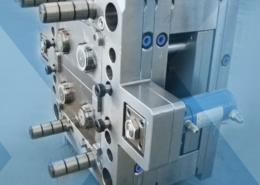
Polycarbonate Injection Molding: Revolutionizing Manufacturing
Author:gly Date: 2024-06-08
Polycarbonate injection molding stands as a pinnacle of modern manufacturing processes, revolutionizing industries with its versatility, durability, and efficiency. As a method of choice for producing intricate and high-quality plastic parts, polycarbonate injection molding has garnered immense interest from engineers, designers, and manufacturers worldwide. This article delves into the intricacies of polycarbonate injection molding, exploring its various facets, applications, and future prospects.
The Essence of Polycarbonate Injection Molding
Polycarbonate injection molding, at its core, embodies the fusion of advanced engineering techniques and polymer science. It entails the precise injection of molten polycarbonate material into a mold cavity, where it solidifies to form the desired product. This process offers unparalleled design freedom, enabling the creation of complex geometries with exceptional precision and surface finish.
Material Properties
Polycarbonate, known for its exceptional impact resistance, optical clarity, and thermal stability, serves as the primary material for injection molding. Its unique combination of properties makes it ideal for a wide range of applications, including automotive components, electronics housings, medical devices, and consumer goods.
Strength and Durability
Polycarbonate exhibits outstanding mechanical strength, allowing it to withstand impact and fatigue over prolonged usage. This inherent toughness makes it suitable for applications where reliability and longevity are paramount, such as safety helmets and protective eyewear.
Optical Clarity
The optical clarity of polycarbonate rivals that of glass, making it a preferred choice for applications requiring transparent or translucent components. Its excellent light transmission properties, coupled with high refractive index, render it indispensable in automotive lighting, LED optics, and optical lenses.
Thermal Stability
With a high heat deflection temperature and excellent dimensional stability, polycarbonate can withstand elevated temperatures without significant deformation or degradation. This thermal resilience makes it suitable for applications subjected to thermal cycling and exposure to harsh environments.
Process Optimization
Achieving optimal results in polycarbonate injection molding necessitates meticulous attention to process parameters, mold design, and material selection. By fine-tuning these variables, manufacturers can enhance productivity, minimize defects, and ensure consistent part quality.
Injection Molding Parameters
Key parameters such as melt temperature, injection speed, and packing pressure play a crucial role in determining the final properties of the molded part. Precise control of these parameters is essential to achieve uniform filling, minimize shrinkage, and mitigate defects such as warpage and sink marks.
Mold Design Considerations
The design of the mold significantly influences the moldability and performance of polycarbonate parts. Factors such as gate location, cooling channel layout, and venting provisions must be carefully optimized to facilitate proper filling, cooling, and ejection of the molded components.
Material Selection Criteria
Choosing the appropriate grade of polycarbonate resin is paramount to meeting the functional and aesthetic requirements of the final product. Factors such as viscosity, flow characteristics, and additives influence the processability and performance of the material, necessitating thorough material testing and qualification.
Applications Across Industries
The versatility of polycarbonate injection molding transcends traditional boundaries, finding applications in diverse industries ranging from automotive and aerospace to healthcare and consumer electronics.
Automotive Components
In the automotive sector, polycarbonate injection molding is instrumental in producing lightweight, yet durable components such as interior trim panels, exterior body parts, and lighting assemblies. Its ability to integrate complex features and incorporate decorative finishes enables automotive manufacturers to achieve design differentiation while meeting stringent performance standards.
Electronics Enclosures
For electronic devices requiring robust protection against environmental factors and mechanical stress, polycarbonate injection molding offers an ideal solution. Enclosures, housings, and connectors molded from polycarbonate provide excellent impact resistance, electromagnetic shielding, and dimensional stability, ensuring the integrity and reliability of sensitive electronic components.
Medical Devices
In the healthcare industry, the biocompatibility, sterilizability, and transparency of polycarbonate make it a preferred choice for medical device applications. From surgical instruments and diagnostic equipment to drug delivery devices and laboratory consumables, polycarbonate injection-molded components play a critical role in advancing patient care and medical innovation.
Future Prospects and Innovations
Looking ahead, advancements in material science, process technology, and design methodologies promise to further enhance the capabilities and applications of polycarbonate injection molding. Novel additives, nanocomposites, and multi-material molding techniques are poised to unlock new possibilities in terms of performance, functionality, and sustainability.
Sustainable Solutions
As the demand for environmentally friendly materials and manufacturing processes continues to rise, efforts are underway to develop sustainable alternatives to conventional polycarbonate resins. Bio-based polymers, recycled feedstocks, and eco-friendly additives offer promising avenues for reducing the environmental footprint of polycarbonate injection molding while maintaining performance and functionality.
Additive Manufacturing Integration
The integration of additive manufacturing techniques such as 3D printing with traditional injection molding processes holds immense potential for accelerating product development cycles and enabling on-demand manufacturing. Hybrid approaches combining the design flexibility of additive manufacturing with the scalability and efficiency of injection molding are poised to revolutionize the production of customized, high-performance parts.
Conclusion
In conclusion, polycarbonate injection molding stands as a cornerstone of modern manufacturing, embodying innovation, efficiency, and versatility. From its exceptional material properties to its diverse applications across industries, polycarbonate injection molding continues to redefine the boundaries of what's possible in plastic part production. By embracing emerging technologies and sustainable practices, the future of polycarbonate injection molding remains bright, promising continued advancements and opportunities for growth and innovation.
GETTING A QUOTE WITH LK-MOULD IS FREE AND SIMPLE.
FIND MORE OF OUR SERVICES:
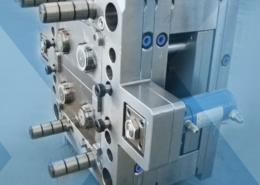
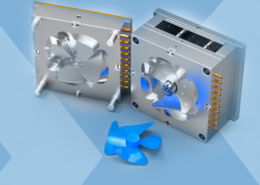
Plastic Molding
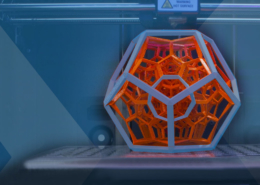
Rapid Prototyping
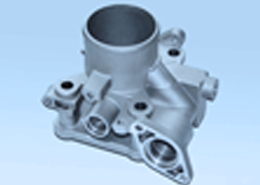
Pressure Die Casting
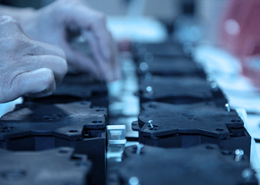
Parts Assembly
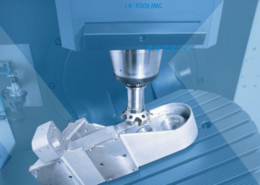