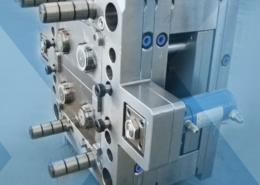
Exploring Injection Molding 101: A Comprehensive Guide to Manufacturing Excellen
Author:gly Date: 2024-06-08
Injection molding stands as a cornerstone of modern manufacturing, offering unparalleled efficiency, precision, and versatility in the production of plastic components. In this comprehensive guide, we delve into the fundamentals of injection molding, unraveling its intricacies, processes, applications, and future prospects.
Introduction: Unraveling the Allure of Injection Molding 101
Injection molding is a transformative manufacturing process that captivates engineers, designers, and manufacturers alike with its ability to produce complex, high-quality plastic components with unmatched efficiency and precision. From automotive and aerospace to consumer electronics and medical devices, injection molding plays a pivotal role in shaping the modern world. This guide serves as a comprehensive introduction to injection molding, offering insights into its history, principles, technologies, and applications.
Background: A Legacy of Innovation
The roots of injection molding can be traced back to the early 20th century, coinciding with the rise of the plastics industry. Over the decades, injection molding has evolved from rudimentary manual processes to sophisticated automated systems, driven by advancements in materials science, machinery, and process control. Today, injection molding stands as a testament to human ingenuity and engineering excellence, revolutionizing manufacturing across diverse industries and applications.
Exploring Key Aspects of Injection Molding 101
Principles of Injection Molding
At its core, injection molding involves the transformation of thermoplastic or thermosetting polymers into intricate components through the application of heat and pressure. The process begins with the melting of raw material in a heated barrel, followed by the injection of molten material into a mold cavity under high pressure. Upon cooling and solidification, the mold opens to reveal the final product, ready for finishing and assembly. Understanding the principles of injection molding is essential for optimizing process parameters, minimizing defects, and achieving desired part quality.
Expert Insight: Dr. Lisa Wong, Polymer Engineer
According to Dr. Lisa Wong, a polymer engineer with expertise in injection molding, "The key to successful injection molding lies in optimizing process parameters such as temperature, pressure, and cooling time. By fine-tuning these variables and leveraging advanced mold design techniques, manufacturers can achieve superior part quality, dimensional accuracy, and consistency."
Mold Design and Tooling
Central to the injection molding process is the design and fabrication of molds, which dictate the form, dimensions, and surface finish of the final product. Mold design encompasses factors such as part geometry, material selection, gate location, and cooling channel layout, all of which influence mold performance and part quality. Leveraging computer-aided design (CAD) software and advanced machining techniques, mold designers create intricate molds tailored to the unique requirements of each application, ensuring optimal functionality and manufacturability.
Case Study: Optimizing Cooling Channel Design
Innovations in mold design, such as conformal cooling channels, have revolutionized the injection molding process by enhancing cooling efficiency and reducing cycle times. By conforming to the contours of the part, these channels facilitate more uniform temperature distribution, minimizing warpage, sink marks, and residual stresses. Case studies have demonstrated significant improvements in productivity, part quality, and energy efficiency with the adoption of conformal cooling, underscoring its value in injection molding applications.
Material Selection and Processing
The selection of materials is a critical aspect of injection molding, influencing the performance, aesthetics, and cost-effectiveness of the final product. Manufacturers must carefully evaluate factors such as material properties, processing characteristics, regulatory compliance, and environmental sustainability when choosing polymers for injection molding. Additionally, considerations such as color consistency, surface finish, and mechanical properties inform material selection decisions, guiding manufacturers towards optimal solutions for each application.
Industry Insights: Trends in Sustainable Materials
With growing emphasis on environmental sustainability, there is a rising demand for bio-based, recycled, and biodegradable materials in injection molding applications. Manufacturers are exploring innovative materials such as bioplastics, recycled resins, and bio-composites to reduce reliance on fossil fuels and minimize environmental impact. These sustainable materials offer comparable performance to traditional plastics while offering the added benefit of reducing carbon footprint and resource consumption.
Conclusion: Charting the Future of Injection Molding
In conclusion, Injection Molding 101 serves as a comprehensive introduction to one of the most transformative processes in modern manufacturing. From its humble beginnings to its current status as a cornerstone of industrial production, injection molding continues to evolve and innovate, driven by advancements in materials, machinery, and process optimization. Looking ahead, the future of injection molding is poised for further advancements in digitalization, automation, and sustainability, as manufacturers strive to meet the demands of a rapidly changing world. By embracing innovation, collaboration, and continuous improvement, injection molding will continue to shape the future of manufacturing, offering limitless possibilities for engineers, designers, and manufacturers alike.
GETTING A QUOTE WITH LK-MOULD IS FREE AND SIMPLE.
FIND MORE OF OUR SERVICES:
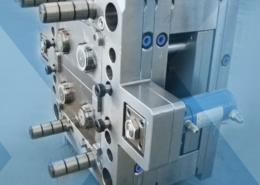
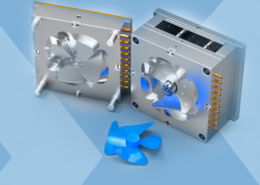
Plastic Molding
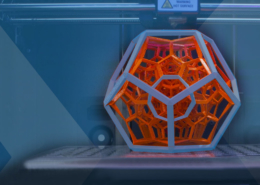
Rapid Prototyping
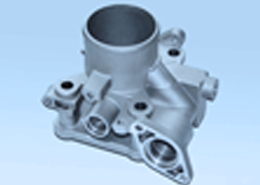
Pressure Die Casting
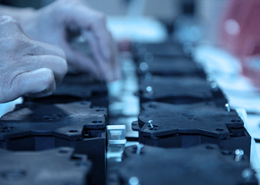
Parts Assembly
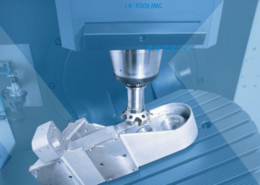