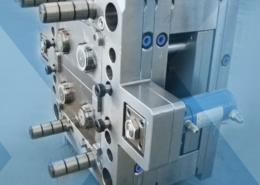
Unveiling the Dynamics of Injection Mold Press
Author:gly Date: 2024-06-08
Introduction
The injection mold press stands as a cornerstone in modern manufacturing, serving as a vital tool for producing intricate plastic components with precision and efficiency. This article aims to explore the intricacies of injection mold press technology, offering insights into its operation, applications, benefits, and future developments.
Understanding Injection Mold Press
The injection mold press, also known as an injection molding machine, is a specialized piece of equipment used to manufacture plastic parts through the injection molding process. This process involves injecting molten plastic material into a mold cavity under high pressure, where it cools and solidifies to form the desired shape. Injection mold presses come in various sizes and configurations, ranging from small desktop machines for prototyping to large industrial-scale presses for mass production.
The injection mold press comprises several key components, including the injection unit, clamping unit, heating and cooling system, and control panel. Each component plays a crucial role in ensuring precise control over the injection molding process, from material melting and injection to mold clamping and part ejection.
Applications Across Industries
Injection mold presses find extensive applications across a wide range of industries, including automotive, aerospace, electronics, medical devices, consumer goods, and packaging. In the automotive sector, injection mold presses are used for producing interior and exterior components such as dashboards, bumpers, and trim panels. Similarly, in the electronics industry, injection mold presses are employed for manufacturing casings, enclosures, and connectors for electronic devices.
Moreover, injection mold presses are utilized in the medical sector for producing components such as syringes, vials, and medical device housings, where precision, cleanliness, and biocompatibility are critical requirements. The versatility of injection molding technology allows manufacturers to produce parts with complex geometries, tight tolerances, and varying material properties to meet the specific needs of each industry.
Advantages and Challenges
Injection mold presses offer several advantages over other manufacturing methods, including high production efficiency, design flexibility, material versatility, and cost-effectiveness for large-scale production runs. Additionally, the ability to utilize a wide range of thermoplastic materials with varying properties allows manufacturers to tailor components to specific performance requirements, such as strength, flexibility, or heat resistance.
However, injection molding also presents challenges such as tooling costs, material selection, and process optimization. Addressing these challenges requires careful consideration of factors such as mold design, material properties, processing parameters, and quality control measures to ensure optimal results.
Technological Advancements and Future Directions
Recent technological advancements in injection mold press technology have focused on enhancing process efficiency, reducing cycle times, and improving part quality. Innovations such as advanced mold designs, hot runner systems, and in-mold decoration techniques have enabled manufacturers to achieve higher productivity and greater design freedom.
Looking ahead, the future of injection mold presses is poised for further innovation and development. Research efforts are underway to explore new materials, optimize processing techniques, and integrate digital technologies such as simulation software and IoT-enabled equipment to enhance process efficiency, reduce waste, and improve product quality.
Conclusion
In conclusion, the injection mold press plays a vital role in modern manufacturing, offering unmatched versatility, precision, and cost-effectiveness in producing a wide range of plastic components across industries. Despite facing challenges, continuous innovation and technological advancements ensure that injection mold presses remain at the forefront of product development and manufacturing. By embracing innovation, collaboration, and continuous improvement, manufacturers can unlock the full potential of injection mold presses and shape the future of manufacturing.
GETTING A QUOTE WITH LK-MOULD IS FREE AND SIMPLE.
FIND MORE OF OUR SERVICES:
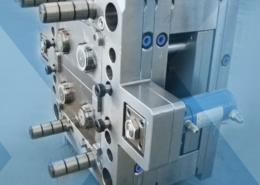
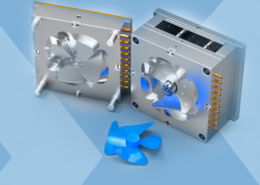
Plastic Molding
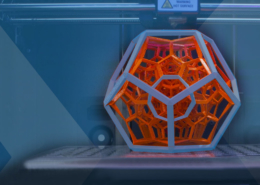
Rapid Prototyping
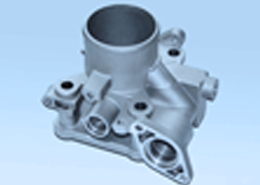
Pressure Die Casting
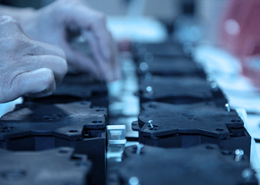
Parts Assembly
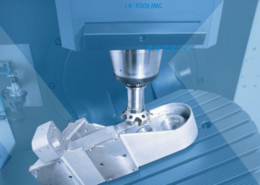