility, and quality. Traditional methods pale in comparison to the precision and speed achieved through this advanced process. By leveraging state-of-the-art machinery and sophisticated design software, manufacturers can seamlessly translate concepts into tangible products, driving innovation and streamlining production cycles.
Plastic molding 1 2 encompasses a diverse range of techniques, including injection molding, blow molding, and compression molding, each tailored to suit specific applications and requirements. This versatility ensures that manufacturers can cater to a myriad of industries, from automotive and aerospace to consumer electronics and medical devices, with utmost precision and efficiency.
Advantages of Plastic Molding 1 2
The advantages of plastic molding 1 2 are manifold, underpinning its widespread adoption and continued prominence in the manufacturing landscape. One of its primary benefits lies in its ability to produce complex geometries with exceptional consistency and repeatability. This not only enhances product performance but also reduces material wastage, optimizing resource utilization and minimizing environmental impact.
Moreover, plastic molding 1 2 facilitates rapid prototyping and iterative design, enabling manufacturers to swiftly iterate concepts and respond to market demands with agility. This iterative approach fosters innovation and creativity, empowering businesses to stay ahead of the curve and maintain a competitive edge in today's dynamic marketplace.
Furthermore, plastic molding 1 2 offers unparalleled cost-effectiveness, thanks to its high production volumes and economies of scale. By leveraging automated processes and advanced materials, manufacturers can achieve significant cost savings without compromising on quality or performance. This makes plastic molding 1 2 an attractive proposition for businesses seeking to enhance their bottom line while delivering superior products to consumers.
Technological Innovations
The evolution of plastic molding 1 2 is intricately intertwined with technological innovations that continue to push the boundaries of what is possible. From advancements in material science to breakthroughs in automation and robotics, each innovation contributes to the refinement and optimization of the plastic molding process.
One notable technological advancement is the integration of artificial intelligence and machine learning algorithms into plastic molding systems. These intelligent systems can analyze vast amounts of data in real-time, optimizing process parameters and identifying potential defects before they occur. This predictive maintenance approach minimizes downtime and maximizes productivity, ensuring uninterrupted operations and consistent product quality.
Additionally, the emergence of 3D printing technologies has revolutionized prototyping and small-batch production, offering unprecedented design freedom and customization options. By harnessing the power of additive manufacturing, manufacturers can rapidly iterate designs and produce bespoke components with minimal lead times, empowering them to cater to niche markets and unique customer preferences with ease.
Future Directions
Looking ahead, the future of plastic molding 1 2 is brimming with possibilities, fueled by ongoing research and development initiatives aimed at enhancing efficiency, sustainability, and scalability. One promising avenue of exploration is the integration of sustainable materials and processes into plastic molding workflows, reducing reliance on fossil fuels and minimizing environmental footprint.
Furthermore, advancements in digital twinning and virtual simulation hold the potential to revolutionize the design and optimization of plastic molding systems, enabling manufacturers to simulate and optimize every aspect of the production process in a virtual environment before physical implementation. This digital-first approach promises to accelerate innovation cycles and drive continuous improvement across the manufacturing ecosystem.
In conclusion, plastic molding 1 2 represents a paradigm shift in manufacturing, offering unparalleled precision, efficiency, and versatility. By embracing technological innovations and adopting a forward-thinking mindset, manufacturers can harness the full potential of this transformative process to drive innovation, enhance competitiveness, and shape the future of industry.
GETTING A QUOTE WITH LK-MOULD IS FREE AND SIMPLE.
FIND MORE OF OUR SERVICES:
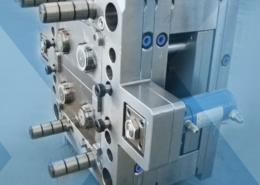
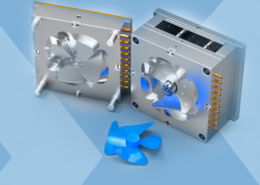
Plastic Molding
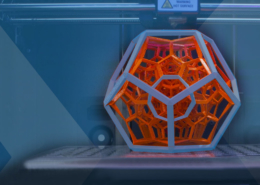
Rapid Prototyping
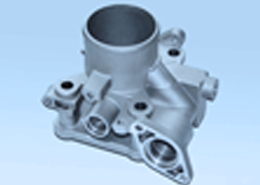
Pressure Die Casting
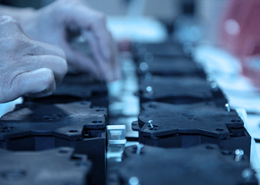
Parts Assembly
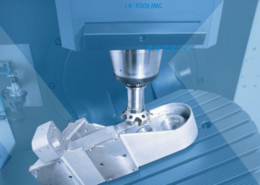