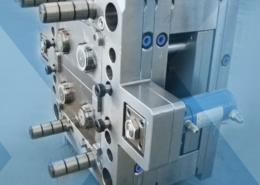
Exploring Polycarbonate Injection Molding: Innovations and Applications
Author:gly Date: 2024-06-08
Introduction
Polycarbonate injection molding stands at the forefront of modern manufacturing, revolutionizing the production of a wide array of products across industries. With its exceptional properties and versatility, polycarbonate injection has garnered significant interest among engineers, designers, and manufacturers worldwide. This article aims to delve into the intricacies of polycarbonate injection molding, exploring its various aspects, innovations, and applications.
Material Properties and Composition
Polycarbonate, a thermoplastic polymer, boasts remarkable properties conducive to injection molding processes. Its molecular structure comprises carbonate groups, contributing to its high impact resistance, transparency, and heat tolerance. Additionally, the inclusion of bisphenol A enhances its rigidity and dimensional stability, making it an ideal material for intricate molding applications.
The injection molding process involves the heating of polycarbonate pellets to their melting point, followed by the injection of the molten material into a mold cavity. Rapid cooling solidifies the material, resulting in the desired shape. Polycarbonate's low viscosity when molten facilitates intricate mold designs, ensuring the production of precise and intricate components.
Furthermore, the ability to incorporate additives such as UV stabilizers and flame retardants enhances the material's performance, extending its applications to diverse industries ranging from automotive to electronics.
Advancements in Manufacturing Techniques
Recent advancements in manufacturing techniques have propelled polycarbonate injection molding to new heights of precision and efficiency. The integration of computer-aided design (CAD) and computer-aided manufacturing (CAM) software enables the creation of complex mold designs with unparalleled accuracy.
Moreover, the advent of multi-cavity molds and hot runner systems enhances productivity by allowing simultaneous production of multiple parts and reducing cycle times. Furthermore, innovations in mold cooling technologies ensure uniform cooling rates, minimizing warpage and improving dimensional stability.
Applications Across Industries
Polycarbonate injection molding finds extensive applications across a myriad of industries, owing to its exceptional properties and versatility. In the automotive sector, it is utilized for the production of exterior components, interior trims, and lighting assemblies, thanks to its high impact resistance and heat tolerance.
In the electronics industry, polycarbonate is preferred for the manufacturing of housings, enclosures, and connectors, offering excellent electrical insulation properties and dimensional stability. Furthermore, its optical clarity makes it an ideal choice for the production of lenses and display screens in consumer electronics.
Additionally, the medical sector utilizes polycarbonate for the fabrication of surgical instruments, equipment housings, and medical device components, owing to its biocompatibility and sterilizability.
Sustainability and Environmental Impact
Despite its myriad benefits, concerns regarding the environmental impact of polycarbonate injection molding have emerged in recent years. The use of bisphenol A (BPA) in polycarbonate production has raised questions regarding its potential health hazards and environmental persistence.
To address these concerns, manufacturers are exploring alternative formulations such as BPA-free polycarbonates and bio-based polymers derived from renewable sources. Additionally, efforts to optimize manufacturing processes to minimize waste generation and energy consumption are underway, promoting sustainability across the industry.
Conclusion
In conclusion, polycarbonate injection molding represents a cornerstone of modern manufacturing, offering unparalleled versatility, precision, and performance. From automotive and electronics to medical applications, polycarbonate continues to drive innovation and advancement across industries. However, as the industry evolves, it is imperative to address environmental concerns and embrace sustainable practices to ensure a greener and more sustainable future for polycarbonate injection molding.
Through continuous research, innovation, and collaboration, the potential of polycarbonate injection molding remains boundless, promising exciting possibilities for the future of manufacturing.
GETTING A QUOTE WITH LK-MOULD IS FREE AND SIMPLE.
FIND MORE OF OUR SERVICES:
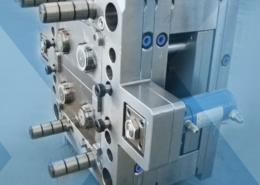
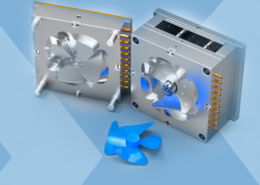
Plastic Molding
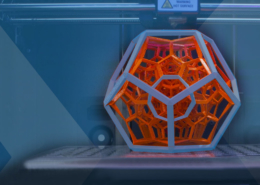
Rapid Prototyping
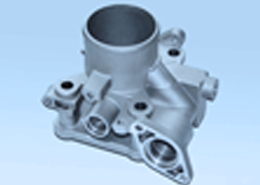
Pressure Die Casting
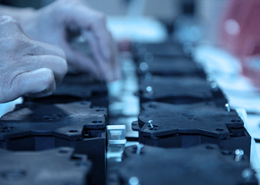
Parts Assembly
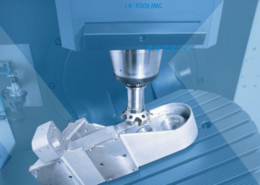